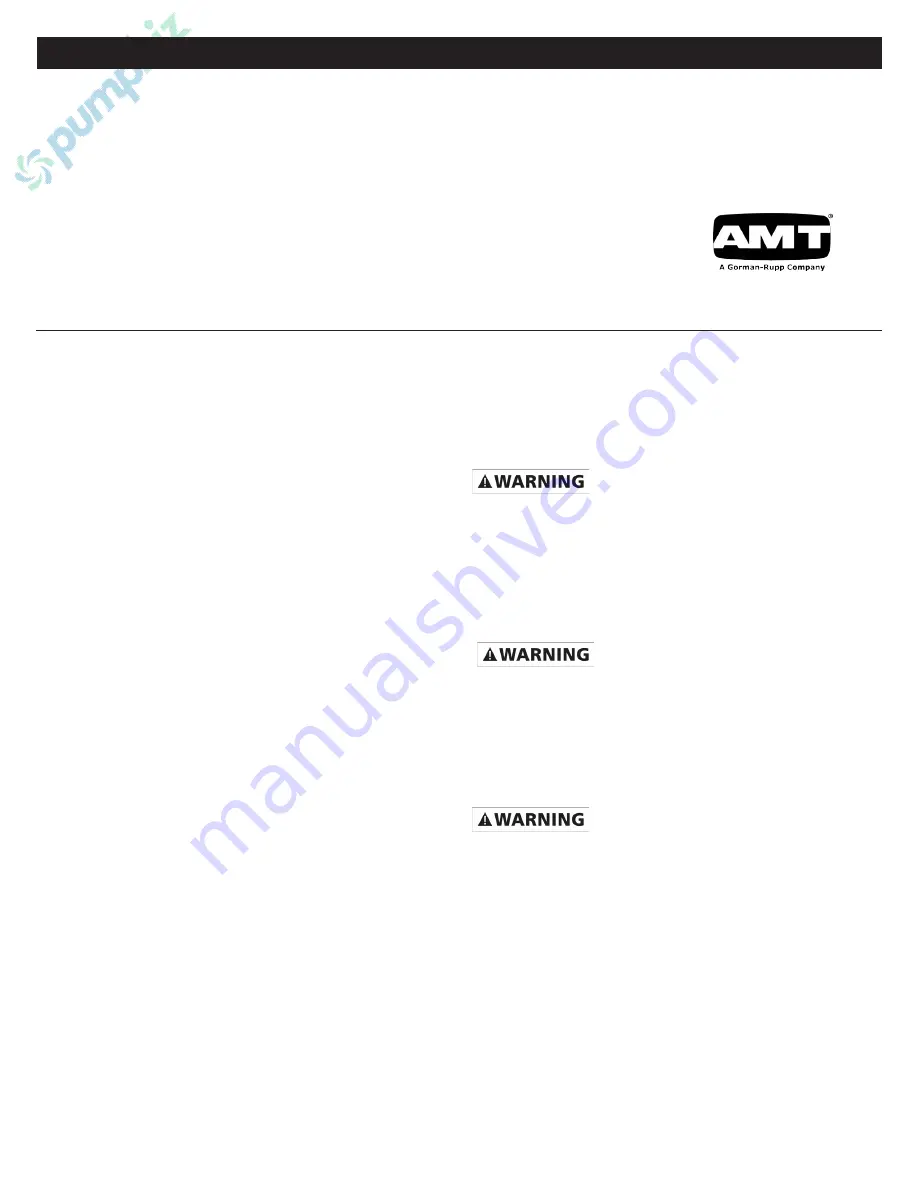
Specifications Information and Repair Parts Manual
489G
489G-250-00
1
4/2016
Please read and save this Repair Parts Manual. Read this manual and the General Operating Instructions carefully before attempting to assemble, install, operate
or maintain the product described. Protect yourself and others by observing all safety information. The Safety Instructions are contained in the General Operating
Instructions. Failure to comply with the safety instructions accompanying this product could result in personal injury and/or property damage! Retain instructions
for future reference. AMT reserves the right to discontinue any model or change specifications at any time without incurring any obligation.
©2016 AMT Pump Company, A Subsidiary of The Gorman-Rupp Company, All Rights Reserved.
Periodic maintenance and inspection is required on all pumps to ensure proper operation. Unit must be clear of debris and sediment. Inspect for leaks and loose bolts. Failure to do so
voids warranty.
High Head Centrifugal Pumps
12-Volt DC Models
Refer to pump manual 1808-634-00 for General Operating and Safety Instructions.
DESCRIPTION
These pumps are non self-priming units designed for use where higher heads are needed to handle liquid transfer, heating and cooling applications, where no
suction lift is required. All models feature high-efficiency closed impellers with 3450 RPM, 56J frame, 12 VDC motors. The discharge port on all models can
be rotated in 90º increments to accommodate specific applications. Casing working pressure to 150 psi (1034 kPa). These are manual units, no controls are
supplied. Check motor wiring before putting unit into operation (see motor nameplate for specific wiring diagrams). All units are for use with non-flammable, non-
abrasive liquids compatible with pump component materials
CAST IRON UNITS
Pump construction is cast iron casing and adapter. Cast 316
stainless steel impeller. Buna N type 21 mechanical shaft seal with
carbon and ceramic wear faces. O-ring casing seal. Handles liquids
from 40º to 180º F (4º to 82º C).
BRONZE UNITS
Pump construction is cast bronze casing and adapter. Cast 316
stainless steel impeller. Viton type 21 mechanical shaft seal with
carbon and ceramic wear faces. O-ring casing seal. Handles liquids
from 40º to 200º F (4º to 93º C).
316 STAINLESS STEEL UNITS
Pump construction is cast 316 stainless steel casing, adapter,
and impeller. Viton type 21 mechanical shaft seal with carbon and
ceramic wear faces. O-ring casing seal. Handles liquids from 40º to
200º F (4º to 93º C).
General Safety
Information for 12 Volt DC Power
1. When connecting power leads, follow this order:
a. Connect POSITIVE or PLUS(+) terminal on motor to supply
lead first.
b. Connect NEGATIVE or MINUS(-) terminal last.
c. When DISCONNECTING – Disconnect NEGATIVE (-) first,
then disconnect POSITIVE (+) lead from motor terminal.
2. When attaching line leads to motor or battery/power supply
terminals, be sure that surrounding area is adequately ventilated
to prevent an explosion or fire from explosive or flammable
vapors that may be present
Batteries emit hydrogen gas which is explosive. Avoid smoking,
sparks or open flame anywhere in vicinity of battery. Explosion
from battery can cause blindness. Shield eyes when working
near any battery.
Batteries contain sulfuric acid. In case of contact with eyes, skin
or clothing, flush immediately with large amount of water, get
medical attention.
3. When running leads, be sure wire gage is adequately sized and
all electrical connections are properly insulated and enclosed.
Do not add acid or electrolyte to battery being used – add only
water. Consult battery manufacturers for any additional safety
instructions.
4. Motor must be located out
of the weather with access to adequate
ventilation for cooling. Motor is not waterproof!
5. All wiring should be performed by a qualified electrician.
Maintenance
Make certain that the unit is disconnected from the power source
before attempting to service or remove any components!
SHAFT SEAL REPLACEMENT
Refer to Figures Nos. 2 and 3.
REMOVAL OF OLD SEAL
IMPORTANT:
Always replace both seal seat (Ref. No. 5) and seal
head (Ref. No. 6) to insure proper mating of components! Also,
impeller seal (Ref. No. 9) should be replaced anytime impeller
fastener (Ref. No. 10) has been removed.
1.
Remove fasteners (Ref. No. 3) connecting casing (Ref. No. 12)
to adapter (Ref. No. 4).