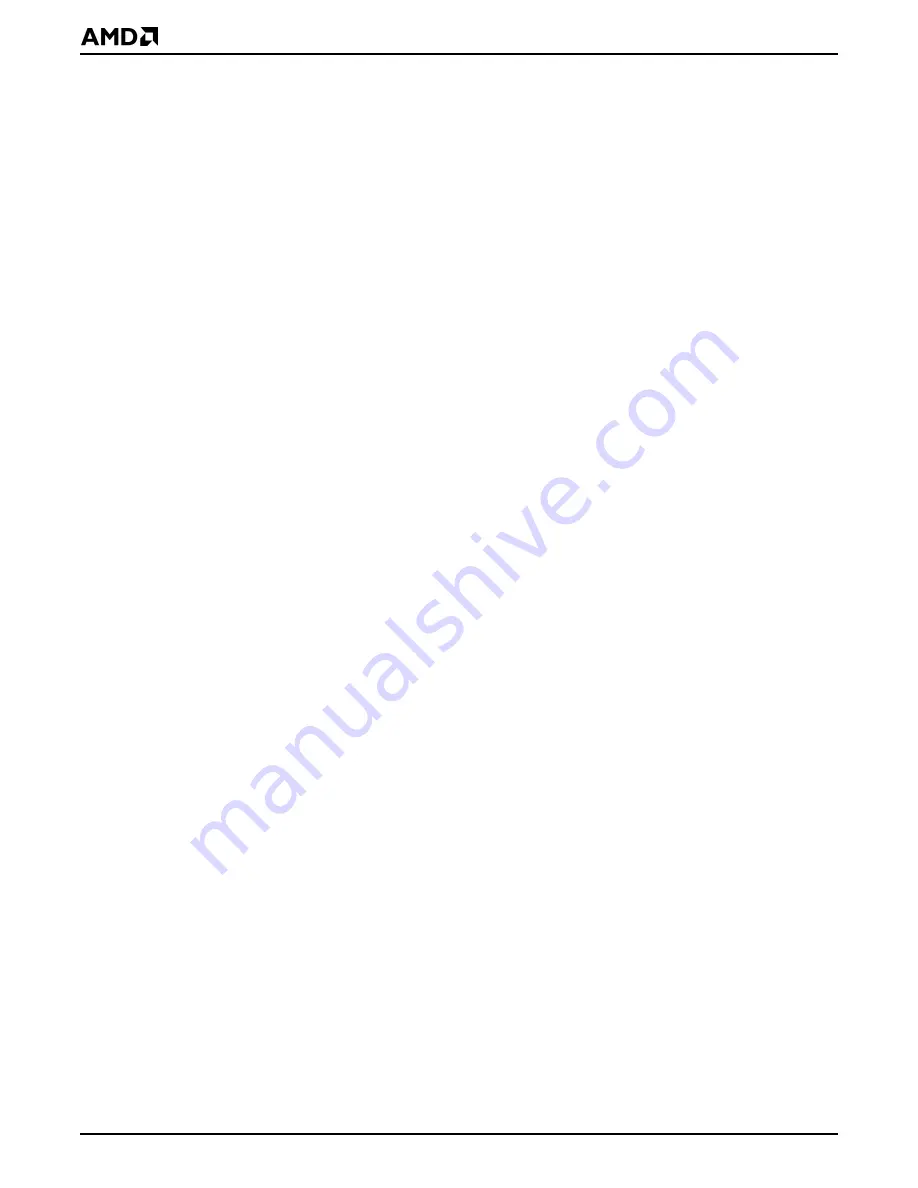
Clock Generation and Control
5-4
Élan™SC520 Microcontroller User’s Manual
5.3.1
Clock Pin Loading
Clock pins are designed to either source or sink 24 mA. The maximum amount of capacitive
load that can be placed on a clock pin is determined by the required rise/fall times.
Use the following equation to determine the maximum capacitive loading.
C = I/(dV/dt)
where:
I = Current
dV = Voltage change
dt = Time change
As an example, suppose that the system requires a rise/fall time of 1 ns, with a voltage
swing of 2.5 V. Then, the maximum capacitive load is:
C
max
= 24 mA/(2.5 V/1 ns) = 9.6 pF
Derating curves for the device are provided in the
Élan™SC520 Microcontroller Data Sheet,
order #22003.
5.3.2
Selecting a Crystal
The accuracy of the real-time clock (RTC) depends on several factors relating to crystal
selection and board design. A clock timing budget determines the clock accuracy. The
designer should determine the timing budget before selecting a crystal.
There are four major contributors to a clock timing budget.
■
Frequency Tolerance—This is the crystal calibration frequency. It states how far off the
actual crystal frequency is from the nominal frequency. For a typical 32.768-kHz crystal
(watch crystal), the frequency tolerance is ± 20 parts per million (ppm). Frequency
tolerance is specified at room temperature.
■
Frequency Stability—This parameter is a measure of how much the crystal resonant
frequency is influenced by operating temperature. For watch crystals, typical numbers
are around –30 ppm over the temperature range.
■
Aging—This parameter is how much the crystal resonant frequency changes with time.
Typical aging numbers are ± 3 ppm per year.
■
Load Capacitance—The crystal is calibrated with a specific load capacitance. If the
system load capacitance does not equal the crystal load capacitance, a timing error is
introduced. The timing error is calculated by the following equation.
Error = {[1 + C1/(CL
xtal
+Co)]
1/2
– [1 +C1/(CL
system
+Co)]
1/2
}/ [1 + C1/(CL
xtal
+Co)]
1/2
where:
C1 is the crystal motional capacitance
Co is the crystal static capacitance
CL
xtal
is the crystal load capacitance
CL
system
is the system load capacitance
For the error in ppm, multiply Error by 10
6
.
Once the complete timing error has been calculated by adding all of the errors together,
compare it to the initial timing budget. Table 5-3 provides a convenient translation of
ppm to seconds per month.
Содержание Elan SC520
Страница 1: ...lan SC520 Microcontroller User s Manual Order 22004A...
Страница 4: ...iv lan SC520 Microcontroller User s Manual...
Страница 28: ...Introduction xxviii lan SC520 Microcontroller User s Manual...
Страница 42: ...Architectural Overview 1 14 lan SC520 Microcontroller User s Manual...
Страница 78: ...System Initialization 3 22 lan SC520 Microcontroller User s Manual...
Страница 108: ...Clock Generation and Control 5 10 lan SC520 Microcontroller User s Manual...
Страница 118: ...Reset Generation 6 10 lan SC520 Microcontroller User s Manual...
Страница 148: ...System Arbitration 8 24 lan SC520 Microcontroller User s Manual...
Страница 214: ...SDRAM Controller 10 36 lan SC520 Microcontroller User s Manual...
Страница 230: ...Write Buffer and Read Buffer 11 16 lan SC520 Microcontroller User s Manual...
Страница 288: ...GP Bus DMA Controller 14 22 lan SC520 Microcontroller User s Manual...
Страница 316: ...Programmable Interval Timer 16 8 lan SC520 Microcontroller User s Manual...
Страница 328: ...Software Timer 18 4 lan SC520 Microcontroller User s Manual...
Страница 346: ...Real Time Clock 20 12 lan SC520 Microcontroller User s Manual...
Страница 360: ...UART Serial Ports 21 14 lan SC520 Microcontroller User s Manual...
Страница 414: ...AMDebug Technology 26 8 lan SC520 Microcontroller User s Manual...