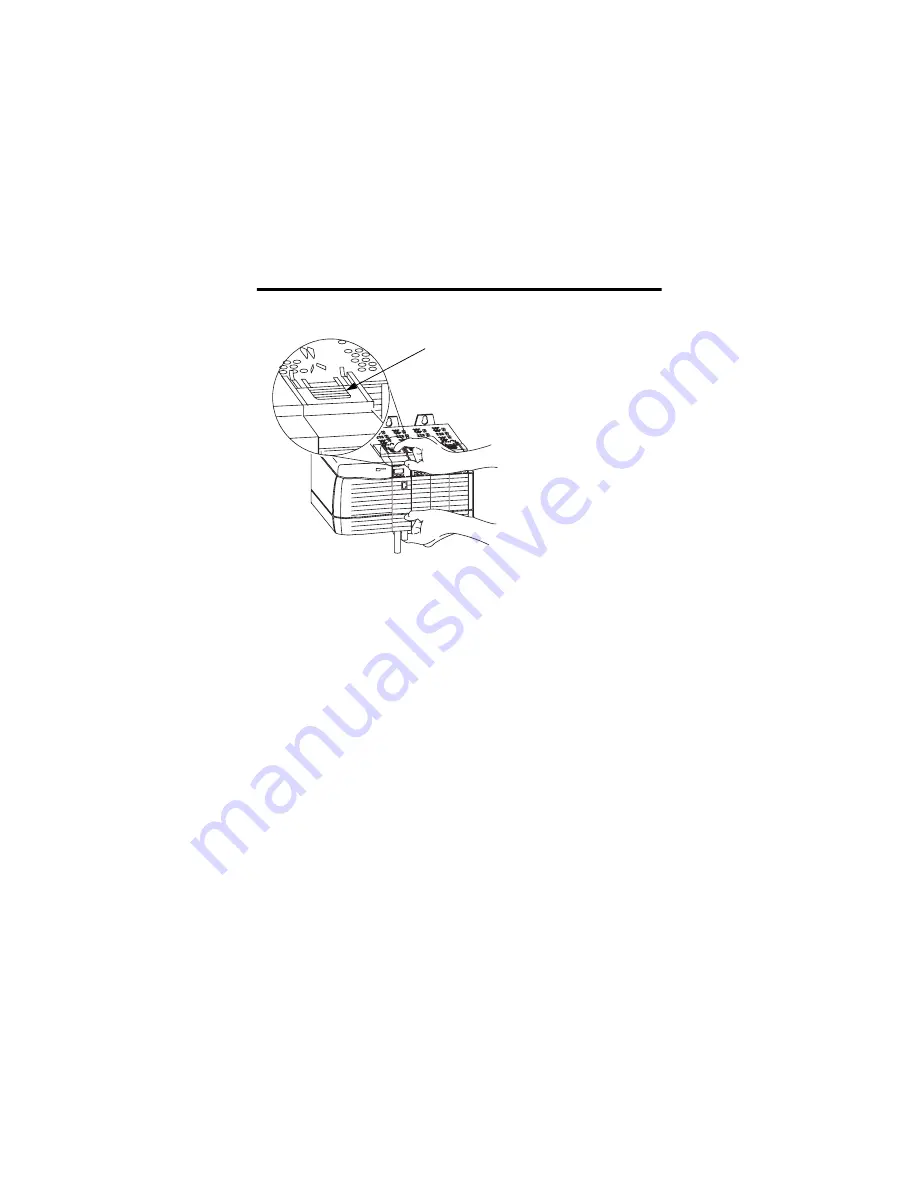
16
ControlLogix ControlNet Interface Module
Publication
1756-IN604A-EN-P - February 2006
Remove the Module
If you are replacing an existing module with an identical one, and you want to
resume identical system operation, you must install the new module with the
same ControlNet address in the same slot.
Upper Tab
Push on the upper and lower tabs
to disengage them. Then slide
the module out of the chassis.