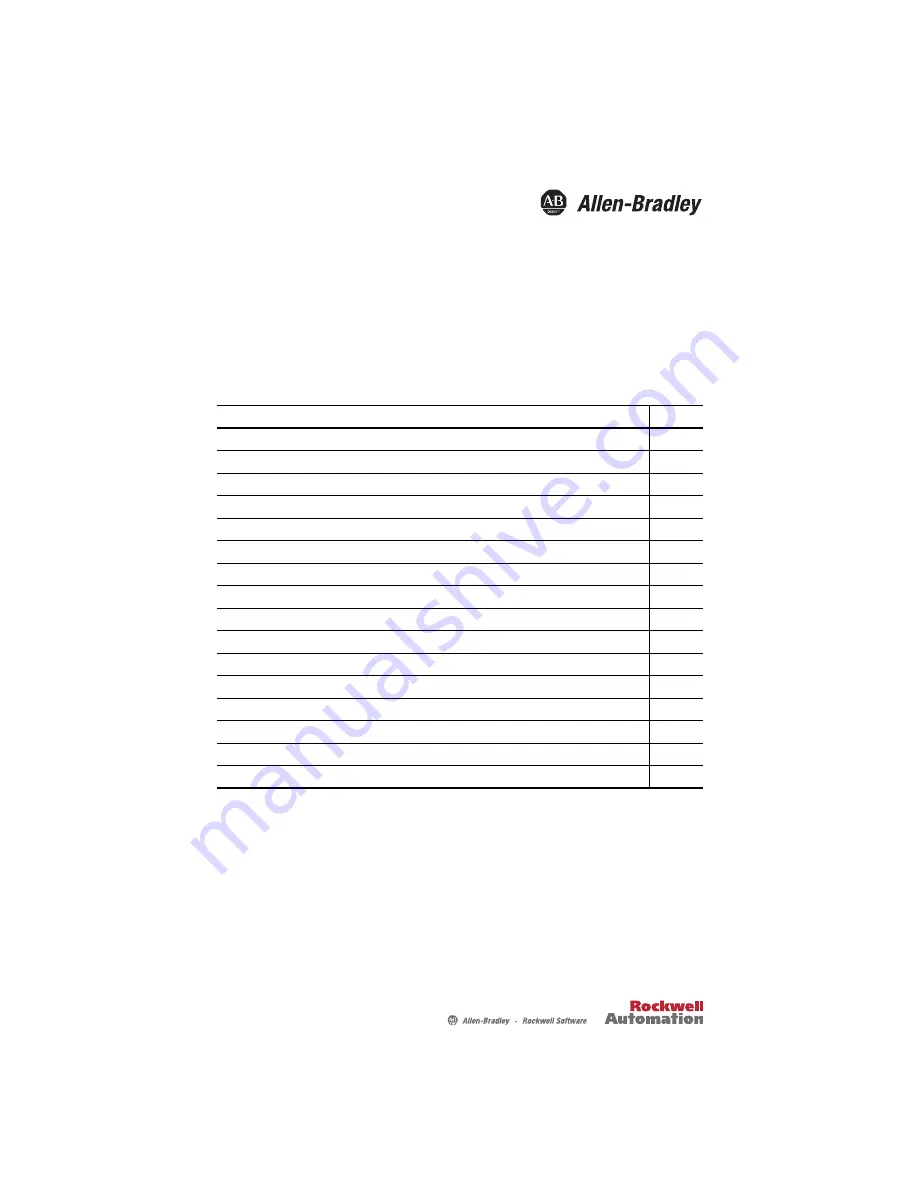
Installation Instructions
Compact I/O High-speed Counter
Module
Catalog Number 1769-HSC
About the Module
The 1769-HSC module has six differential DC inputs that can be used as two to four high-speed
counters. The module has 4 sourcing DC outputs and 12 additional ‘virtual’ outputs. The
counters provide accumulated pulse counts to the input array of the module and can cause
onboard outputs to react to input conditions at high speed.
The module is compatible with CompactLogix controllers, MicroLogix 1500 controllers , and
the 1769-ADN DeviceNet adapter.
Topic
Page
North American Hazardous Location Approval