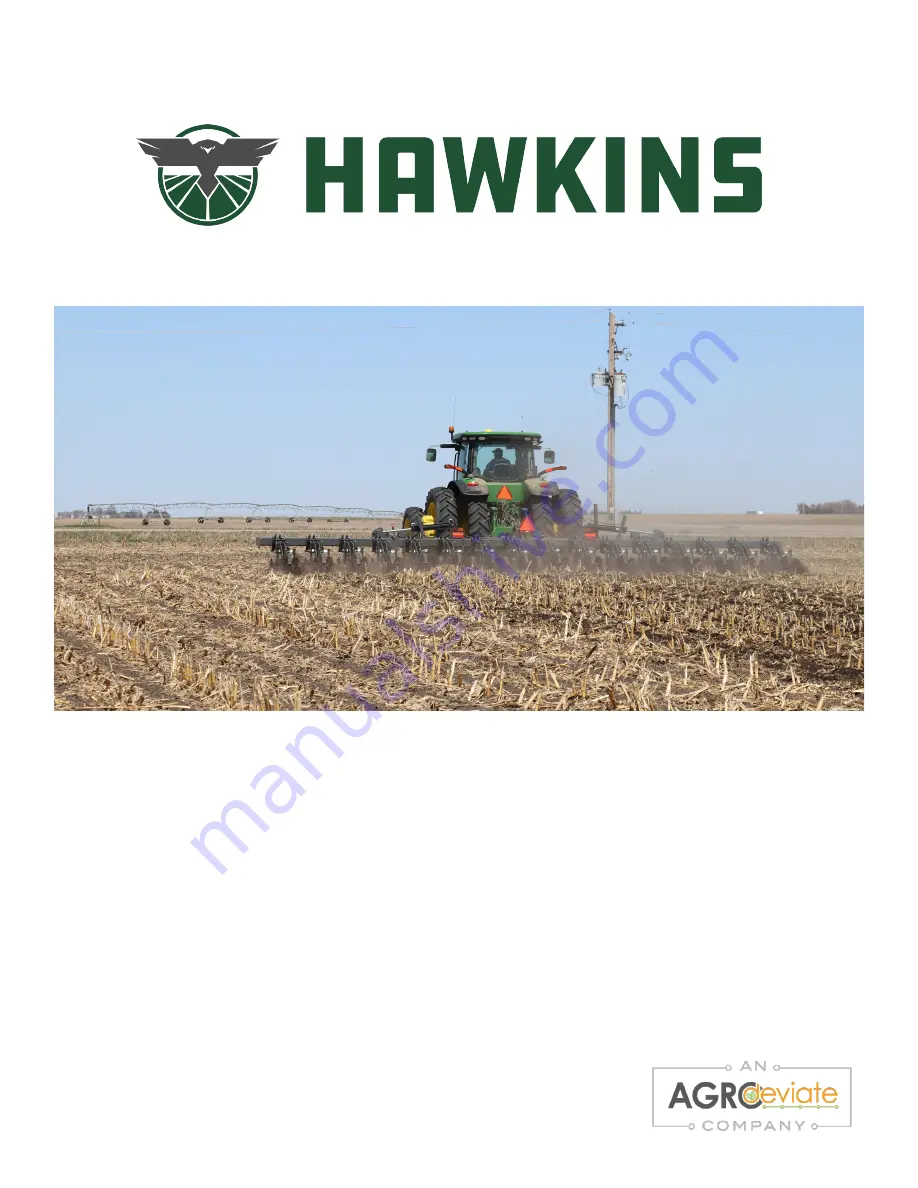
308.708.8185 | [email protected]| Rev. 01/21 | Part Number 123013
STRIPCAT™
OWNER’s Manual
R
evised 01.21
Содержание Hawkins StripCat
Страница 1: ...308 708 8185 Hawkins HawkinsAg com Rev 01 21 Part Number 123013 STRIPCAT OWNER s Manual Revised 01 21 ...
Страница 6: ......
Страница 11: ......
Страница 18: ......
Страница 27: ......
Страница 58: ......
Страница 62: ......
Страница 69: ......
Страница 98: ...308 708 8185 Hawkins HawkinsAg com Rev 12 20 308 708 8185 HawkinsAg com 2120 4th AVE Holdrege NE 68949 ...