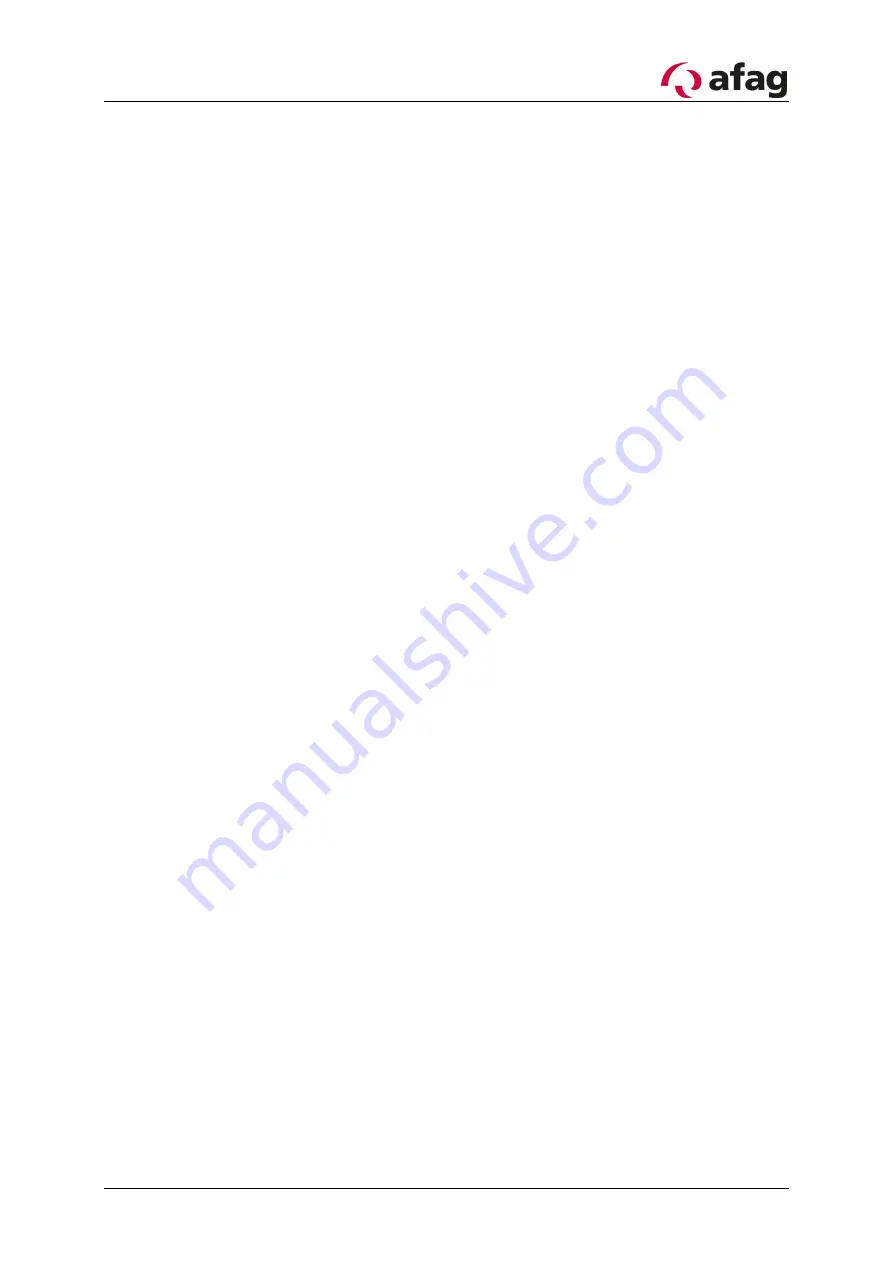
R05.1
12/02/2020
Page 11
For the operation, the linear feeder must always be mounted on a sufficiently dimen-
sioned (mass) subframe. The subsurface should be vibration-resistant (plate or block
design) in order to absorb the vibration forces.
Self-supporting profiles must be reinforced by a base plate on which the linear feeder is
attached. A steel plate should be used which is at least 20mm thick and more than
120mm wide.
Suitable substructures are to be provided for the height adjustment. Suitable afag stand-
ard parts are available for complete station extensions in combination with afag helical
conveyors.
During the assembly of the linear feeder make sure that the base is horizontal or slightly
inclined in the direction of transport (1.5-2°).
3.3
Mounting of the linear track
In order to achieve optimum transport speed, the following basic requirements must be
fulfilled:
1.
The rail and LF-support must match each other
2.
The structure of the rail must transmit the vibration ideally. (rail-profile standing,
not flat)
3.
The length of the conveyor rail must not exceed the maximum permissible length.
4.
Depending on the material to be conveyed, a maximum of two additional support
springs is necessary.
5.
The weight of the rail (including parts) must not exceed the weight limit.
(see 2.3
The rail is to be aligned approximately symmetrical to the intermediate plate of the linear
feeder. The conveying speed can be increased by tilting the rail in the direction of travel
by 1.5
– 2°.
All LF models feature four boreholes on the upper side of the drive to connect the con-
veying rail to the vibratory conveyor.
(See Chapter 2.3 Technical data)