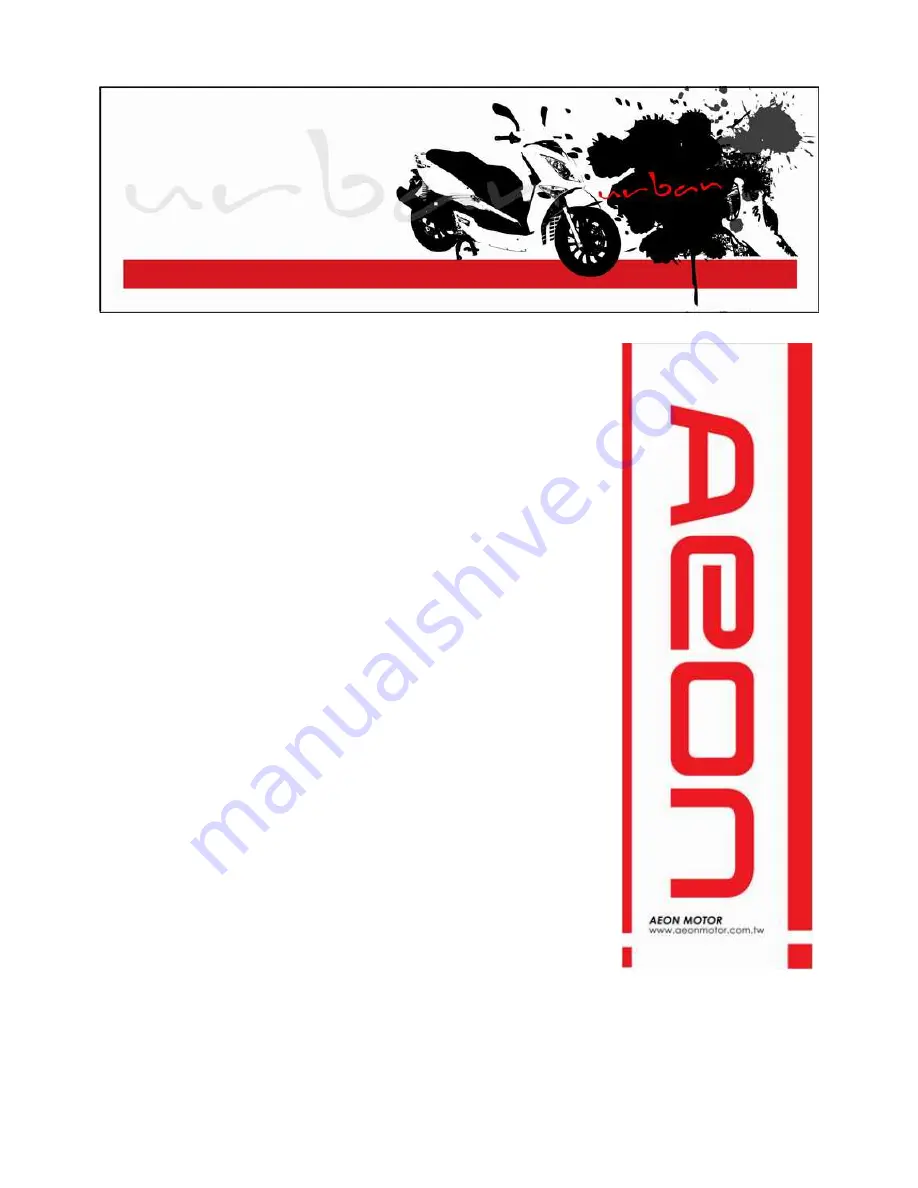
GENERAL INFORMATION
1-1
2010 URBAN 350 EFI
SERVICE MANUAL
FOREWORD
This service manual is designed primarily for use by certified Aeon Master Service
Dealer technicians in a properly equipped shop and should be kept available for
reference. All references to left and right side of the vehicle are from the operator's
perspective when seated in a normal riding position.
Some procedures outlined in this manual require a sound knowledge of mechanical
theory, tool use, and shop procedures in order to perform the work safely and
correctly. Technicians should read the text and be familiar with service procedures
before starting the work. Certain procedures require the use of special tools. Use
only the proper tools as specified.
Содержание 350cc
Страница 11: ...GENERAL INFORMATION 1 11...
Страница 32: ...CVT SYSTEM 3 32...
Страница 43: ...ENGINE 4 43 ENGINE SERVICE ENGINE EXPLODED VIEW 1...
Страница 44: ...ENGINE 4 44 ENGINE EXPLODED VIEW 2...
Страница 45: ...ENGINE 4 45...
Страница 46: ...ENGINE 4 46 ENGINE COOLING SYSTEM COOLING SYSTEM EXPLODED VIEW...
Страница 53: ...ENGINE 4 53 TOP END DISASSEMBLY...
Страница 60: ...ENGINE 4 60...
Страница 74: ...ENGINE 4 74...
Страница 103: ...ELECTRONIC FUEL INJECTION 5 103 FUELTANK...
Страница 132: ...ELECTRONIC FUEL INJECTION 5 132 3 Select file smd format 4 Press Convert 5 Press Confirm after transformation completed...
Страница 168: ...ELECTRICAL 7 168...
Страница 171: ...ELECTRICAL 7 171...
Страница 191: ...ELECTRICAL 7 191...
Страница 192: ...ELECTRICAL 7 192...