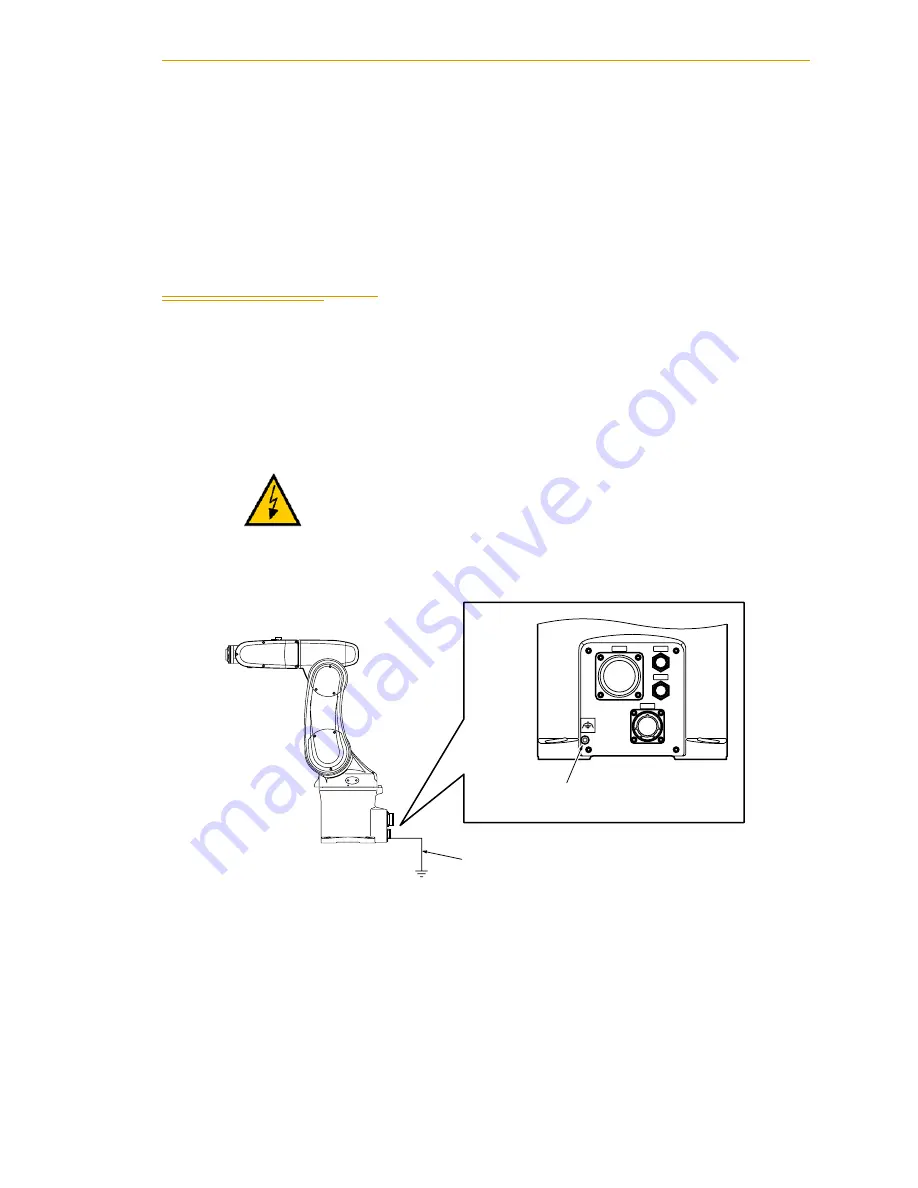
Grounding the Robot
AdeptViper s650/s850 Robot User’s Guide, Rev A
31
5. Set the robot unit into place on the robot mount. When transporting the robot
unit, follow the instructions given in
6. Secure the robot unit to the mount with four bolts and plain washers.
• Bolt: M10 x 30 mm (strength class: 12.9)
• Tightening torque: 70 +/- 14 Nm
3.5
Grounding the Robot
Ground the grounding terminal of the robot unit with a wire of 12 AWG or more. Ground
resistance must be less than 100 milliohms.
NOTE:
Use a dedicated grounding wire and grounding electrode. Do not
share them with any other electric power or power equipment such as a
welder.
Figure 3-3. Ground Point on Robot
WARNING:
Wiring must be performed by authorized or
certified personnel. Failure to observe this caution may
result in fire or electric shock.
C N 2 2
C N 2 0
A I R 1
A I R 2
Grounding terminal (M5)
12 AWG or more
Содержание AdeptViper s650
Страница 1: ...AdeptViper s650 s850 Robot User s Guide...
Страница 2: ......
Страница 8: ...Table of Contents 8 AdeptViper s650s 850 Robot User s Guide Rev A...
Страница 38: ...Chapter 3 Robot Installation 38 AdeptViper s650 s850 Robot User s Guide Rev A...
Страница 48: ...Chapter 4 System Installation 48 AdeptViper s650 s850 Robot User s Guide Rev A...
Страница 56: ...Chapter 5 System Operation 56 AdeptViper s650 s850 Robot User s Guide Rev A...
Страница 62: ...Chapter 6 Maintenance 62 AdeptViper s650 s850 Robot User s Guide Rev A...
Страница 70: ...Chapter 7 Technical Specifications 70 AdeptViper s650 s850 Robot User s Guide Rev A...
Страница 74: ...Index 74 AdeptViper s650 s850 Robot User s Guide Rev A...
Страница 75: ......
Страница 76: ...3011 Triad Drive Livermore CA 94551 925 245 3400 P N 05173 000 Rev A...