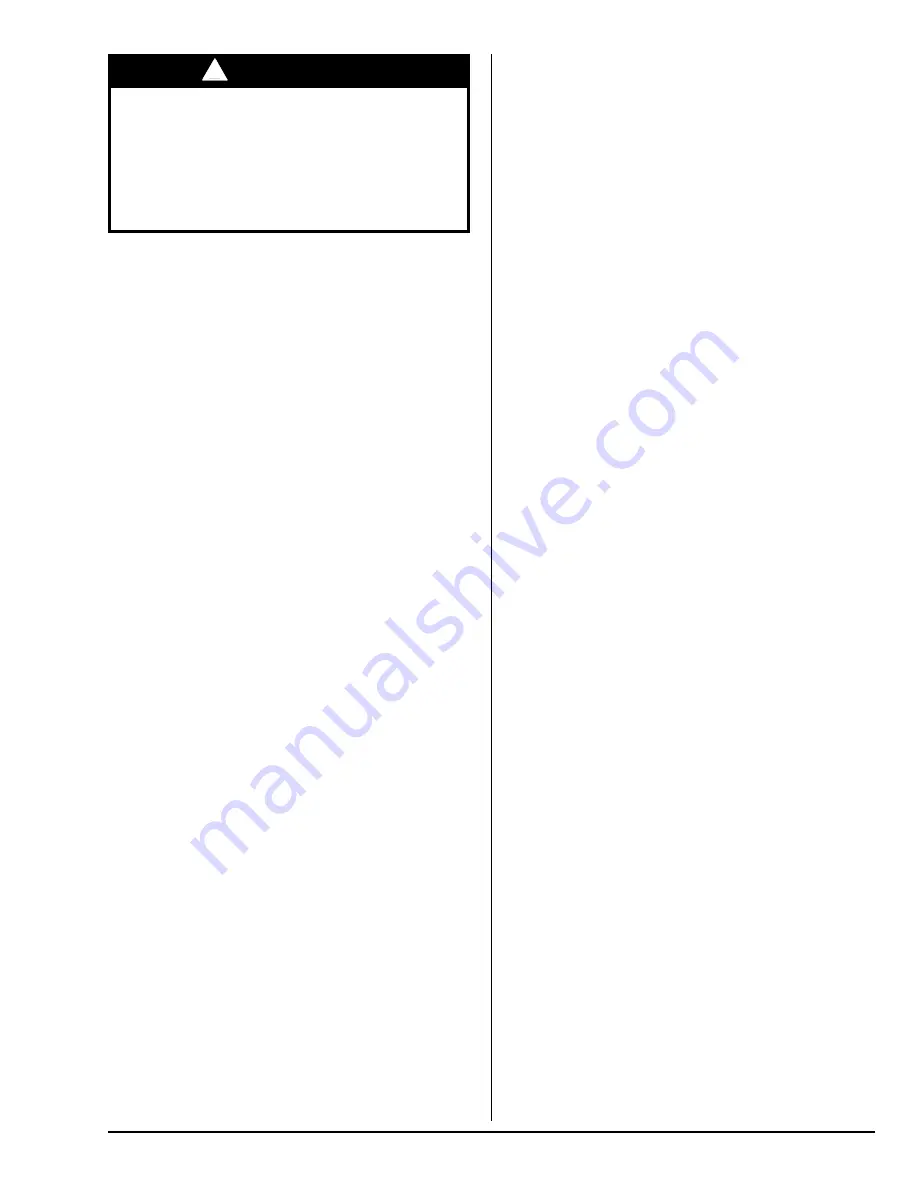
113362 - 25
17
When a gas dryer is first started (during initial start-up), it
has a tendency not to ignite on the first ignition attempt.
This is because the gas supply piping is filled with air, so it
may take a few minutes for the air to be purged from the
lines.
NOTE:
During the purging period, check to be sure that
all gas shutoff valves are open.
Gas dryers are equipped with a DSI system, which has
internal diagnostics. If ignition is not established within 3
attempts, the heat circuit in the DSI module will “lockout”
until it is manually reset. To reset the DSI system, open
and close the main door and restart the dryer.
A gas pressure test should be taken at the gas valve pressure
tap of each dryer to ensure that the water column pressure is
correct and consistent.
NOTE:
Water column pressure requirements (measured at
the pressure tap of the gas valve body):
Natural Gas _____ 3.5 in WC (8.7 mb)
Propane Gas __ 10.5 in WC (26.1 mb)
IMPORTANT:
There is no regulator provided in a propane
dryer. The water column pressure must be regulated at
the source (propane tank), or an external regulator must
be added to each dryer.
Safety Related Circuits
Make a complete operational check of all safety related
circuits:
• Door Switch(es)
• Hi-Limit Thermostats
• Sail Switch
Sail Switch Adjustment
To check for proper sail switch operation (for gas and electric
models only), open the main door and while holding main
door switch plunger in, start dryer. Dryer should start but
heat circuit should not be activated (on). If the heat system
is activated, the sail switch is improperly adjusted and must
be adjusted by bending the actuator arm of the sail switch
toward the burner box. If the actuator arm is bent too far
toward the burner box of the dryer, the dryer may not have
heat when needed. After any adjustment to the sail switch,
the above procedure must be repeated to verify proper
operation of the sail switch.
The dryer should be operated through 1 complete cycle to
ensure that no further adjustments are necessary and that
all components are functioning properly.
Make a complete operational check of all operating controls.
For microprocessor model check controller (computer)
programs/selections: each microprocessor controller
(computer) has been preprogrammed by the factory with the
most commonly used parameter (program) selections. If
computer program changes are required, refer to the
computer programming manual, which was shipped with the
dryer.
Tumbler Coating
The tumbler is treated with a protective coating. We suggest
dampening old garments or cloth material with a solution of
water and nonflammable mild detergent and tumbling them
in the tumbler to remove this coating.
!
WARNING
ELECTRICAL SHOCK HAZARD
Electrical shock hazard can result in serious injury.
If the water dispensing system is activated do not
attempt to operate the dryer.
If the water dispensing system is activated have the
dryer inspected by a qualified agency before operating
the dryer.
Preparation for Operation / Start-Up _
The following items should be checked before attempting
to operate the dryer:
• Read all “CAUTION,” “WARNING,” and “DIRECTION”
labels attached to the dryer.
• Check incoming supply voltage to be sure that it is the
same as indicated on the data label. In the case of 208
VAC or 240 VAC, the supply voltage must match the
electric service exactly.
• GAS MODELS – Check to ensure that the dryer is
connected to the type of gas indicated on the data label.
• GAS MODELS – Be sure that all gas shutoff valves are
in the open position.
• GAS AND ELECTRIC MODELS – The sail switch
damper assembly was installed and adjusted at the
factory prior to shipping. However, each sail switch
adjustment must be checked to ensure that this
important safety control is functioning. (Refer to Sail
Switch Adjustment in the Preoperational Test section.)
• Be sure all back panels (guards) and electric box
covers are in place.
• Be sure the service doors are closed and securely in
place.
• Be sure the lint door/drawer is securely in place.
• Rotate the tumbler (drum) by hand to be sure it moves
freely.
• Check bolts, nuts, screws, terminals, and fittings for
tightness and security.
• Check tumbler bearing setscrews to ensure they are all
tight.
• Check that the vent is connected to the dryer and is
exhausted to the outdoors.
Preoperational Test __________________
All dryers are thoroughly tested and inspected before leaving
the factory. However, a preoperational test should be
performed before the dryer is publicly used. It is possible
that adjustments have changed in transit or due to marginal
location (installation) conditions. Installer must instruct the
user on how to correctly operate the dryer before leaving.
Turn on electric power to the dryer.
Refer to the Operating Instructions for starting your particular
model dryer.
Gas Dryers
Open all shutoff valves.
Содержание ML-96
Страница 24: ...ADC Part No 113362 25 09 17 21 ...