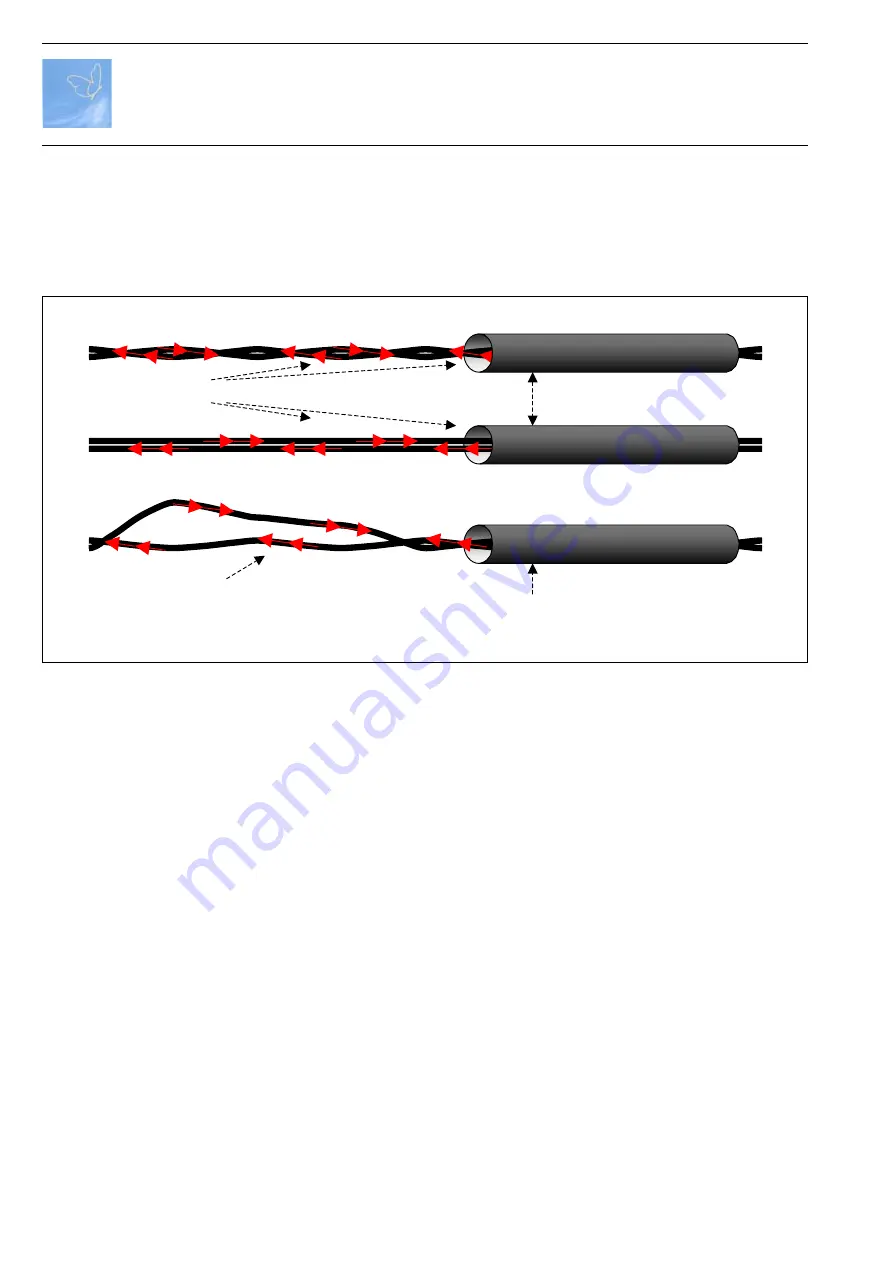
12 Planning and Installation Guidelines
Planning and
Installation Guidelines
Technical Description
Wireless Proximity Switches / Issue: 03.2005
V 6
1.6 Installation of the supply line for the primary loops
●
The supply lines for a primary loop must be twisted with each other or held closely together in any
other way (e.g. by cable ties, heat shrinkable tubes, etc.) over the entire distance to the power
supply.
●
The total length of all supply lines for one pair of primary loops can be max. 8 m.
●
The line length required for one primary loop can be calculated as follows:
line length = circumference x number of wi 2 x supply line length.
●
Due to double insulation the supply lines can also be laid open.
●
For higher stability the supply lines for a primary loop (twisted with each other or held closely
together in any other way) can be laid in armored plastic or steel conduits or similar materials.
Fig. 1.8: Laying of the supply lines for a primary loop
2CDC352020F0003.EPS
Permitted laying of the supply lines for the primary loops
Inadmissible laying of the supply lines for the primary loops
Installation conduit, cable duct or similar
Installation conduit, cable duct or similar