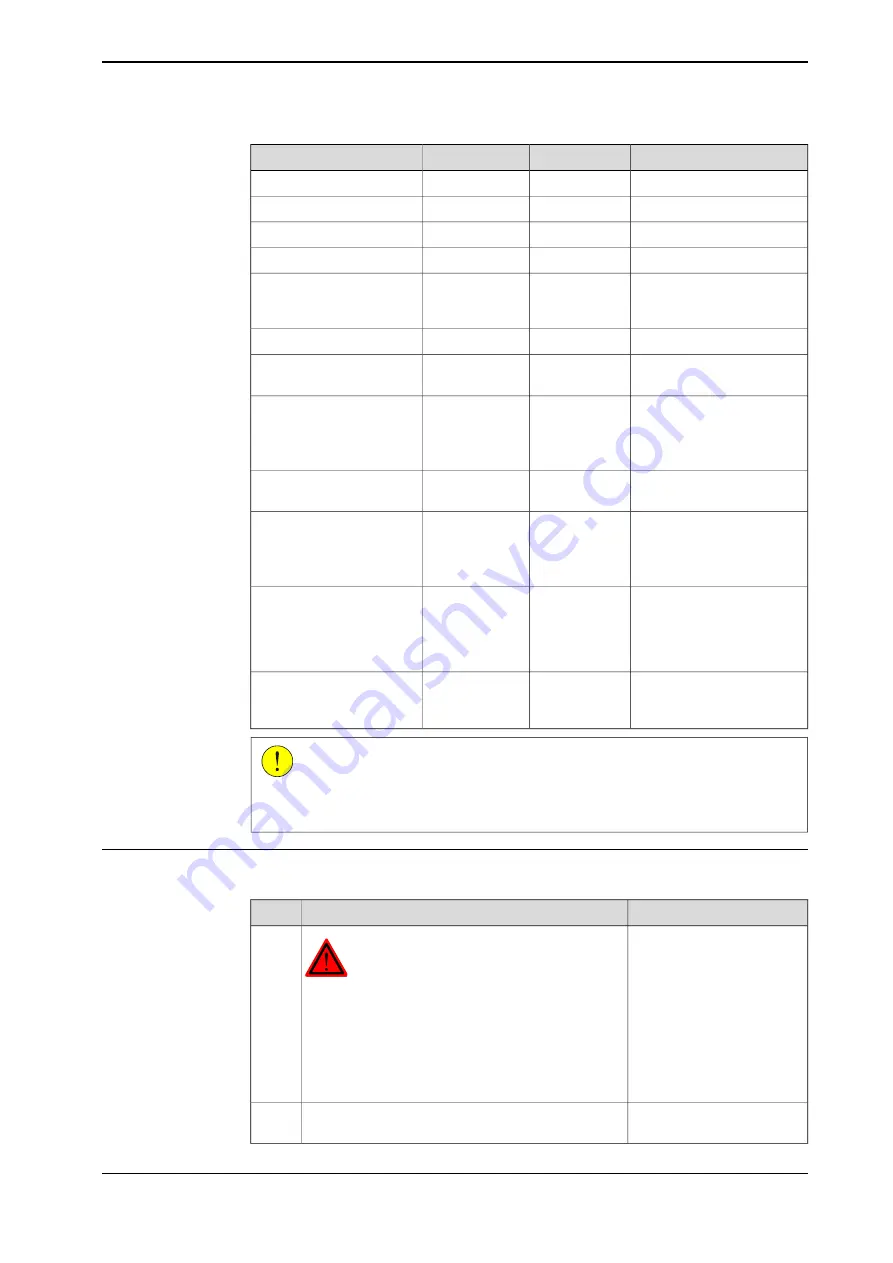
Note
Art. no.
Spare part no.
Equipment, etc.
3HAB3772-23
O-ring
3HAC3297-1
Sealing, outside
3HAA2167-11
Spherical roller bearing
3HAC3990-11
Sealing, inside
Used to lubricate the shaft
on the robot where the tie
rod is to be refitted.
3HAB3537-1
Grease
Loctite 243
Locking liquid
Content is defined in section
3HAC17594-1
Standard toolkit
2 pcs
Puller tool
Used to pull out the tie rod
alternately at the upper and
lower end if the tie rod.
Used to press in the spheric-
al roller bearing.
3HAB1598-1
Press tool
2 pcs.
3HAB1529-1
Press tool, p-arm
Used to press on the tie rod
alternately at the upper and
lower end of the tie rod.
These procedures include
references to the tools re-
quired.
Other tools and procedures
may be required. See refer-
ences to these procedures
in the step-by-step instruc-
tions below.
General calibration informa-
tion is included in section
Calibration Pendulum In-
struction
CAUTION
Always cut the paint with a knife and grind the paint edge when disassembling
parts. See
Cut the paint or surface on the robot before replacing parts on page 140
.
Removal, tie rod
The procedure below details how to remove the tie rod from the robot.
Info/Illustration
Action
DANGER
Turn off all:
•
electric power supply
•
hydraulic pressure supply
•
air pressure supply (do not turn off for Foundry
Prime robots!)
to the robot, before entering the robot working area.
1
Lock the upper arm in a horizontal position with help
of a crane or similar.
2
Continues on next page
Product manual - IRB 4400
191
3HAC022032-001 Revision: Q
© Copyright 2004-2018 ABB. All rights reserved.
4 Repair
4.5.2 Replacement of tie rod
Continued
Содержание IRB 4400 - L10
Страница 1: ...ROBOTICS Product manual IRB 4400 ...
Страница 2: ...Trace back information Workspace R18 1 version a9 Checked in 2018 03 22 Skribenta version 5 2 025 ...
Страница 8: ...This page is intentionally left blank ...
Страница 94: ...This page is intentionally left blank ...
Страница 282: ...This page is intentionally left blank ...
Страница 294: ...This page is intentionally left blank ...
Страница 296: ...This page is intentionally left blank ...
Страница 302: ......
Страница 303: ......