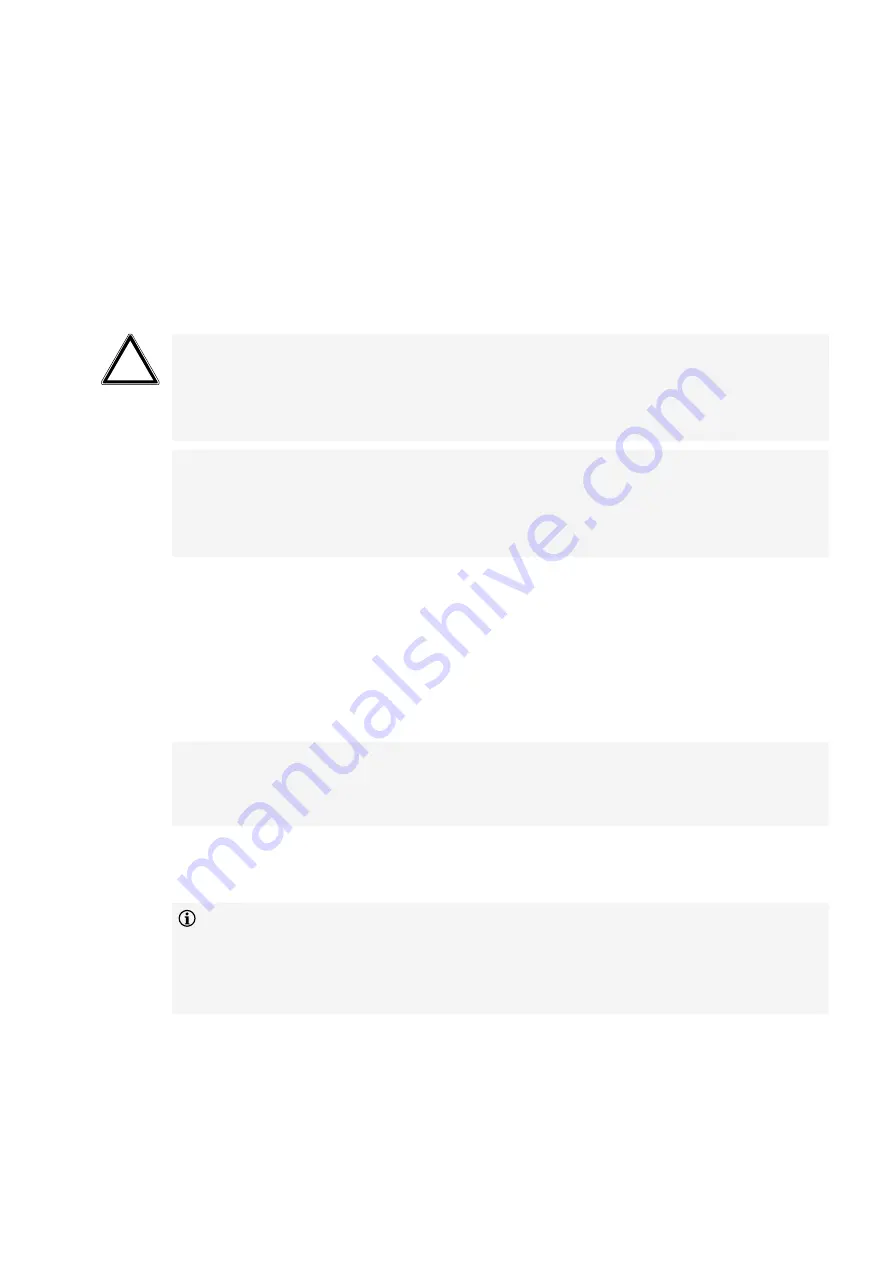
ABB i-bus
®
KNX
Planning and application
FCC/S 1.X.X.1 | 2CDC 508 200 D0211 Rev A 366
12.5.1
2-point controller
A 2-point controller possesses two output states (On/Off) that change depending on the actual
value. If the actual value is higher than the parametrized setpoint, the associated control value is 0.
If the actual value is less than the parametrized setpoint, the associated control value is 1.
Application for a 2-point controller:
•
As the control value oscillates only between the two On and Off states, the controller can con-
trol an electrothermal valve connected to a switch actuator or a valve drive actuator.
•
Control of an electric heater via a relay output, as a distinction is also made only between On
and Off with this heater.
NOTICE
The number of relay operating cycles must be observed. The relay switches each time the con-
trol value changes. The maximum number of relay operating cycles, particularly under load, is
limited. This can quickly exceed the relay's service life, especially when controlling an electric
heater (which often represents high loads).
Example:
If the control value changes only ten times per day, this already amounts to 3,650 operating cy-
cles per year.
If the control value changes 50 times per day, this already amounts to 18,250 operating cycles
per year.
A 2-point controller can quickly compensate for control deviations in case of large changes in the
command variable (setpoint temperature). However, it never settles and it tends to lead to system
overshoot (exceeding the setpoint temperature) in this process. In oder to avoid overshooting the
initial states, 2-point controllers always feature integrated hysteresis that fluctuates around the set-
point.
The function of hysteresis is to allow the control value to switch only when the control value is ex-
ceeded/fallen below by a certain value. This reduces number of control value changes and there-
fore leads to smoother control.
Correctly adjusting the hysteresis can also limit the number of relay operating cycles.
Example:
If the heating-operation setpoint is 21 °C and the hysteresis is 1.0 K, the controller will switch on
when the temperature falls below 20.5 °C and will switch off again when the temperature exceeds
21.5 °C.
The parameter
Hysteresis
should be set based on the following factors:
•
How quickly the heater can heat the room or how quickly the cooler can cool it
•
How people in the room perceive the temperature.
Note
The selected hysteresis should not be too small, because a switching valve drive would con-
stantly open and close in this case.
The selected hysteresis should not be too large, because the temperature fluctuations in the
room would be too large in this case.
12.5.1.1
Pulse width modulation (PWM)
With pulse width modulation, the valve is operated as with 2-point control exclusively in the posi-
tions fully opened and fully closed. In contrast to 2-point control, the position is not controlled via
limit values, but rather by calculated control values similar to continuous control.
The control value is fixed for a timed cycle and recalculated in the duration for valve opening. The
control value 20% at a cycle time of 15 minutes, for example, will be converted to a valve opening
time of three minutes. The control value 50% results in a valve opening time of 7.5 minutes.