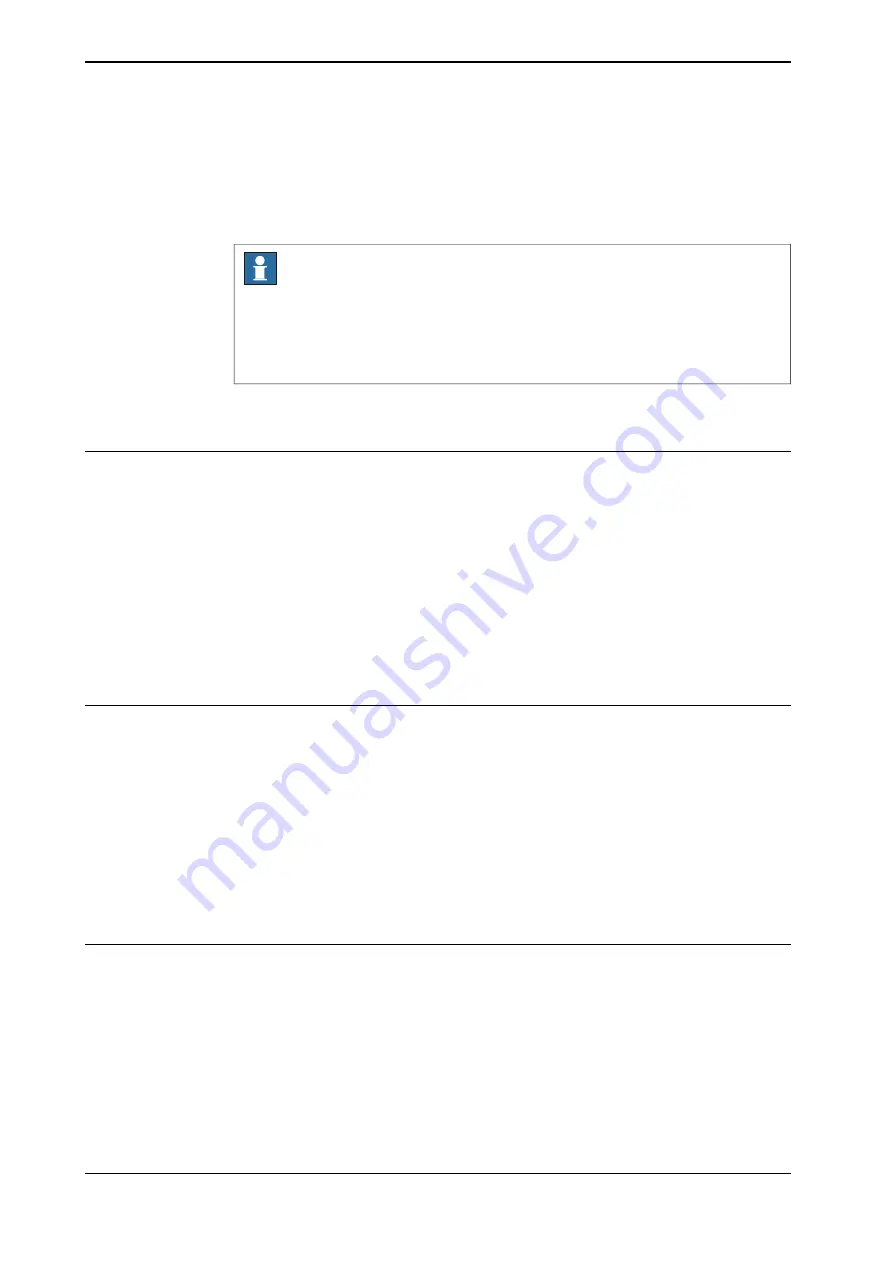
•
All safety zones with connected supervision functions and signals used for
safety interlocking
•
All global supervision functions
•
All tools with corresponding supervision functions
Note
Depending on the combination of functions, the validation procedures have to
be modified for the specific configuration.
A more detailed description of validation of the safety configuration is found in
Application manual - Functional safety and SafeMove
.
After safety configuration is validated, it must be set to validated and locked in the
system.
Preparations before validation
Do the following checks before you start the validation procedure:
1 Carry out the synchronization procedure.
2 If configured, run the service routine for the function Cyclic Break Check.
3 Turn off the
SafeMove Assistant
functionality, with the system parameter
Disable SafeMove Assistant
.
4 Turn off collision detection during validation of any tool force supervision
5 Start the validation procedure.
If using protected groups in the safety configuration, only the modified parts
must be validated.
ABB Safety Configuration Report
The validation of each function should be documented in the safety report by
signature of the validator.
The safety configuration report lists all parameters that are set for the installation.
The report also includes a visual representation of the installation, a floor plan.
This shows the robot and safety zones as seen from above.
The configuration report includes the checksum (multiple checksums if using
protected groups in the safety configuration). The checksum can also be read
using the RAPID function
SafetyControllerGetChecksum
or
SafetyControllerGetGroupChecksum
.
Setting the configuration to validated
When the safety technician has validated the configuration and signed the safety
report, the status of the configuration shall be changed to
Validated
on the
FlexPendant.
1 Log in as a user with the grant
Safety Services
.
2 In the
Settings
app, select the
Safety Controller
, and then
Configuration
.
3 Select the check box
Validated
.
Continues on next page
130
Product manual - CRB 15000
3HAC077389-001 Revision: L
© Copyright 2021 - 2023 ABB. All rights reserved.
3 Installation and commissioning
3.6.3 The SafeMove configurator app on FlexPendant
Continued
Содержание CRB 15000
Страница 1: ...ROBOTICS Product manual CRB 15000 ...
Страница 2: ...Trace back information Workspace 23B version a17 Checked in 2023 06 29 Skribenta version 5 5 019 ...
Страница 8: ...This page is intentionally left blank ...
Страница 16: ...This page is intentionally left blank ...
Страница 38: ...This page is intentionally left blank ...
Страница 54: ...This page is intentionally left blank ...
Страница 182: ...This page is intentionally left blank ...
Страница 200: ...This page is intentionally left blank ...
Страница 1058: ...This page is intentionally left blank ...
Страница 1076: ...This page is intentionally left blank ...
Страница 1095: ......