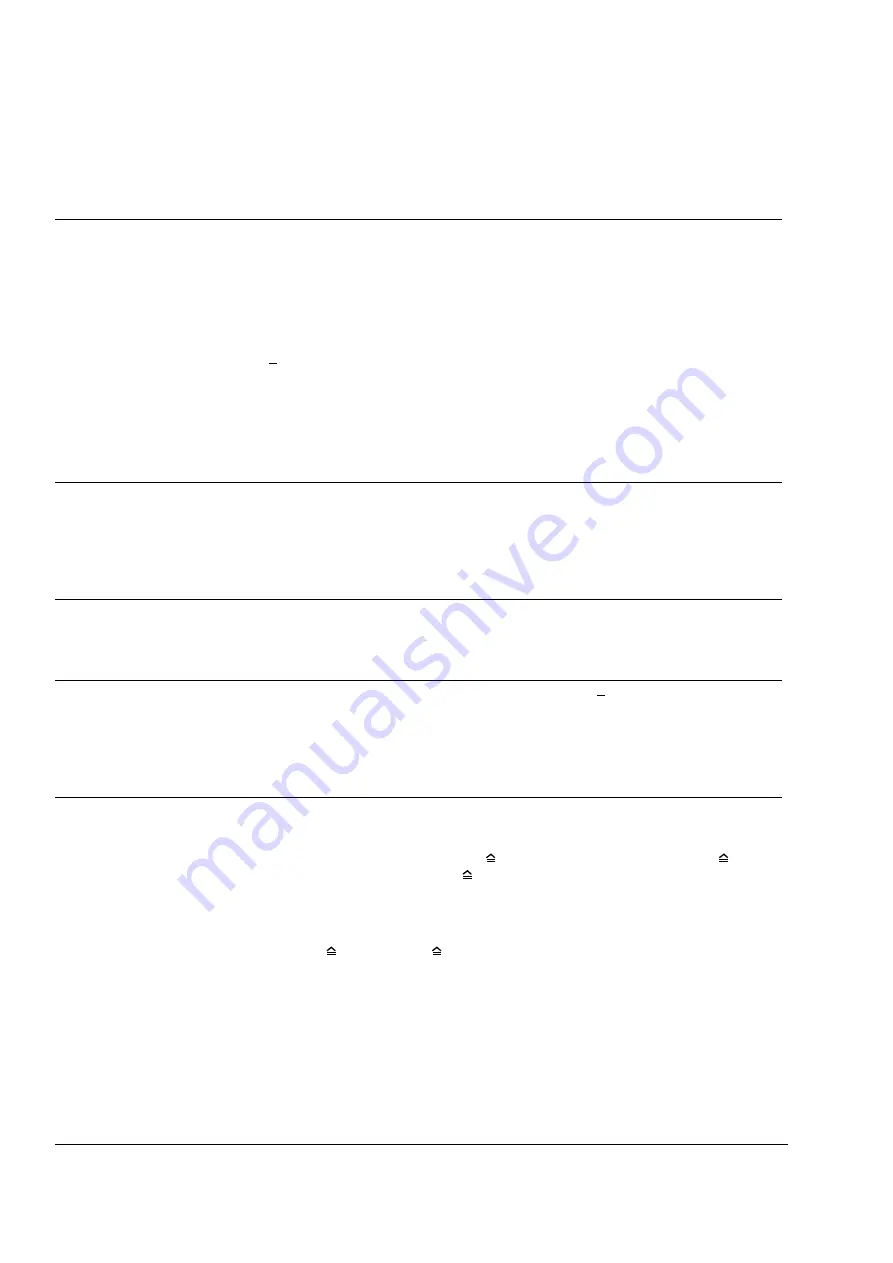
Motor control and I/O board (RMIO)
72
RMIO board specifications
Analogue inputs
With Standard Application Program two programmable differential current inputs
(0 mA / 4 mA ... 20 mA,
R
in
= 100 ohm) and one programmable differential voltage
input (-10 V / 0 V / 2 V ... +10 V,
R
in
> 200 kohm).
The analogue inputs are galvanically isolated as a group.
Isolation test voltage
500 VAC, 1 min
Max. common mode voltage
between the channels
±15 VDC
Common mode rejection ratio
> 60 dB at 50 Hz
Resolution
0.025 % (12 bit) for the -10 V ... +10 V input. 0.5 % (11 bit) for the 0 ... +10 V and 0 ...
20 mA inputs.
Inaccuracy
±
0.5 % (Full Scale Range) at 25
°
C (77
°
F). Temperature coefficient: ± 100 ppm/
°
C
(± 56 ppm/°F), max.
Constant voltage output
Voltage
+10 VDC, 0, -10 VDC ± 0.5 % (Full Scale Range) at 25 °C (77
°
F). Temperature
coefficient: ± 100 ppm/°C (± 56 ppm/°F) max.
Maximum load
10 mA
Applicable potentiometer
1 kohm to 10 kohm
Auxiliary power output
Voltage
24 VDC ± 10 %, short circuit proof
Maximum current
250 mA (without any optional modules inserted onto slots 1 and 2)
Analogue outputs
Two programmable current outputs: 0 (4) to 20 mA,
R
L
< 700 ohm
Resolution
0.1 % (10 bit)
Inaccuracy
±
1 % (Full Scale Range) at 25
°
C (77
°
F). Temperature coefficient: ± 200 ppm/
°
C
(± 111 ppm/
°
F) max.
Digital inputs
With Standard Application Program six programmable digital inputs (common ground:
24 VDC, -15 % to +20 %) and a start interlock input. Group isolated, can be divided in
two isolated groups (see
Isolation and grounding diagram
below).
Thermistor input: 5 mA, < 1.5 kohm
“1” (normal temperature), > 4 kohm
“0”
(high temperature), open circuit
“0” (high temperature).
Internal supply for digital inputs (+24 VDC): short circuit proof. An external 24 VDC
supply can be used instead of the internal supply.
Isolation test voltage
500 VAC, 1 min
Logical thresholds
< 8 VDC
“0”, > 12 VDC
“1”
Input current
DI1 to DI 5: 10 mA, DI6: 5 mA
Filtering time constant
1 ms
Содержание ACS800-02
Страница 1: ...ACS800 Hardware Manual ACS800 02 Drives 45 to 500 kW ACS800 U2 Drives 60 to 600 HP ...
Страница 4: ......
Страница 10: ...Safety instructions 10 ...
Страница 20: ...About this manual 20 ...
Страница 26: ...The ACS800 02 U2 26 ...
Страница 42: ...Planning the electrical installation 42 ...
Страница 76: ...Installation checklist 76 ...
Страница 106: ...Technical data 106 ...
Страница 107: ...Dimensional drawings 107 Dimensional drawings The dimensions are given in milllimetres and inches ...
Страница 108: ...Dimensional drawings 108 Frame size R7 US gland conduit plate 64579746 H ...
Страница 109: ...Dimensional drawings 109 Frame size R8 3AFE 64564161 D US gland conduit plate ...
Страница 110: ...Dimensional drawings 110 Frame size R7 with enclosure extension bottom entry 64625942 1 2 B ...
Страница 111: ...Dimensional drawings 111 64625942 2 2 C ...
Страница 112: ...Dimensional drawings 112 Frame size R7 with enclosure extension top entry 64626264 1 2 C ...
Страница 113: ...Dimensional drawings 113 64626264 2 2 C ...
Страница 114: ...Dimensional drawings 114 Frame size R8 with enclosure extension bottom entry 3AFE 64626388 1 2 B ...
Страница 115: ...Dimensional drawings 115 3AFE 64626388 2 2 B ...
Страница 116: ...Dimensional drawings 116 Frame size R8 with enclosure extension top entry 3AFE 64626370 1 2 C ...
Страница 117: ...Dimensional drawings 117 3AFE 64626370 2 2 C ...
Страница 118: ...Dimensional drawings 118 ...
Страница 127: ......