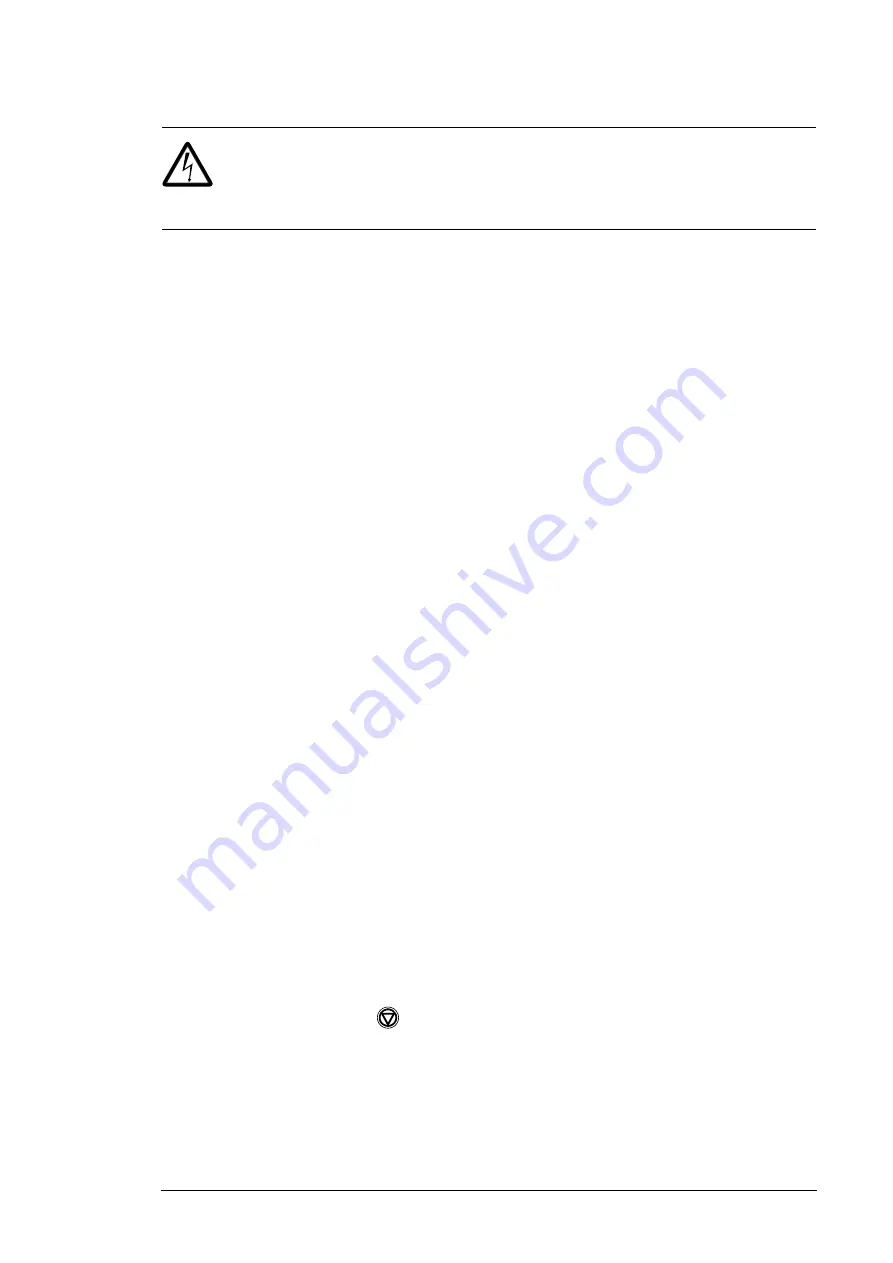
Planning the electrical installation 63
WARNING!
If the drive is connected to multiple motors, a separate thermal
overload switch or a circuit breaker must be used for protecting each cable and
motor. These devices may require a separate fuse to cut off the short-circuit
current.
Protecting the motor against thermal overload
According to regulations, the motor must be protected against thermal overload and the
current must be switched off when overload is detected. The drive includes a motor
thermal protection function that protects the motor and switches off the current when
necessary. Depending on a drive parameter value, the function either monitors a
calculated temperature value (based on a motor thermal model) or an actual temperature
indication given by motor temperature sensors. The user can tune the thermal model
further by feeding in additional motor and load data.
The most common temperature sensors are:
•
motor sizes IEC180…225: thermal switch eg, Klixon
•
motor sizes IEC200…250 and larger: PTC or Pt100.
See the
Firmware manual
for more information on the motor thermal protection, and the
connection and use of the temperature sensors.
Protecting the drive against ground faults
The drive is equipped with an internal ground fault protective function to protect the unit
against ground faults in the motor and motor cable. This is not a personnel safety or a fire
protection feature. The ground fault protective function can be disabled with a parameter,
refer to the appropriate
Firmware manual
.
Measures for protection in case of direct or indirect contact, such as separation from the
environment by double or reinforced insulation or isolation from the supply system by a
transformer, can be applied.
Residual current device compatibility
The drive is suitable to be used with residual current devices of Type B.
Note:
The EMC filter of the drive includes capacitors connected between the main circuit
and the frame. These capacitors and long motor cables increase the ground leakage
current and may cause fault current circuit breakers to function.
Implementing the Emergency stop function
For safety reasons, install the emergency stop devices at each operator control station
and at other operating stations where emergency stop may be needed.
Note:
Pressing the stop key (
) on the control panel of the drive does not generate an
emergency stop of the motor or separate the drive from dangerous potential.
Содержание ACQ810
Страница 1: ...ABB industrial drives Hardware manual ACQ810 drive modules 200 to 400 kW 250 to 600 hp...
Страница 4: ......
Страница 16: ...16 Safety instructions...
Страница 30: ...30 Operation principle and hardware description...
Страница 69: ...Planning the electrical installation 69 Example circuit diagram See page 129...
Страница 70: ...70 Planning the electrical installation...
Страница 88: ...88 Electrical installation...
Страница 94: ...94 Start up...
Страница 96: ...96 Fault tracing...
Страница 122: ...122 Dimension drawings Frame without pedestal mm 64801082_3 6 E Center of gravity...
Страница 123: ...Dimension drawings 123 Frame with busbars on the left side mm 64801082_5 6 E...
Страница 124: ...124 Dimension drawings Drive control unit JCU Can be mounted on a DIN rail EN 50022 35 mm x 7 5 mm...
Страница 125: ...Dimension drawings 125 Package...
Страница 127: ...Dimension drawings 127 Frame with busbars on the left side inches 68440513_5 6 A 64801082 asm E...
Страница 128: ...128 Dimension drawings...
Страница 132: ...132 du dt filters and sine filters Sine filters Contact your local ABB representative...