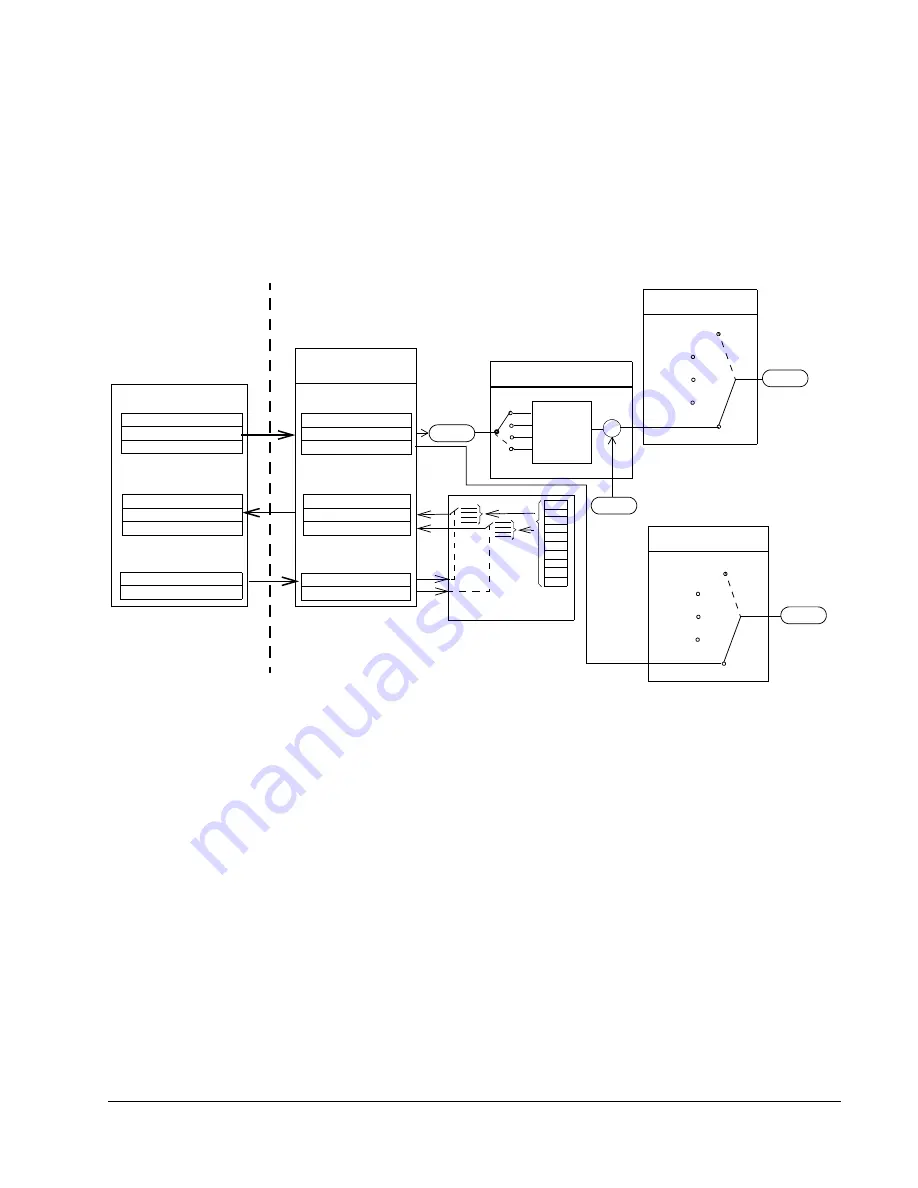
ACQ800-37 Hardware Manual
39
The ACQ800-37
Fieldbus control of the line-side converter
Fieldbus control of the line-side converter is performed via the motor-side converter
RMIO board as shown in the block diagram below.
Block diagram: reference select
The figure below shows the parameters for DC and reactive power reference
selection in the ACQ800 Pump Control Program. AMC table contains actual values
and parameters of the line converter.
Dataset 123 (CH1)
95.08 LCU PAR1 SEL
95.09 LCU PAR2 SEL
+
+
24.04
Dataset 122 (CH0)
MSW (fixed)
106 (value)
110 (value)
PARAM 23.01
AI1
AI2
AI3
FIELD BUS
11.01 DC REF SELECT
23.01
Dataset 121 (CH0)
MCW (fixed)
Q-REF(fixed)
DC REF(fixed)
Dataset 121 (CH1)
MCW
95.06 LCU Q PW REF
95.07 LCU DC REF
Dataset 122 (CH1)
MSW
9.12 LCU ACT SIGNAL 1
9.13 LCU ACT SIGNAL 2
98.02 COMM. MODULE
= INU COM LIM
MCW = Main Control Word
MSW = Main Status Word
DC VOLT REF
Dataset 123 (CH0)
106
110
PARAM 24.01
AI1
AI2
AI3
PARAM 24.02
24.03 Q POWER REF2 SEL
PERCENT
kVAr
PHI
COSPHI
24.02
11.02 Q REF SELECT
24.01
Q POWER REF
Inverter RMIO
board
Line converter RMIO board
AMC
table
Содержание ACQ800 Series
Страница 1: ...Hardware Manual ACQ800 37 Drives 55 to 450 kW 75 to 550 hp ACQ800 ...
Страница 4: ......
Страница 12: ...12 ACQ800 37 Hardware Manual Safety instructions ...
Страница 24: ...24 ACQ800 37 Hardware Manual About this manual ...
Страница 52: ...52 ACQ800 37 Hardware Manual Mechanical installation ...
Страница 78: ...78 ACQ800 37 Hardware Manual Electrical installation ...
Страница 84: ...84 ACQ800 37 Hardware Manual Motor control and I O board RMIO ...
Страница 92: ...92 ACQ800 37 Hardware Manual Installation checklist and start up ...
Страница 106: ...106 ACQ800 37 Hardware Manual Maintenance 3 4 5 6 8 7b 7a ...
Страница 107: ...ACQ800 37 Hardware Manual 107 Maintenance 9 10 11 View from back ...
Страница 123: ...ACQ800 37 Hardware Manual 123 Technical data Declaration of Conformity ...
Страница 124: ...124 ACQ800 37 Hardware Manual Technical data ...
Страница 128: ...128 ACQ800 37 Hardware Manual Dimensions Frame R6 ...
Страница 129: ...ACQ800 37 Hardware Manual 129 Dimensions Frame R6 continued ...
Страница 130: ...130 ACQ800 37 Hardware Manual Dimensions Frame R7i ...
Страница 131: ...ACQ800 37 Hardware Manual 131 Dimensions Frame R7i continued ...
Страница 132: ...132 ACQ800 37 Hardware Manual Dimensions Frame R7i continued ...
Страница 133: ...ACQ800 37 Hardware Manual 133 Dimensions Frame R7i continued ...
Страница 134: ...134 ACQ800 37 Hardware Manual Dimensions Frame R8i ...
Страница 135: ...ACQ800 37 Hardware Manual 135 Dimensions Frame R8i continued ...
Страница 136: ...136 ACQ800 37 Hardware Manual Dimensions Frame R8i continued ...
Страница 137: ...ACQ800 37 Hardware Manual 137 Dimensions Frame R8i continued ...
Страница 138: ...138 ACQ800 37 Hardware Manual Dimensions ...