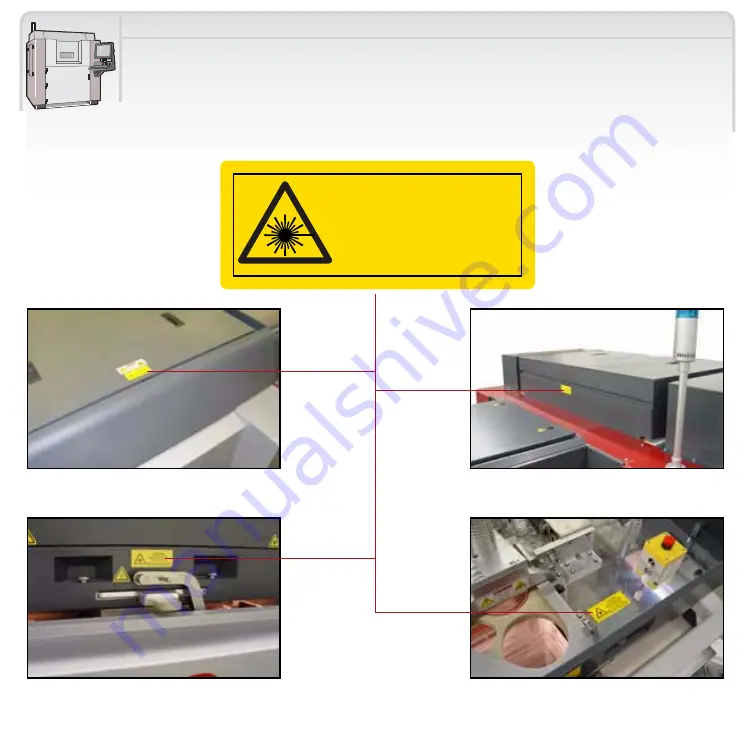
SLS
p r o c e s s
2 3
S A F E T Y
u s e r ’ s g u i d e
l a s e r s a f e t y
DEFEATABLY INTERLOCKED PROTECTIVE HOUSING LASER LABEL LOCATIONS
CAUTION
CLASS 4 INVISIBLE LASER
RADIATION WHEN OPEN AND
INTERLOCKS DEFEATED
AVOID EYE OR SKIN EXPOSURE TO
DIRECT OR SCATTERED RADIATION
At top of SLS system;
on IPM access panel
On back panel of IPM
On front face of IPM;
behind raised laser window access door
(Internal) on IPM base plate; visible after
removing the IPM access panel
Содержание sPro
Страница 68: ...SLS p r o c e s s 6 8 e m p t y u s e r s g u i d e e m p t y...
Страница 106: ...SLS p r o c e s s 1 0 6 u s e r s g u i d e...
Страница 107: ...SLS p r o c e s s 1 0 7 u s e r s g u i d e...
Страница 110: ...SLS p r o c e s s 1 1 0 u s e r s g u i d e...
Страница 111: ...SLS p r o c e s s 1 1 1 u s e r s g u i d e...
Страница 114: ...SLS p r o c e s s 1 1 4 u s e r s g u i d e...
Страница 115: ...SLS p r o c e s s 1 1 5 u s e r s g u i d e...
Страница 116: ...SLS p r o c e s s 1 1 6 u s e r s g u i d e...
Страница 117: ...SLS p r o c e s s 1 1 7 u s e r s g u i d e...
Страница 118: ...SLS p r o c e s s 1 1 8 u s e r s g u i d e...
Страница 119: ...SLS p r o c e s s 1 1 9 u s e r s g u i d e...
Страница 120: ...SLS p r o c e s s 1 2 0 u s e r s g u i d e...
Страница 121: ...SLS p r o c e s s 1 2 1 u s e r s g u i d e...
Страница 122: ...SLS p r o c e s s 1 2 2 u s e r s g u i d e...
Страница 123: ...SLS p r o c e s s 1 2 3 u s e r s g u i d e...
Страница 124: ...SLS p r o c e s s 1 2 4 u s e r s g u i d e...
Страница 125: ...SLS p r o c e s s 1 2 5 u s e r s g u i d e...
Страница 126: ...SLS p r o c e s s 1 2 6 u s e r s g u i d e...
Страница 127: ...SLS p r o c e s s 1 2 7 u s e r s g u i d e...
Страница 128: ...SLS p r o c e s s 1 2 8 u s e r s g u i d e...
Страница 132: ...SLS p r o c e s s 1 3 2 u s e r s g u i d e...