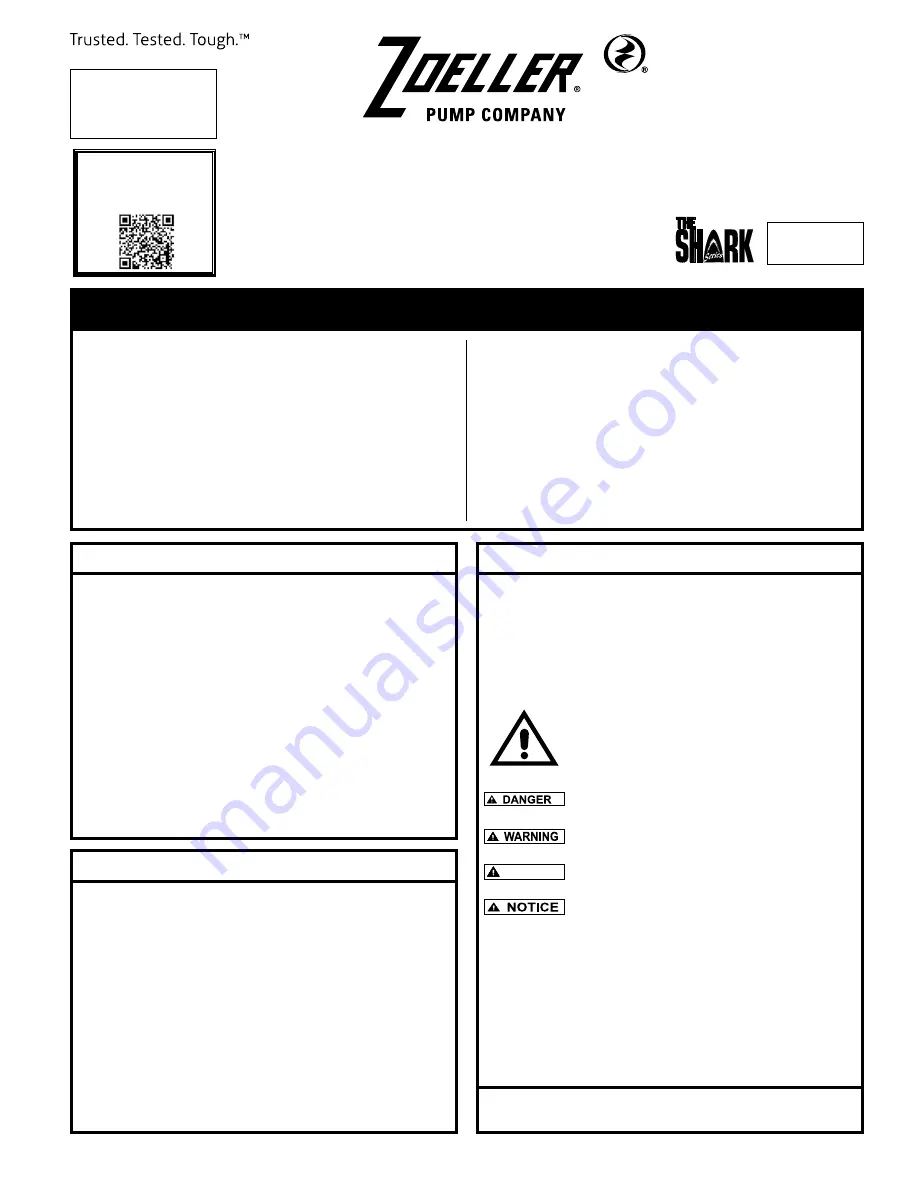
1
© Copyright 2017 Zoeller
®
Co. All rights reserved.
Congratulations on the purchase of the Zoeller submersible
grinder pump. Since 1939, the name Zoeller
®
has represented the
standard for submersible dewatering and sewage pumps. The same
high quality workmanship and easy maintenance design has been
incorporated into this line of heavy-duty submersible grinder pumps.
This Zoeller
®
pump will provide years of trouble-free service when
installed according to the manufacturer’s recommendations.
This manual incorporates the installation, operation,
maintenance, and service instructions into one document to aid
in the ownership of a Zoeller
®
submersible wastewater product.
Model Number:
______________
Date Code:
_______________
Automatic
Nonautomatic
Packaged System
Field Assembled System
Job Name: ____________________________________________
Distributor:
____________________________________________
Date of Purchase:
_________
Zoeller S/O No.:
______________
Contractor:
____________________________________________
Date of Installation:
____________________________________
System Readings During Start-up: Voltage
_____
Amps
______
OWNER’S MANUAL
MODELS 818, 819 & 820 SUBMERSIBLE GRINDER UNITS
Please read and review this manual before installing the
product. Follow the steps in this manual for a proper start-up.
Many items contained within, when followed correctly, will not
only ensure a long and problem-free life for the pump, but also
save time and money during installation. For replacement parts
lists, please reference FM2993 for 818 series, FM2995 for 819
series, and FM1531 for 820 series. Should further assistance
be necessary please call our Product Support Department at
1-800-928-PUMP (7867).
Owner’s Information
Table of Contents
Safety Instructions .......................................................................1
Limited Warranty ..........................................................................2
Preinstallation Checklist ..............................................................3
General Information .....................................................................4
Pump Wiring Instructions ............................................................5
Typical Indoor Prepackaged System ..........................................6
Indoor Prepackaged Installation Instructions ...........................7
Typical Outdoor Prepackaged System .......................................8
Outdoor Prepackaged Installation Instructions ........................9
Operation .....................................................................................10
Cutter Maintenance .................................................................... 11
Service Checklist ........................................................................12
Safety Instructions
TO AVOID SERIOUS OR FATAL PERSONAL INJURY OR MA-
JOR PROPERTY DAMAGE, READ AND FOLLOW ALL SAFETY
INSTRUCTIONS IN THIS MANUAL AND ON THE PUMP.
THIS MANUAL IS INTENDED TO ASSIST IN THE INSTALLATION
AND OPERATION OF THIS UNIT AND MUST BE KEPT WITH
THE PUMP.
This is a
SAFETY ALERT SYMBOL.
When you see this symbol on the pump or in the
manual, look for one of the following signal words
and be alert to the potential for personal injury or
property damage.
Warns of hazards that
WILL
cause serious personal
injury, death or major property damage.
Warns of hazards that
CAN
cause serious personal
injury, death or major property damage.
Warns of hazards that
CAN
cause personal injury
or property damage.
INDICATES SPECIAL INSTRUCTIONS WHICH ARE
VERY IMPORTANT AND MUST BE FOLLOWED.
THOROUGHLY REVIEW ALL INSTRUCTIONS AND WARNINGS
PRIOR TO PERFORMING ANY WORK ON THIS PUMP.
MAINTAIN ALL SAFETY DECALS.
PUMPS WITH THE “UL” MARK AND PUMPS WITH THE “US”
MARK ARE TESTED TO UL STANDARD UL778. CSA CERTIFIED
PUMPS ARE CERTIFIED TO CSA STANDARD C22.2 NO. 108.
CAUTION
REFER TO WARRANTY ON PAGE 2.
FM2167
0917
Supersedes
0117
P/N 019555
Product information presented
here reflects conditions at time
of publication. Consult factory
regarding discrepancies or
inconsistencies.
MAIL TO: P.O. BOX 16347 • Louisville, KY 40256-0347
SHIP TO: 3649 Cane Run Road • Louisville, KY 40211-1961
TEL: (502) 778-2731 • 1 (800) 928-PUMP • FAX: (502) 774-3624
Visit our web site:
zoellerpumps.com
Register your
Zoeller Pump Company
Product on our website:
http://reg.zoellerpumps.com/
®
U.S. Patent No.
8,562,287