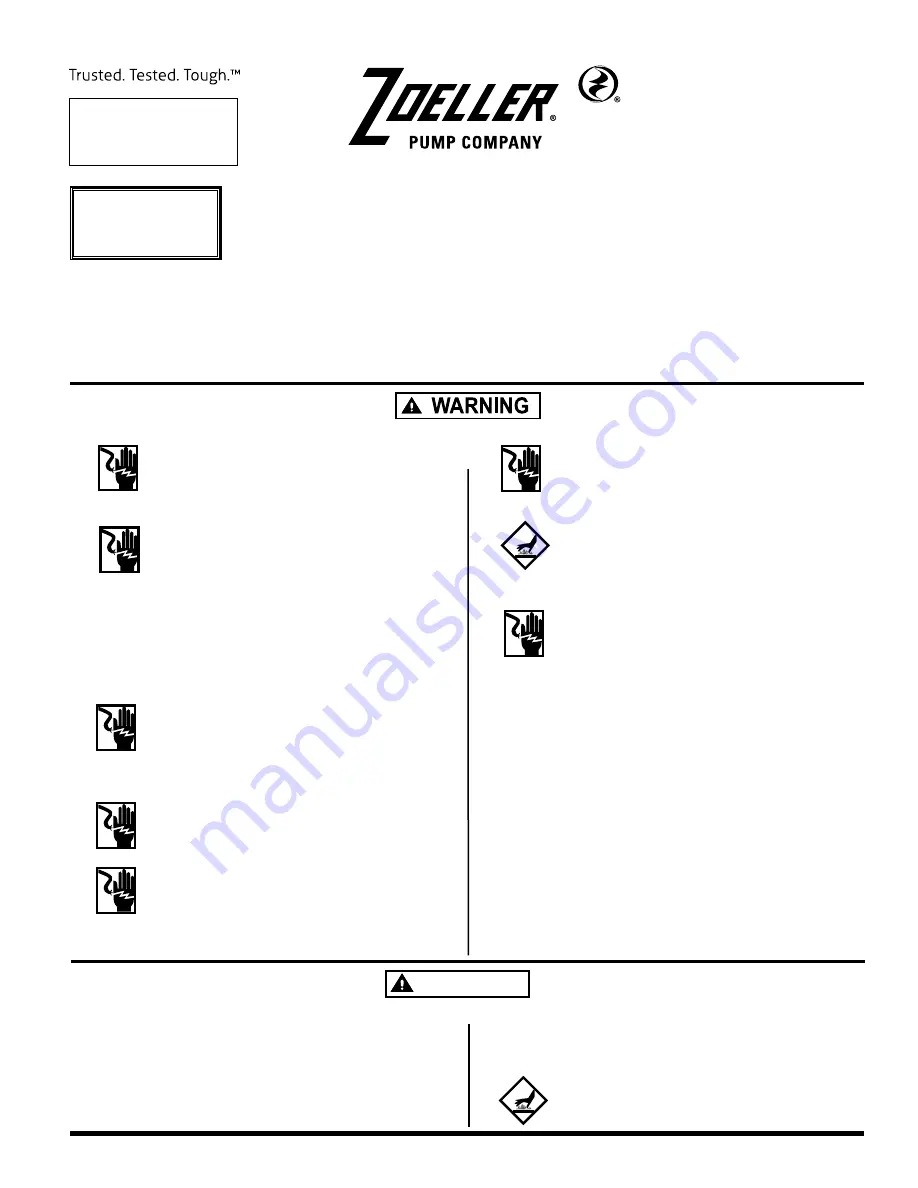
© Copyright 2014 Zoeller
®
Co. All rights reserved.
1
1. Inspect all materials. Occasionally, products are damaged during shipment. If the unit is damaged, contact your dealer before using.
2. Carefully read all the literature provided to familiarize yourself with specific details regarding installation and use before attempting the installation.
These materials should be retained for future reference.
FM2100
1014
Supersedes
0414
INSTALLATION INSTRUCTIONS
300 Series End Suction Pumps
Notice to Installer: Instructions must remain with installation.
PREINSTALLATION CHECKLIST - ALL INSTALLATIONS
SEE BELOW FOR LIST OF WARNINGS
1.
To help reduce the risk of electrical shock, a proper ground
or control box of grounding type must be installed and pro-
tected by a ground fault circuit interrupter (GFCI) in accordance
with the National Electrical Code and applicable local codes.
2.
DO NOT USE AN EXTENSION CORD. Extension cords that
are too long or too light do not deliver sufficient voltage to the
pump motor. But more important, they could present a safety
hazard if the insulation were to become damaged or the connection end
were to fall into a damp or wet area.
3. Make sure the pump’s electrical supply circuit is equipped with fuses
or circuit breakers of proper capacity. A separate branch circuit, sized
according to the National Electrical Code for the current shown on the
pump name plate is recommended.
4.
TESTING FOR GROUND. As a safety measure, electrical
supply should be checked for ground using an Underwriters
Laboratory Listed circuit analyzer which will indicate if the
power, neutral and ground wires are correctly connected . If they are not,
call a qualified licensed electrician.
5.
Installation and checking of electrical circuits and hardware
should only be performed by a qualified licensed
electrician.
6.
FOR YOUR PROTECTION ALWAYS DISCONNECT PUMP
FROM ITS POWER SOURCE BEFORE HANDLING. De-
energize the circuit at the control box. If the power point is
out-of-sight, lock it in the open position and tag it to prevent unexpected
application of power. Failure to do so could result in fatal electrical shock.
7.
Unit must be securely and adequately electrically grounded.
This can be accomplished by wiring the unit to a ground
metal-clad raceway system or by using a separate ground wire
connected to the bare metal of the motor frame or other suitable means.
8.
Do not put a valve in the discharge line
without
automatic shut-
off capability. Failure to install an automatic shut-off (pressure
switch and tank) can allow the pump to run at no flow causing
the pumped liquid to overheat and cause steam burns.
9.
Risk of electric shock. This pump has not been investigated
for use in swimming pool areas.
10. According to the state of California (Prop 65), this product contains chemi-
cals known to the state of California to cause cancer and birth defects or
other reproductive harm.
NOTE: Repair and service should be performed by an Authorized Service Sta-
tion only (Consult factory).
NOTE: Pumps are designed to have a maximum static lift (suction head) of 25
feet (vertical distance from water surface to center line of pump) see suction
limitations.
NOTE: Pumps with the CSA CUS mark are tested to UL standard UL 778 and
certified to CSA standard C22.2 No. 108.
1. Check to be sure your power source is adequate to handle the
amperage requirements of the motor as indicated on the pump or
unit I.D. tag.
2. All plumbing (discharge and intake lines) must be installed to meet
local codes.
3. Be certain the pump is completely primed before starting. Other-
wise damage may occur to the seal.
4.
Be careful when touching the exterior of an operating
motor - it may be hot enough to be painful or cause injury.
020294
CAUTION
SEE BELOW FOR LIST OF CAUTIONS
NOTE: THIS DOCUMENT DOES NOT CONTAIN THE NECESSARY LINKS TO PRINT PROPERLY. ALL LINKS
WILL BE SUPPLIED BY F & W AND A PDF DOCUMENT WILL BE SUPPLIED. THE PDF DOCUMENT MUST BE
USED TO PRINT FROM FOR ZOELLER USE. ANY CHANGES MADE TO THIS DOCUMENT MUST ALSO BE
SENT TO F & W FOR PDF OUTPUT FOR OUR PRINTING NEEDS.
Product information presented
here reflects conditions at time
of publication. Consult factory
regarding discrepancies or
inconsistencies.
MAIL TO: P.O. BOX 16347 • Louisville, KY 40256-0347
SHIP TO: 3649 Cane Run Road • Louisville, KY 40211-1961
TEL: (502) 778-2731 • 1 (800) 928-PUMP • FAX: (502) 774-3624
Visit our web site:
zoellerpumps.com
Register your
Zoeller Pump Company
Product on our website:
http://reg.zoellerpumps.com/