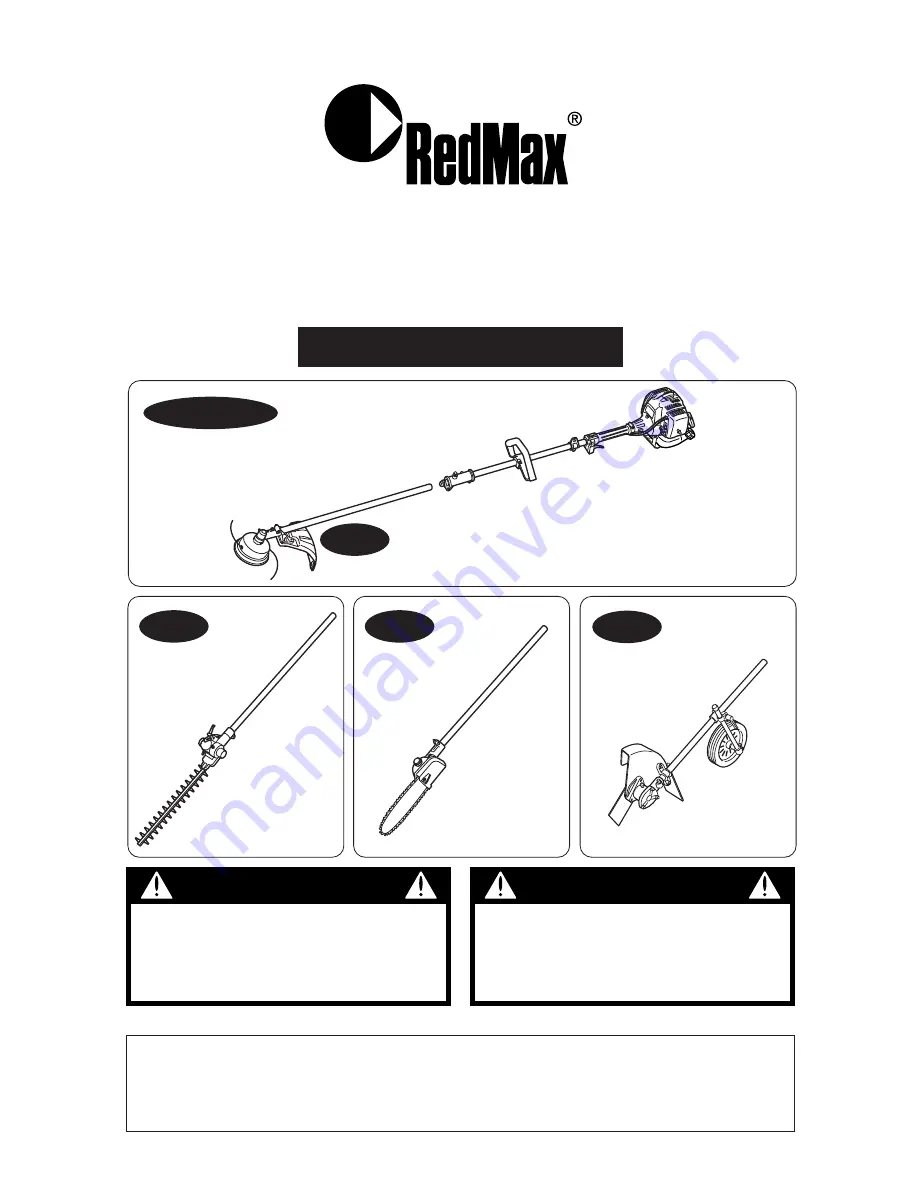
OWNER / OPERATOR MANUAL
EXtreme™
848-BP6-93A1 (501)
The engine exhaust from this product
contains chemicals known to the State
of California to cause cancer, birth
defects or other reproductive harm.
WARNING
Before using our products, please
read this manual carefully to
understand the proper use of your
unit.
WARNING
EXZ-PU
302845 and up
EX-BC
302960 and up
EX-LRT
000531 and up
ENGINE UNIT 50100000 and up
EX-PS
000000 and up
EX-HE
000101 and up
APPLICABLE SERIAL NUMBERS :
EX-BC
EX-PS
EX-LRT
EX-HE
EXZ2500S-BC
Summary of Contents for EXtreme EXZ2500S-BC
Page 46: ...12 Parts list 46 Fig 1 EXZ PU S N 302845 and up ...
Page 48: ...12 Parts list 48 Fig 2 EX BC S N 302960 and up ...
Page 50: ...Fig 3 ENGINE UNIT 50100000 and up 50 12 Parts list ...
Page 52: ...12 Parts list 52 Fig 4 EX LRT S N 000531 and up ...
Page 54: ...12 Parts list 54 Fig 5 EX PS S N 000000 and up ...
Page 56: ...12 Parts list 56 Fig 6 EX HE S N 000101 and up ...