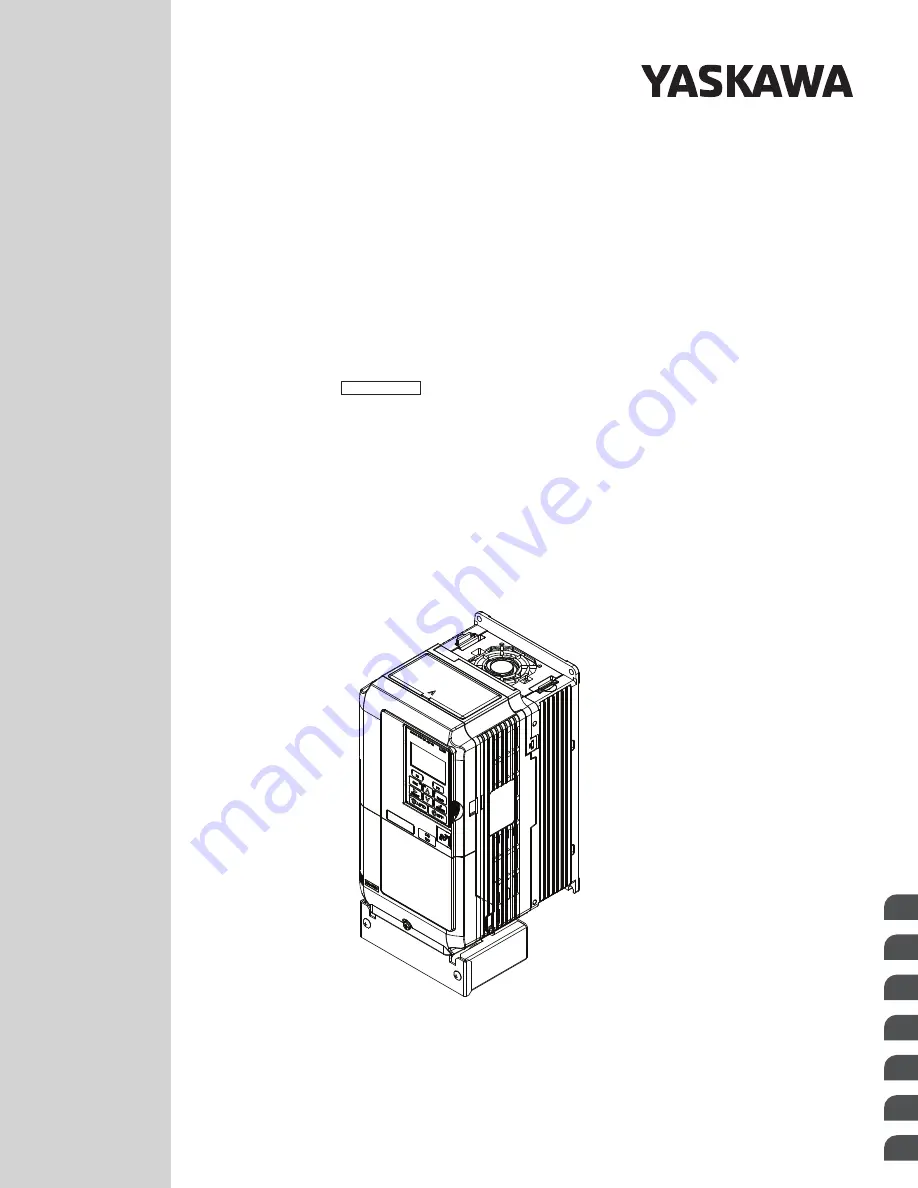
YASKAWA AC Drive Z1000
MANUAL NO. SIEP YAIZ1U 03B
AC Drive for HVAC Fan and Pump
Programming Manual
Models: 600 V Class: 2 to 250 HP
To properly use the product, read this manual thoroughly and retain
for easy reference, inspection, and maintenance. Ensure the end user
receives this manual.
Type: CIMR-ZU
Parameter Details
1
Periodic Inspection &
Maintenance
2
Parameter List
A
BACnet Communications
B
APOGEE FLN (P1)
Communications
C
Metasys N2
Communications
D
MEMOBUS/Modbus
Communications
E
Summary of Contents for Z1000 CIMR-ZU*A Series
Page 339: ......