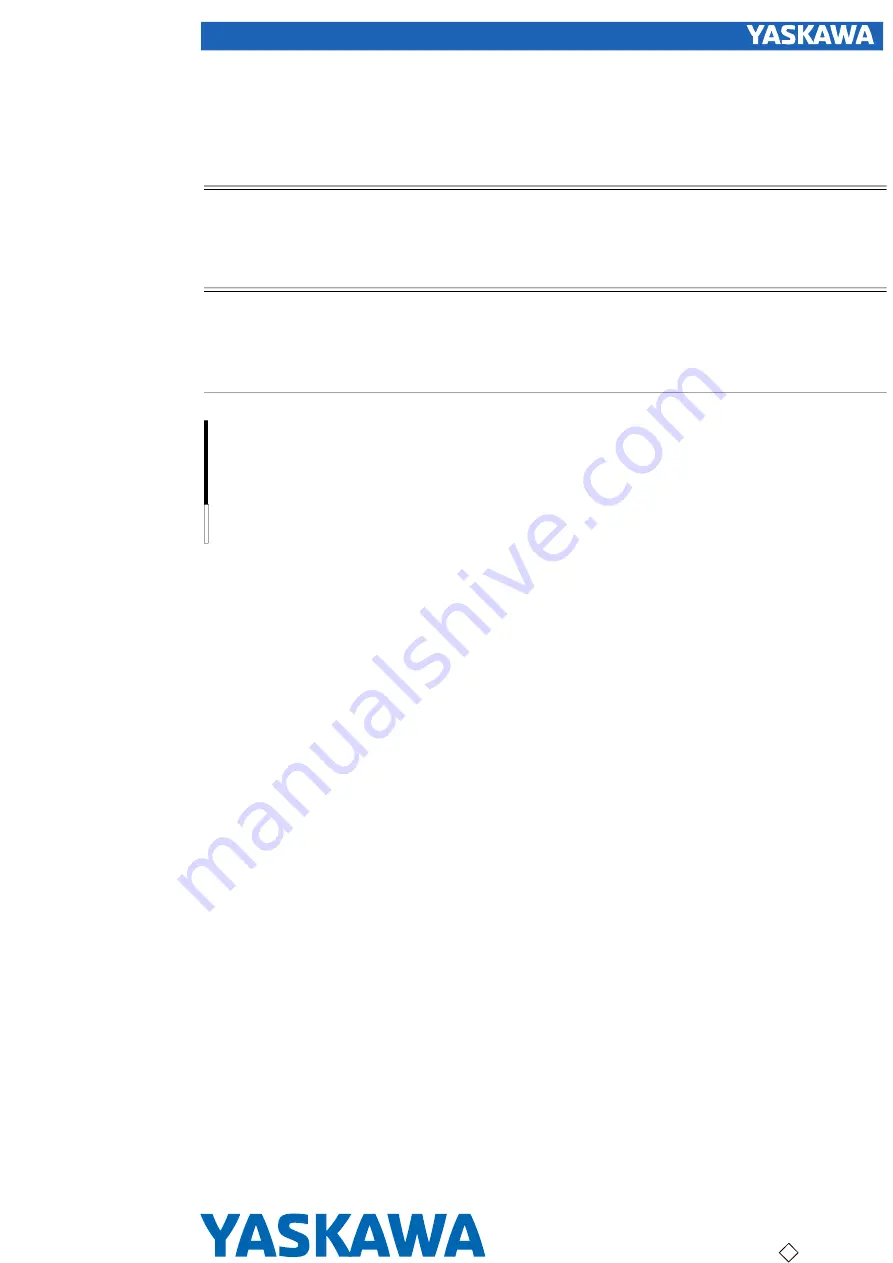
MANUAL NO.
3
HW1480357
Part Number:
159281-1CD
Revision:
1
MOTOMAN-HP20D
MAINTENANCE MANUAL
TYPE:
YR-HP0020D-A00 (STANDARD SPECIFICATION FOR DX100)
YR-HP0020D-B00 (ZEROING SPECIFICATIONS FOR DX100)
YR-HP0020D-A10 (LONG U-ARM, 6kg PAYLOAD SPECIFICATION)
Procedures described in this maintenance manual should be carried out by the person who took the
maintenance-relevant trainings offered by YASKAWA.
Upon receipt of the product and prior to initial operation, read these instructions thoroughly, and retain
for future reference.
MOTOMAN INSTRUCTIONS
MOTOMAN-HP20D INSTRUCTIONS
DX100 INSTRUCTIONS
DX100 OPERATOR’S MANUAL
DX100 MAINTENACE MANUAL
The DX100 operator’s manual above corresponds to specific usage.
Be sure to use the appropriate manual.
1 of 96