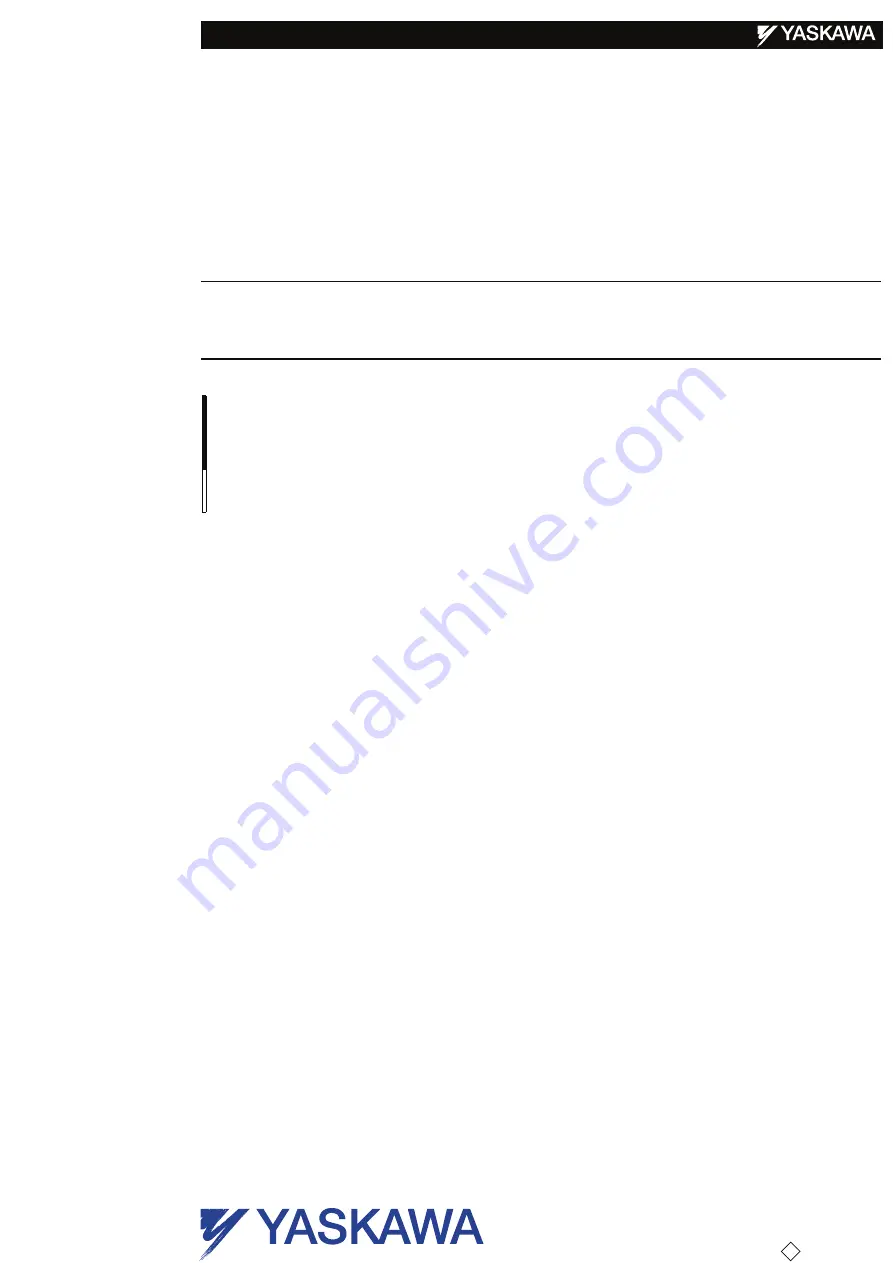
MANUAL NO.
HW0482143
8
YASKAWA ELECTRIC CORPORATION
MOTOMAN-ES200RN
INSTRUCTIONS
TYPE: YR-ES200RN-A00 (STANDARD SPECIFICATION)
YR-ES200RN-A01 (SLU-AXES WITH L.S. SPECIFICATION)
Upon receipt of the product and prior to initial operation, read these instructions thoroughly, and retain
for future reference.
MOTOMAN INSTRUCTIONS
MOTOMAN-ES200RN INSTRUCTIONS
NX100 INSTRUCTIONS
NX100 OPERATOR’S MANUAL
NX100 MAINTENANCE MANUAL
The NX100 operator’s manual above corresponds to specific usage.
Be sure to use the appropriate manual.
1/71
Part Number: 149539-1CD
Revision: 2