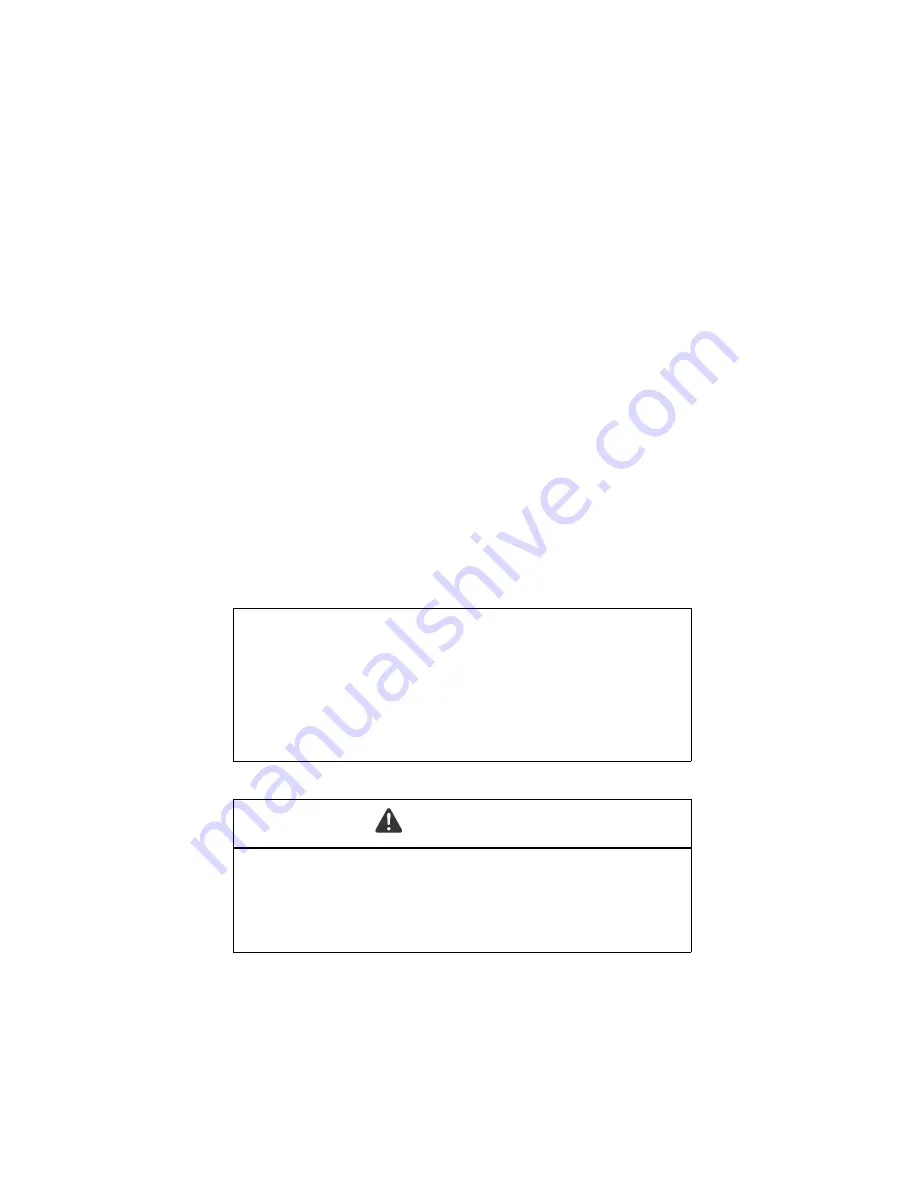
380GLC Excavator
(PIN: 1FF380GX_ _E900001— )
*OMT310294*
OPERATOR'S MANUAL
380GLC Excavator
(PIN: 1FF380GX_ _E900001— )
OMT310294 ISSUE I1
(ENGLISH)
CALIFORNIA
Proposition 65 Warning
Diesel engine exhaust and some of its constituents
are known to the State of California to cause cancer,
birth defects, and other reproductive harm.
If this product contains a gasoline engine:
WARNING
The engine exhaust from this product contains
chemicals known to the State of California to cause
cancer, birth defects or other reproductive harm.
The State of California requires the above two warnings.
Additional Proposition 65 Warnings can be found in this manual.
Worldwide Construction
And Forestry Division
PRINTED IN U.S.A.
Summary of Contents for 380GLC
Page 6: ...Introduction Continued on next page TX JDEULA 19 11JUL16 2 3 TX1219046 UN 11JUL16 092221 PN 6...
Page 7: ...Introduction TX JDEULA 19 11JUL16 3 3 TX1219047 UN 14JUL16 092221 PN 7...
Page 9: ...Introduction DX EMISSIONS EPA 19 12DEC12 2 2 TS1721 UN 15JUL13 092221 PN 9...
Page 17: ...Introduction DX EMISSIONS CARB 19 26AUG20 8 8 RG32759 UN 19AUG20 092221 PN 17...
Page 24: ...Introduction 092221 PN 24...
Page 287: ...Index Index 11 092221 PN 11...
Page 288: ...Index Index 12 092221 PN 12...