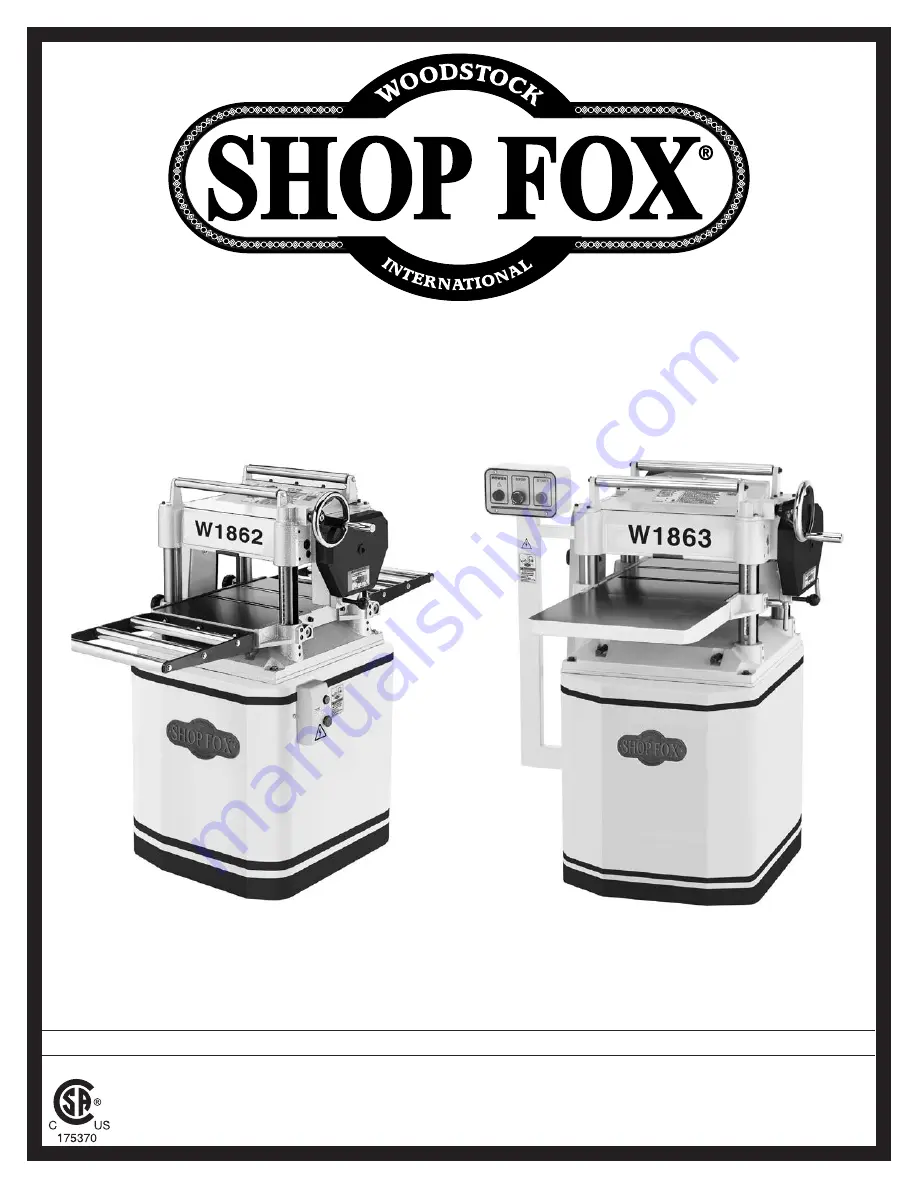
OWNER'S MANUAL
(FOR MODELS MANUFACTURED SINCE 02/19)
MODEL W1862/W1863
15" PLANERS
Phone: (360) 734-3482 • Online Technical Support: [email protected]
COPYRIGHT © DECEMBER, 2018 BY WOODSTOCK INTERNATIONAL, INC. REVISED FEBRUARY, 2019.
WARNING: NO PORTION OF THIS MANUAL MAY BE REPRODUCED IN ANY SHAPE OR FORM WITHOUT
THE WRITTEN APPROVAL OF WOODSTOCK INTERNATIONAL, INC.
#WK19893
Printed in Taiwan
Summary of Contents for W1862
Page 73: ...Model W1862 W1863 For Machines Mfd Since 02 19...
Page 76: ......