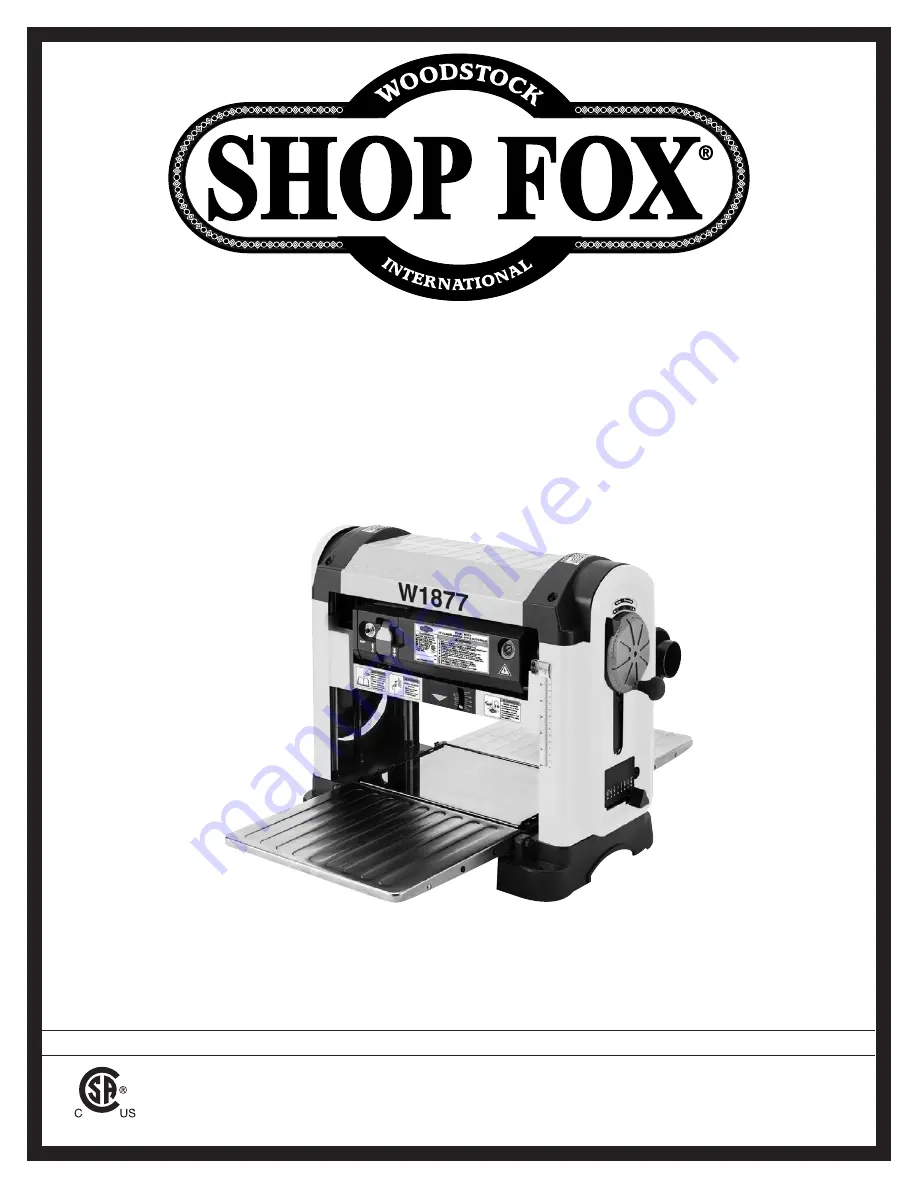
OWNER'S MANUAL
(FOR MODELS MANUFACTURED
SINCE 7/20
)
MODEL W1877
13" PORTABLE PLANER
W
/SPIRAL CUTTERHEAD
Phone: (360) 734-3482 • Online Technical Support: [email protected]
COPYRIGHT ©
SEPTEMBER, 2020
BY WOODSTOCK INTERNATIONAL, INC.
WARNING: NO PORTION OF THIS MANUAL MAY BE REPRODUCED IN ANY SHAPE OR FORM WITHOUT
THE WRITTEN APPROVAL OF WOODSTOCK INTERNATIONAL, INC.
#21226MN Printed in Taiwan
262149
V1.09.20
Summary of Contents for Shop Fox W1877
Page 52: ......