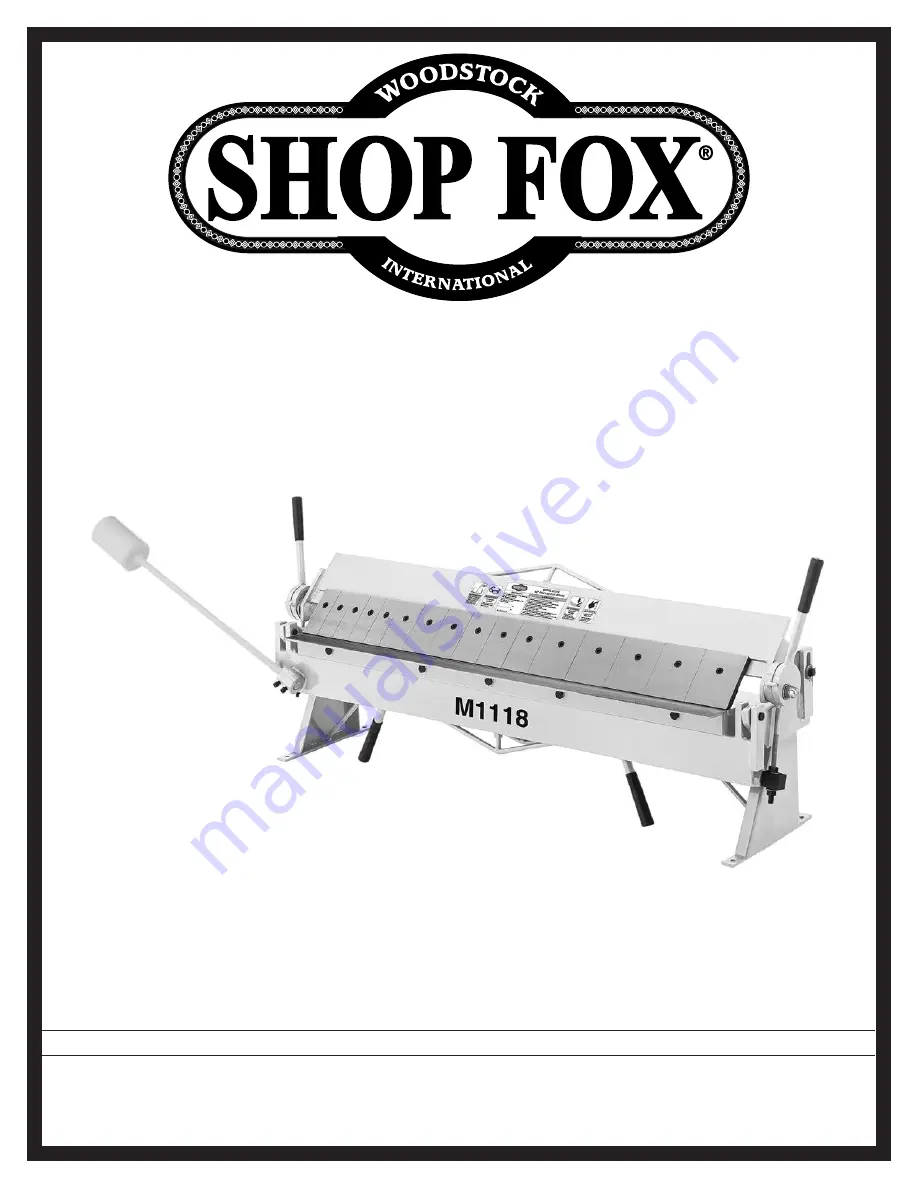
OWNER'S MANUAL
(FOR MODELS MANUFACTURED SINCE 09/21)
MODEL M1118
48" PAN & BOX BRAKE
Phone: (360) 734-3482 • Online Technical Support: [email protected]
COPYRIGHT © OCTOBER, 2021 BY WOODSTOCK INTERNATIONAL, INC.
WARNING: NO PORTION OF THIS MANUAL MAY BE REPRODUCED IN ANY SHAPE OR FORM WITHOUT
THE WRITTEN APPROVAL OF WOODSTOCK INTERNATIONAL, INC.
#22091KS Printed in China
V1.10.21