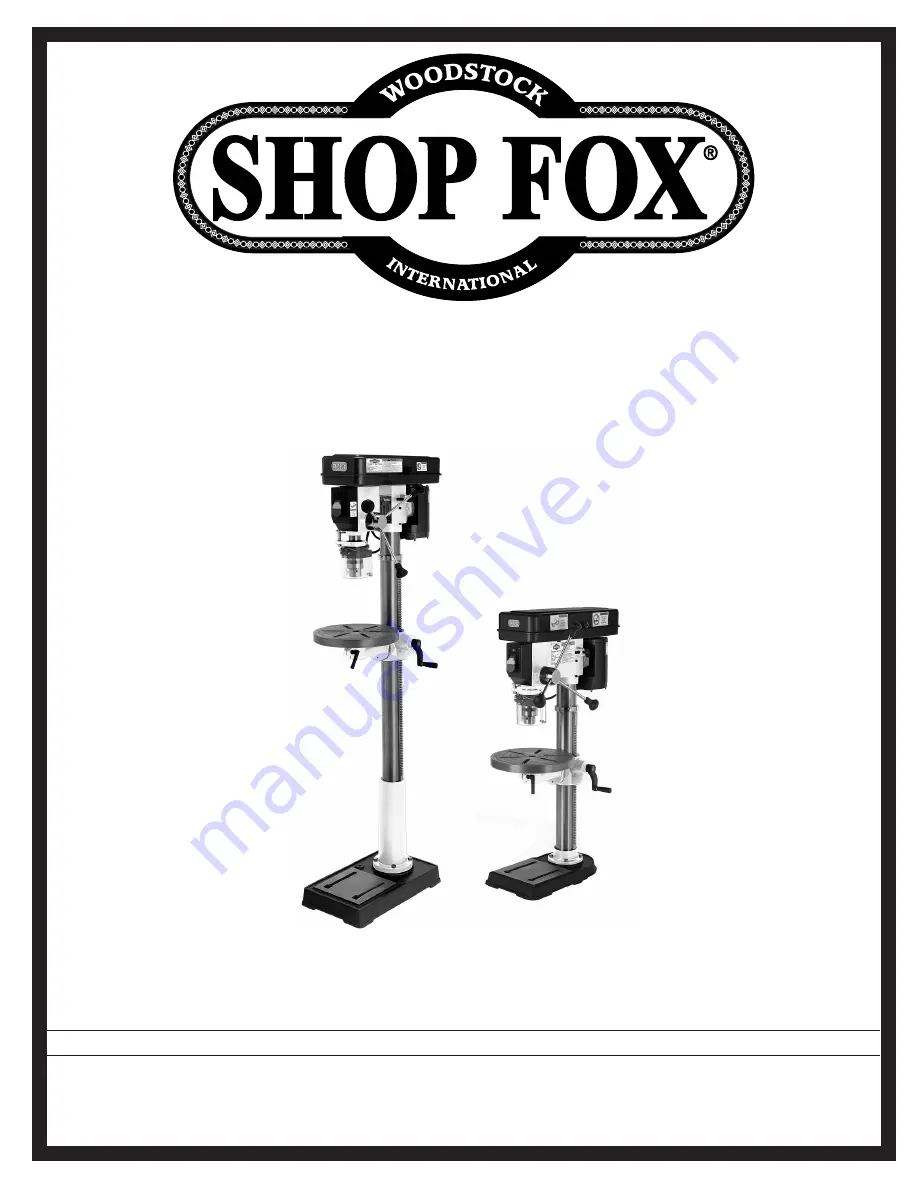
OWNER'S MANUAL
Phone: (360) 734-3482 • On-Line Technical Support: [email protected]
COPYRIGHT © FEBRUARY, 2006 BY WOODSTOCK INTERNATIONAL, INC.
WARNING: NO PORTION OF THIS MANUAL MAY BE REPRODUCED IN ANY SHAPE OR FORM WITHOUT
THE WRITTEN APPROVAL OF WOODSTOCK INTERNATIONAL, INC.
Printed in China
#7958CR
MODEL M1102/M1103
16-SPEED DRILL PRESS
Summary of Contents for SHOP FOX M1102
Page 2: ......
Page 25: ...23 M1102 M1103 16 Speed Drill Press OPERATIONS...
Page 26: ...24 M1102 M1103 16 Speed Drill Press OPERATIONS...
Page 35: ...33 M1102 M1103 16 Speed Drill Press SERVICE Service Notes...
Page 36: ...34 M1102 M1103 16 Speed Drill Press PARTS M1102 M1103 Parts Diagram...
Page 40: ...38 M1102 M1103 16 Speed Drill Press PARTS Parts Notes...
Page 44: ......