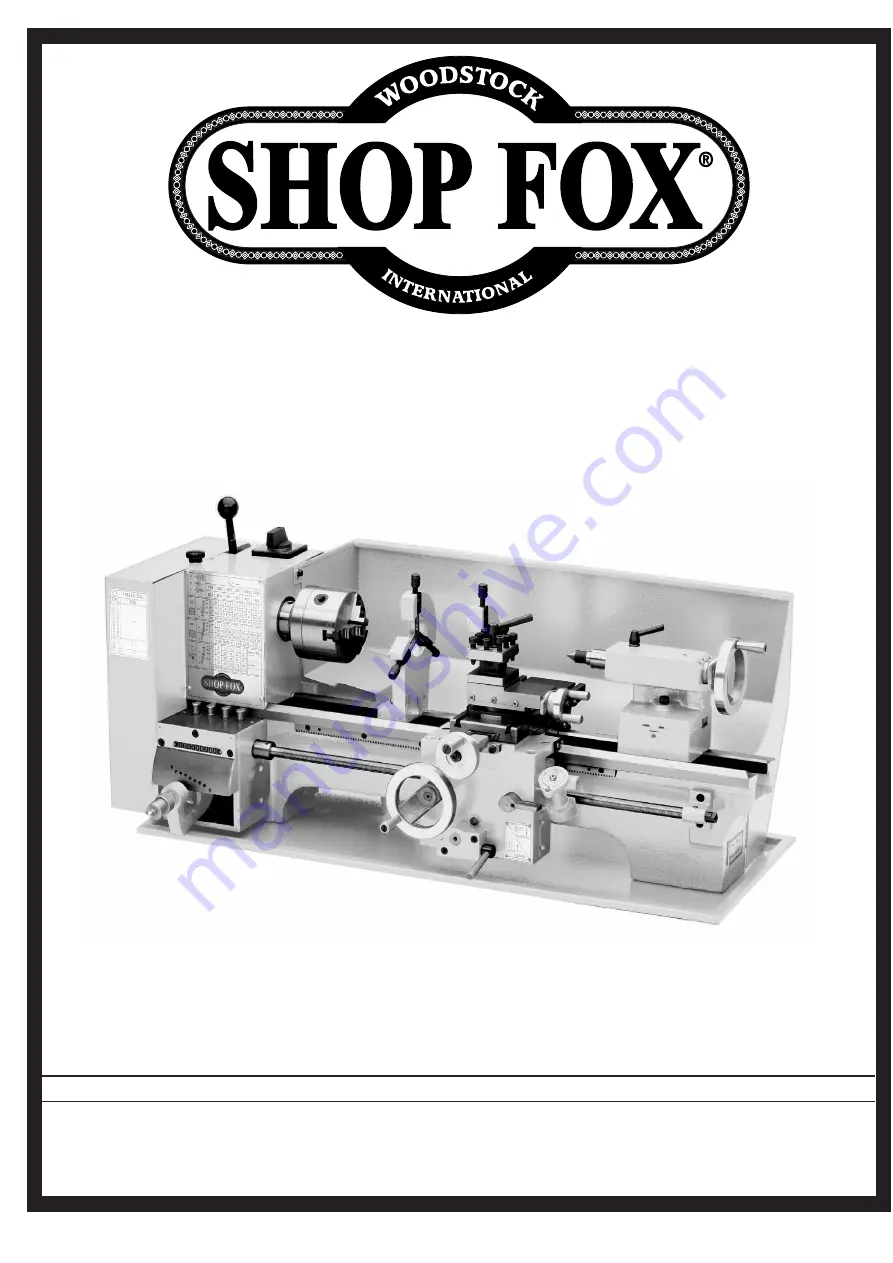
BD9:AB&%).
7:C8=IDEA6I=:
E]dcZ/(+%,()"()-'Dca^cZIZX]c^XVaHjeedgi/iZX]"hjeedgi5h]de[dm#W^o
8DENG><=I?JAN'%%+7NLDD9HID8@>CI:GC6I>DC6A!>C8#!G:K>H:9?JC:!'%&&IH
L6GC>C</CDEDGI>DCD;I=>HB6CJ6AB6N7:G:EGD9J8:9>C6CNH=6E:DG;DGBL>I=DJI
I=:LG>II:C6EEGDK6AD;LDD9HID8@>CI:GC6I>DC6A!>C8#
Eg^ciZY^c8]^cV
-&%+8G
DLC:GHB6CJ6A
;DGBD9:AHB6CJ;68IJG:9H>C8:-$%.
All manuals and user guides at all-guides.com
all-guides.com