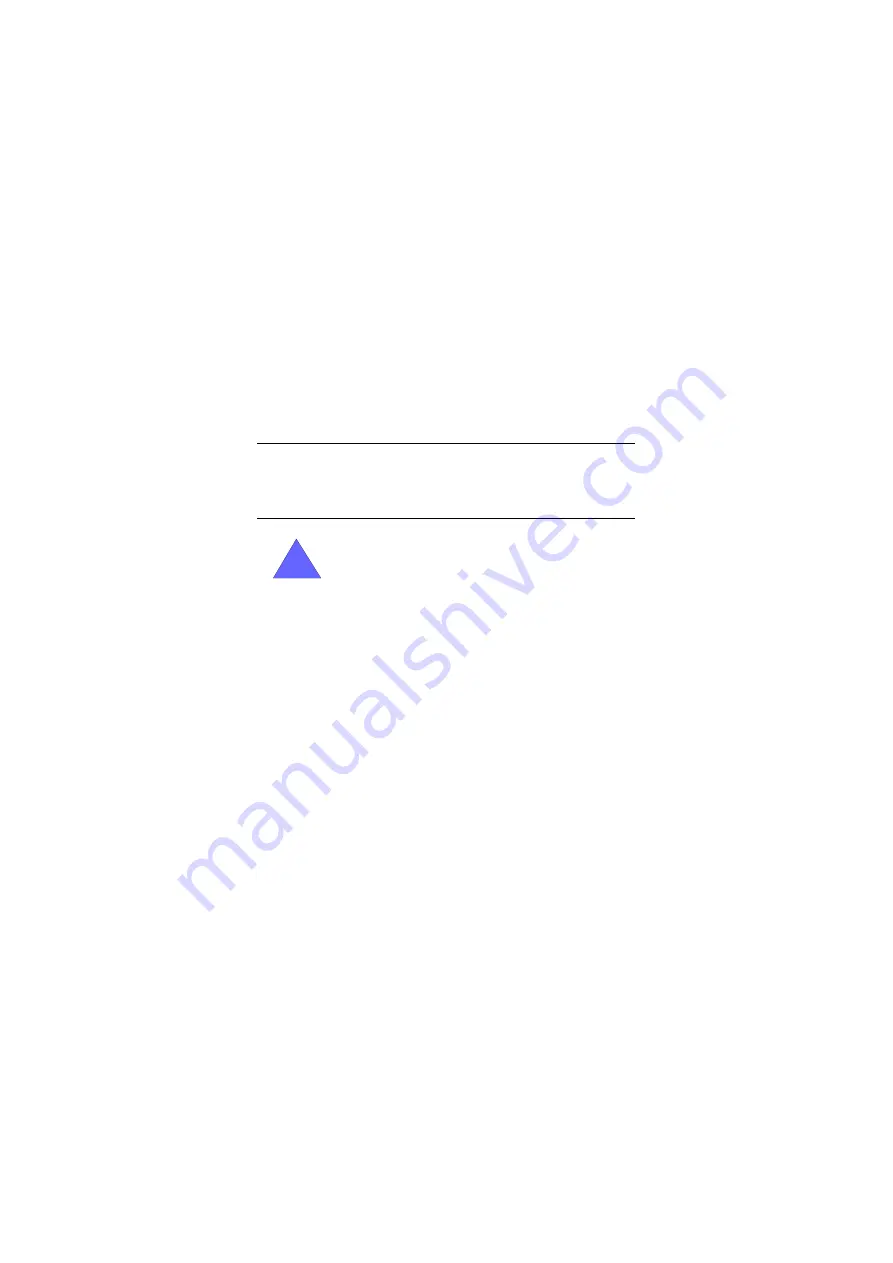
LTAGA-PLCBN SHARPENER
Safety, Operation, Maintenance
& Parts Manual
097032 rev. A.00
Safety is our #1 concern!
Read and understand
all safety information and instructions before oper-
ating, setting up or maintaining this machine.
August 2001
Form #944
!