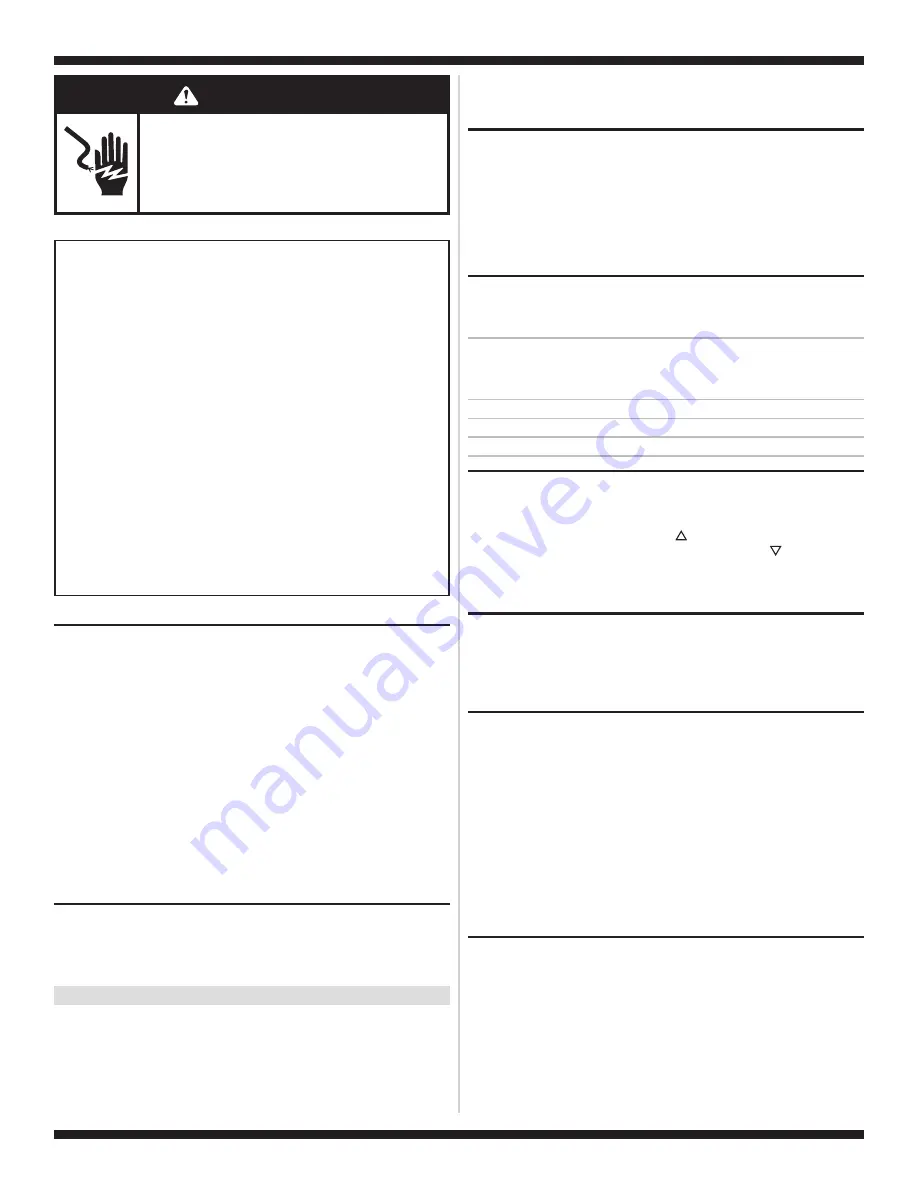
TECH SHEET - DO NOT DISCARD
PAGE 1
W10301482B
.
O
N
T
R
A
P
Y
L
N
O
E
S
U
S
’
N
A
I
C
I
N
H
C
E
T
E
C
I
V
R
E
S
R
O
F
WARNING
Electrical Shock Hazard
Disconnect power before servicing.
Replace all parts and panels before operating.
Failure to do so can result in death or
electrical shock.
IMPORTANT
Electrostatic Discharge (ESD) Sensitive Electronics
ESD problems are present everywhere. ESD may damage or weaken the
machine control electronics. The new control assembly may appear to
work well after repair is finished, but failure may occur at a later date
due to ESD stress.
■
Use an anti-static wrist strap. Connect wrist strap to green ground
connection point or unpainted metal in the appliance
-
OR
-
Touch your finger repeatedly to a green ground connection point or
unpainted metal in the appliance.
■
Before removing the part from its package, touch the anti-static bag
to a green ground connection point or unpainted metal in the
appliance.
■
Avoid touching electronic parts or terminal contacts; handle machine
control electronics by edges only.
■
When repackaging failed machine control electronics in anti-static
bag, observe above instructions.
DIAGNOSTIC GUIDE
Before servicing, check the following:
■
Make sure there is power at the wall outlet.
■
Has a household fuse blown or circuit breaker tripped? Was a regular fuse
used? Use a time-delay fuse.
■
Is dryer vent properly installed and clear of lint or obstructions?
■
All tests/checks should be made with a VOM (volt-ohm-milliammeter) or DVM
(digital-voltmeter) having a sensitivity of 20,000
Ω
per volt DC or greater.
■
Check all connections before replacing components. Look for broken or loose
wires, failed terminals, or wires not pressed into connectors far enough.
■
A potential cause of a control not functioning is corrosion on connections.
Observe connections and check for continuity with an ohmmeter.
■
Connectors: Look at top of connector. Check for broken or loose wires. Check
for wires not pressed into connector far enough to engage metal barbs.
■
Resistance checks must be made with dryer unplugged or power disconnected.
DIAGNOSTIC TESTS
These tests allow factory or service personnel to test and verify all inputs to the
machine control electronics. You may want to do a quick and overall checkup of
the dryer with these tests before going to specific troubleshooting tests.
ACTIVATING THE DIAGNOSTIC TEST MODE
1.
Be sure the dryer is in standby mode (plugged in with all indicators off, or with
only the Done indicator on).
2.
Select any one button (except Power) and follow the steps below, using the
same button (remember the button):
Press/hold
2-5 seconds
➔
Release for
2-5 seconds
➔
Press/hold
2-5 seconds
➔
Release for
2-5 seconds
➔
Press/hold
2-5 seconds
3.
If this test mode has been entered successfully, all indicators on the console
are illuminated for 5 seconds with
showing in the Estimated Time
Remaining two-digit display.
DIAGNOSTIC: Unsuccessful Entry
If entry into diagnostic mode is unsuccessful, press the Power button twice.
➔
If indicators come on, try to use a different button than was used to activate
the diagnostic test mode. If that button fails to enter the diagnostic mode,
something is faulty, and it is not possible to enter the diagnostic mode. Go to
TEST #2, page 4.
➔
If no indicators come on after pressing the Power button, go to TEST #1,
page 4.
DIAGNOSTIC: Saved Fault Codes
If there are saved fault codes, the most recent fault code will alternately show “F-”
and “XX” where XX is the fault code.
Press and release
the same button
used to activate
Diagnostics
➔
beep tone
➔
Second most recent fault code is displayed.
Repeat
➔
beep tone
➔
Third most recent fault code is displayed.
Repeat
➔
beep tone
➔
Fourth most recent fault code is displayed.
Repeat
➔
All indicators momentarily turn off, then stay on.
DIAGNOSTIC: Console Buttons and Indicators
Pressing the console buttons or rotating the cycle selector will sound a beep and
will turn on or off the corresponding indicators as shown in Figure 1, Console
Diagnostics, page 2. Pressing Time Adjust
▲
(more time) will sound a beep and
turn the left digit of the display on or off. Pressing Time Adjust
▼
(less time) will
sound a beep and turn the right digit of the display on or off.
➔
If indicators fail to turn on or off and beep after pressing buttons or rotating
the cycle selector, go to TEST #6, page 8.
DIAGNOSTIC: Door Switch
Opening the door should cause a beep and an alphanumeric number to be
displayed. Closing the door should cause a beep and
to be displayed.
➔
If opening the door fails to cause a beep and a number and letter to be
displayed, go to TEST #7, page 8.
DIAGNOSTIC: Moisture Sensor
1.
Open the door and locate two metal strips on the face of the lint screen
housing. Using a wet cloth or one finger, jointly touch both strips.
➔
If a continuous beep tone is heard and an alphanumeric number is
displayed on the console, the sensor is OK.
➔
If a continuous beep tone is not heard, or if a continuous beep tone is heard
before touching both moisture strips, go to step 2.
2.
Check to see if there is water in the dryer around the moisture strips.
➔
If no water is present, go to TEST#5, page 7.
➔
If water is present, wipe the strips off with a dry cloth and repeat step 1.
➔
If wiping the strips does not stop the beeping, run a timed dry cycle for 2
minutes to dry out the drum, then repeat this diagnostic test.
DIAGNOSTIC: Motor, Heater, and Console ID
Close the door. Press the Start button. The motor and heater will turn on, and the
display will show one of the following console IDs:
c9, ca, cb, cc.
➔
If none of the Console IDs listed above are displayed, replace the user
interface assembly. See Accessing & Removing the Electronic Assemblies,
page 9.
➔
If the motor does not turn on, go to TEST #3, page 4.
➔
If no heat is detected, go to TEST #4, page 6.
88
88