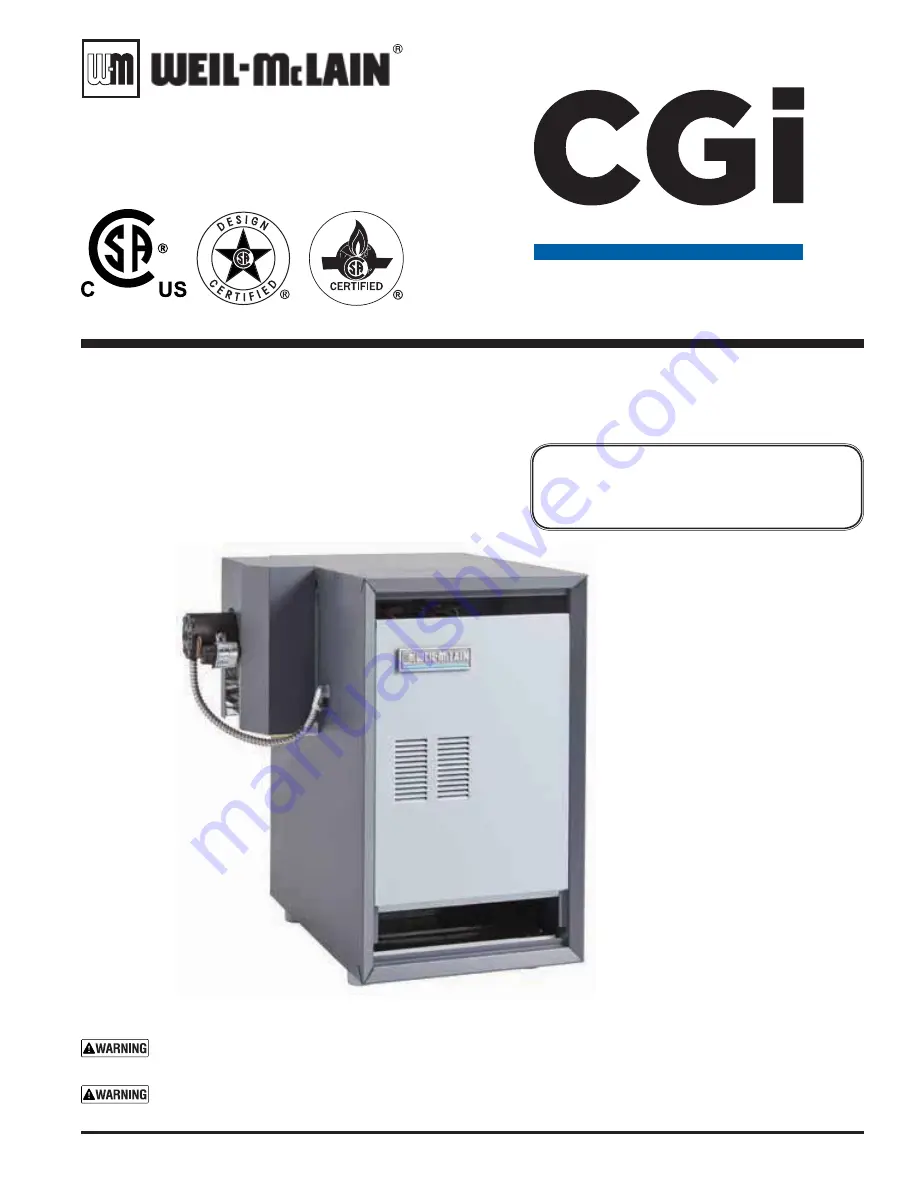
Part Number 550-142-302/0520
DO NOT USE BOILER DURING CONSTRUCTION
unless you provide dust-free air to the boiler area or follow
the requirements given on page 9. Failure to comply could result in severe personal injury, death or substantial property
damage.
This manual must only be used by a qualified heating installer/service technician.
Before
installing
,
read all instructions, including this manual, and any related supplements. Perform steps in the order
given. Failure to comply could result in severe personal injury, death or substantial property damage.
Now With Built In
Low Water Cut Off Functionality
*
Blower cover on sizes CGi 25-6 only
*
Series 4
Gas-Fired Water Boilers
Boiler Manual
• Maintenance
• Parts
• Installation
• Startup