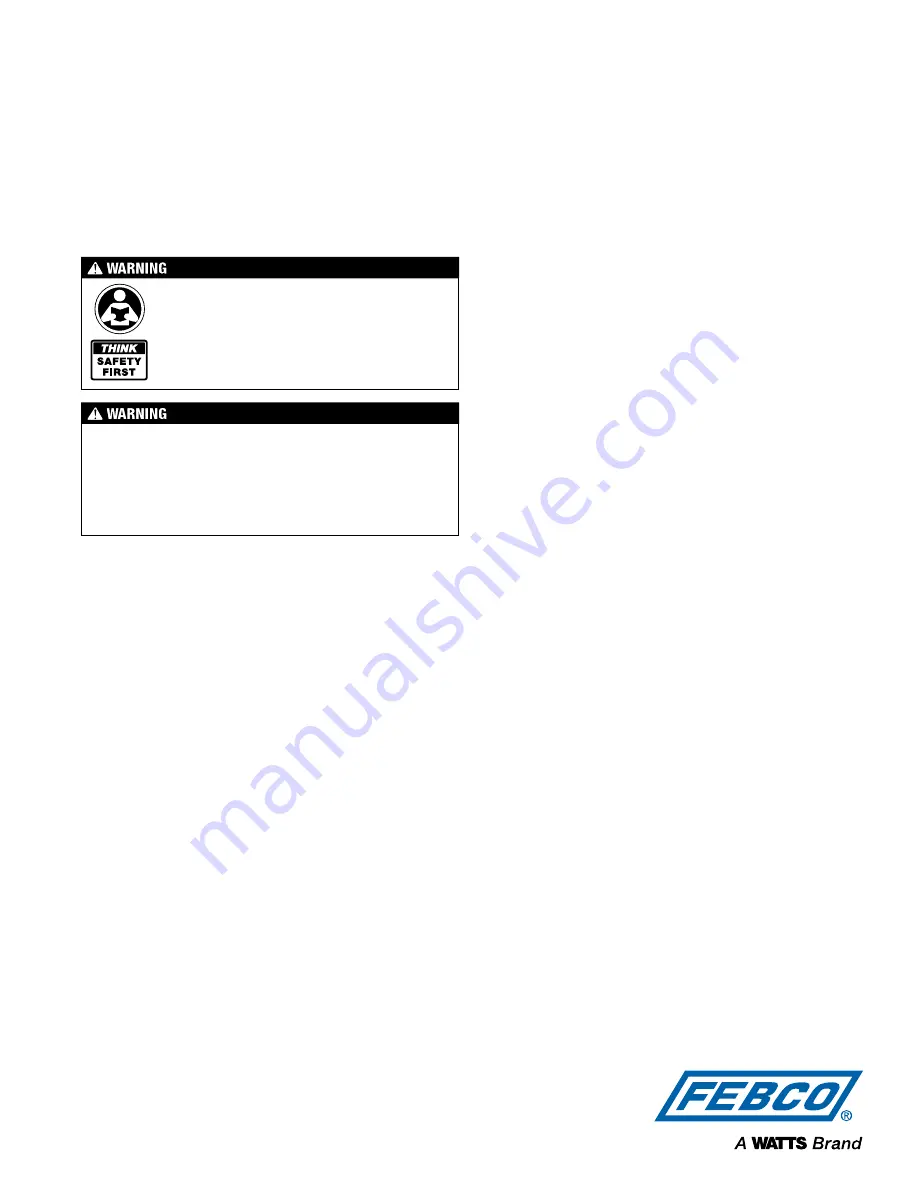
IOM-F-FreezeProtection
Installation, Operation and Maintenance Manual
Freeze Protection
Series 850 Small, LF850 Small
Series 860 Small, LF860 Small
1/2" – 2"
Read this Manual BEFORE using this equipment.
Failure to read and follow all safety and use information
can result in death, serious personal injury, property
damage, or damage to the equipment.
Keep this Manual for future reference.
Local building or plumbing codes may require modifications to
the information provided. You are required to consult the local
building and plumbing codes prior to installation. If the
information provided here is not consistent with local building
or plumbing codes, the local codes should be followed.
This product must be installed by a licensed contractor in
accordance with local codes and ordinances.
Damage from freezing can be costly. FEBCO assemblies are not
warranted against freeze damage. Use the main valve and ball valve
draining procedures to apply freeze protection to Double Check
Valve and Reduced Pressure Zone assemblies.
Guidelines
Backflow prevention assemblies must be protected against freezing for
the winter season in areas where freezing temperatures may occur. If
water inside the assembly freezes, damage to the assembly and the
system may occur.
Proper draining, insulation using heat tape, and heated protective
enclosures are all acceptable methods of freeze protection.
In areas with freezing temperatures, consider installing Series 850U,
860U, LF850U, or LF860U with union end ball valves. The union end
ball valve allows the body of the device to be removed.
When draining an assembly to prevent freezing, remember these
important points:
• The assembly cannot be adequately drained through the test cocks.
For proper draining, follow the Main Valve Draining procedure.
• Drain valves must be added on the inlet and the outlet sides of the
assembly, below the assembly, and preferably below the freeze
line if the remainder of the system is to be drained.
Main Valve Draining
For visual aid information, see Figure 1 when following the Winter
Preparation or the Spring Startup procedure.
Winter Preparation
1. Close the main shutoff valve (A).
2. Open the inlet drain valve (B)
3. Open the inlet and the outlet ball valves (C and D) to the
45 degree (half-open/half-closed) position.
4. Open all test cocks (F).
5. Open the outlet drain valve (E).
6. Remove the cover (G) and the inlet check module until all water
inside the valve drains back through the inlet drain valve (B).
7. Take the followings steps if the piping downstream of the backflow
assembly is blown out with compressed air.
a. Connect the air supply to the outlet drain valve (E) and close the
outlet ball valve (D).
b. After clearing the system with air, partially open the outlet ball
valve (D).
c. Leave all drain valves (E and B), test cocks (F), and ball valves
(C and D) in a half-open/half-closed position for winter.
(For more information, see the Ball Valve Draining procedure.)
d. Make sure the main shutoff valve (A) remains closed and does
not leak.
8. For Reduced Pressure units only. Loosen the relief valve cover (H)
to drain. Tighten the cover when draining is completed.
Spring Startup
When the chance of freeze damage has passed, prepare the
assembly to restore operation.
1. Close all drain valves (E and B), test cocks (F), and ball valves
(C and D).
2. Retighten the relief valve cover (H), then slowly open the main
shutoff valve (A) and the inlet ball valve (C).
3. Slightly open then close all test cocks (F) one at a time to empty
air from the device.
4. Slowly open the outlet ball valve (D) and refill the system.