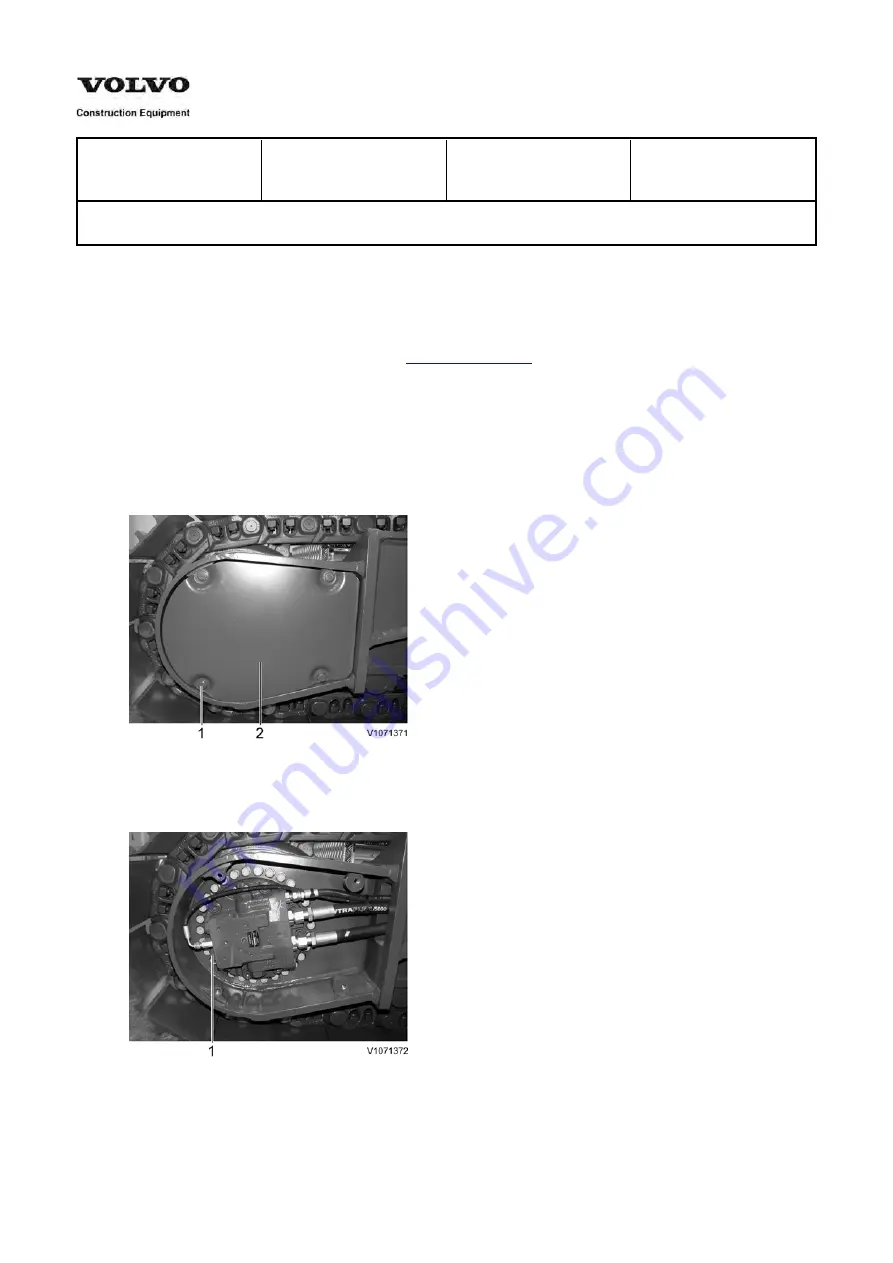
Service Information
Document Title:
Function Group:
Information Type:
Date:
Track motor relief valve,
replacing
Service Information
2014/6/12
Profile:
EXC, EC210B LC [GB]
Track motor relief valve, replacing
Op nbr 441-112
1. Park the machine in the service position F, see
.
091 Service positions
2. When the engine is running, the hydraulic line is under high pressure. Stop the engine, and remove the residual
pressure inside the hydraulic line by the travel control lever smoothly for 3 ~ 4 times with ignition switch at "ON"
position.
NOTE!
Remove the residual pressure inside the hydraulic tank by pressing the air breather on the hydraulic tank.
3. Remove screws (1) and motor cover (2).
Figure 1
Removal, motor cover
4. Remove track motor relief valve (1).
Figure 2
Removal, relief valve
5. Install a new relief valve.
6. Check relief valve pressure of the track motor, and adjust if necessary
Summary of Contents for EC210B LC
Page 14: ...Figure 32 Spring removal ...