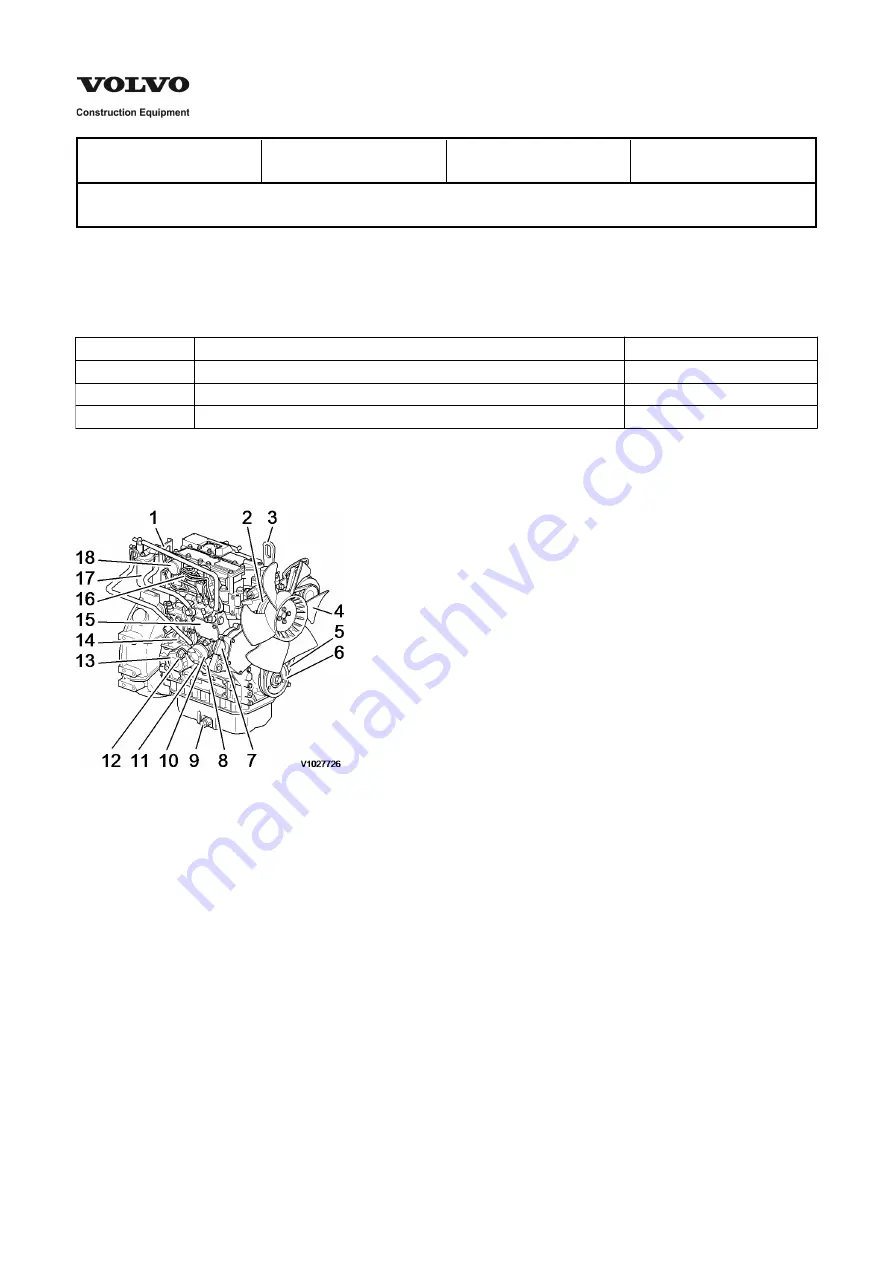
Service Information
Document Title:
Function Group:
Information Type:
Date:
Engine, description
200
Service Information
2014/4/14
Profile:
CEX, ECR28 [GB]
Engine, description
Model code (3TNV76)
Model code
Symbol
Description
Remarks
3
Number of cylinders
TNV
Model series
76
Cylinder bore (mm)
The engine is a 3–cylinder, indirect injected, water cooled diesel engine.
Engine, front view
Figure 1
Engine, front view
1.
2.
3.
4.
5.
6.
7.
8.
9.
10.
11.
12.
13.
14.
15.
16.
17.
18.
Lifting eye
Cooling water pump
Lifting eye
Fan
V-belt
V-pulley
Filler port (lube oil)
Fuel oil inlet
Drain plug (lube oil)
Mechanical fuel feeding pump
Fuel priming lever
Dipstick
Oil filter
Governor lever
Fuel injection pump
Intake manifold
Fuel filter
Air intake port