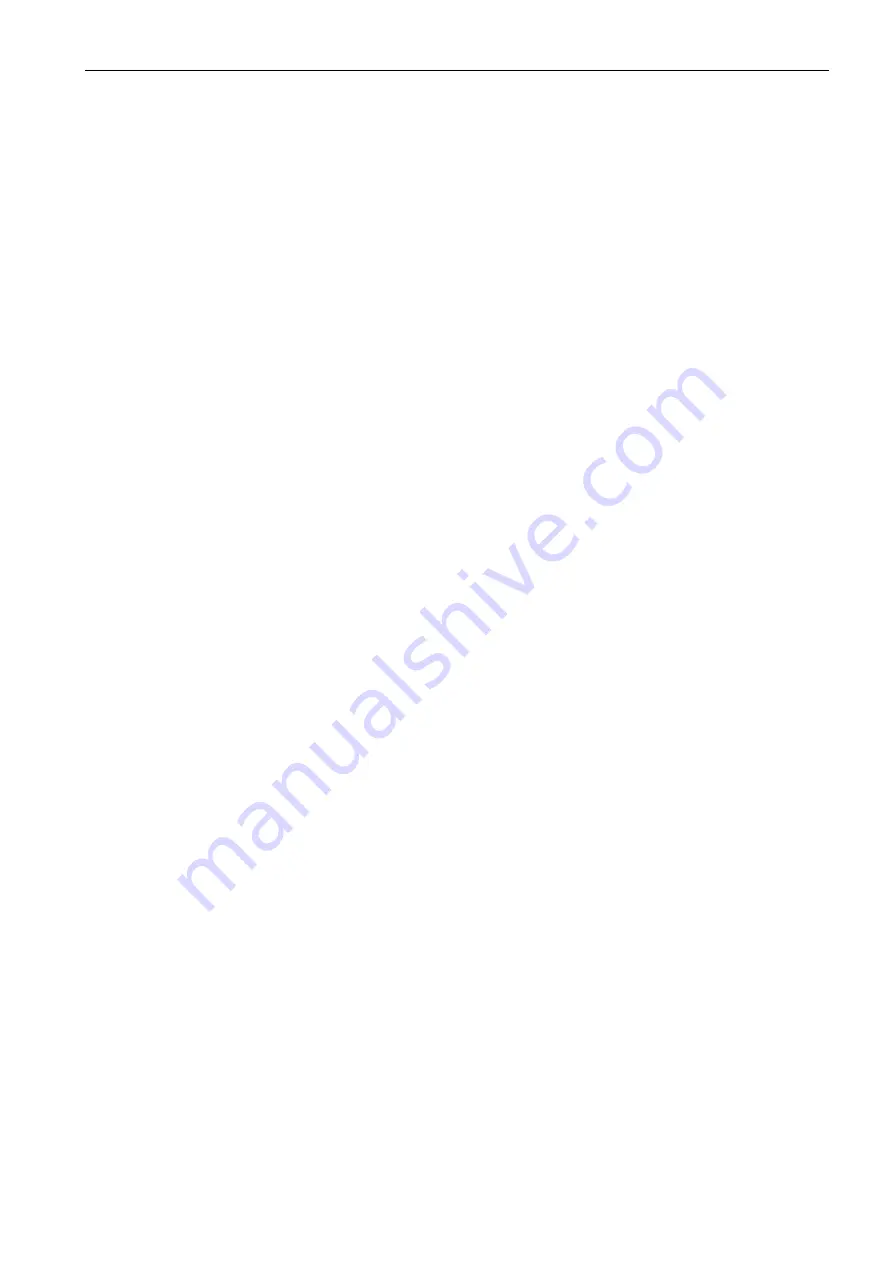
1
Workshop Manual
Industrial Engines
Checks and adjustments
..................................... 82
Engine block ....................................................... 82
Crankshaft, measuring ........................................ 84
Connecting rods, measuring ................................ 87
Pistons ............................................................... 90
Camshaft ............................................................ 93
Camshaft bearings .............................................. 95
Cylinder head ...................................................... 97
Valve seat, changing .......................................... 100
Valve seat, grinding ............................................ 101
Valves, grinding .................................................. 101
Rocker arm bracket ............................................. 102
Control rod .......................................................... 103
Repairing components
........................................ 107
Group 21:
Flywheel ring gear, changing ............................... 107
Valve clearance, checking/adjusting ................... 109
Crankshaft seals, changing (complete engine) .... 111
Front crankshaft seal, changing (front housing) ... 113
Drive belts, adjusting and replacing ..................... 115
Group 22:
Reduction valve, removing .................................. 116
Reduction valve, inserting ................................... 116
Front housing, oil pump ....................................... 117
Engine oil cooler ................................................. 119
Lubricating oil pressure ....................................... 121
Group 23:
Fuel pump, fuel supply pressure check ............... 122
Changing injection pump ..................................... 123
Group 25:
Boost pressure .................................................... 124
Group 26:
Coolant pump ...................................................... 125
Thermostat ......................................................... 127
Wiring diagrams
................................................... 128
Index
..................................................................... 133
Safety information
................................................
2
General information
.............................................
5
Repair instructions
...............................................
6
Special tools
........................................................
9
Engine description
............................................... 12
Location of the engine identification plate ............ 12
Identification plates ............................................. 12
Engine serial number .......................................... 13
Cylinder numbering ............................................. 13
Engine, location of components .......................... 14
Starter motor side ............................................... 14
Service side ........................................................ 15
Lubrication system .............................................. 16
Fuel system ........................................................ 17
Commencement of delivery, Fb .......................... 18
Cooling system ................................................... 19
Technical data
...................................................... 20
Engine ................................................................ 20
Tables ................................................................. 22
Checks and adjustments
..................................... 30
Compression test ................................................ 30
Injectors, checking/adjusting ............................... 31
Disassembly, complete engine
........................... 33
Exposure of engine ............................................. 33
Fitting of fixture ................................................... 34
Engine, disassembly ........................................... 36
Assembly, complete engine
................................ 48
Engine, assembly ............................................... 48
Contents
TD520GE, TAD520GE, TD520VE, TAD520VE,
TAD530/531/532GE, TD720GE, TAD720GE, TD720VE,
TAD720VE, TAD721GE, TAD721VE, TAD722GE,
TAD722VE, TAD730/731/732/733GE