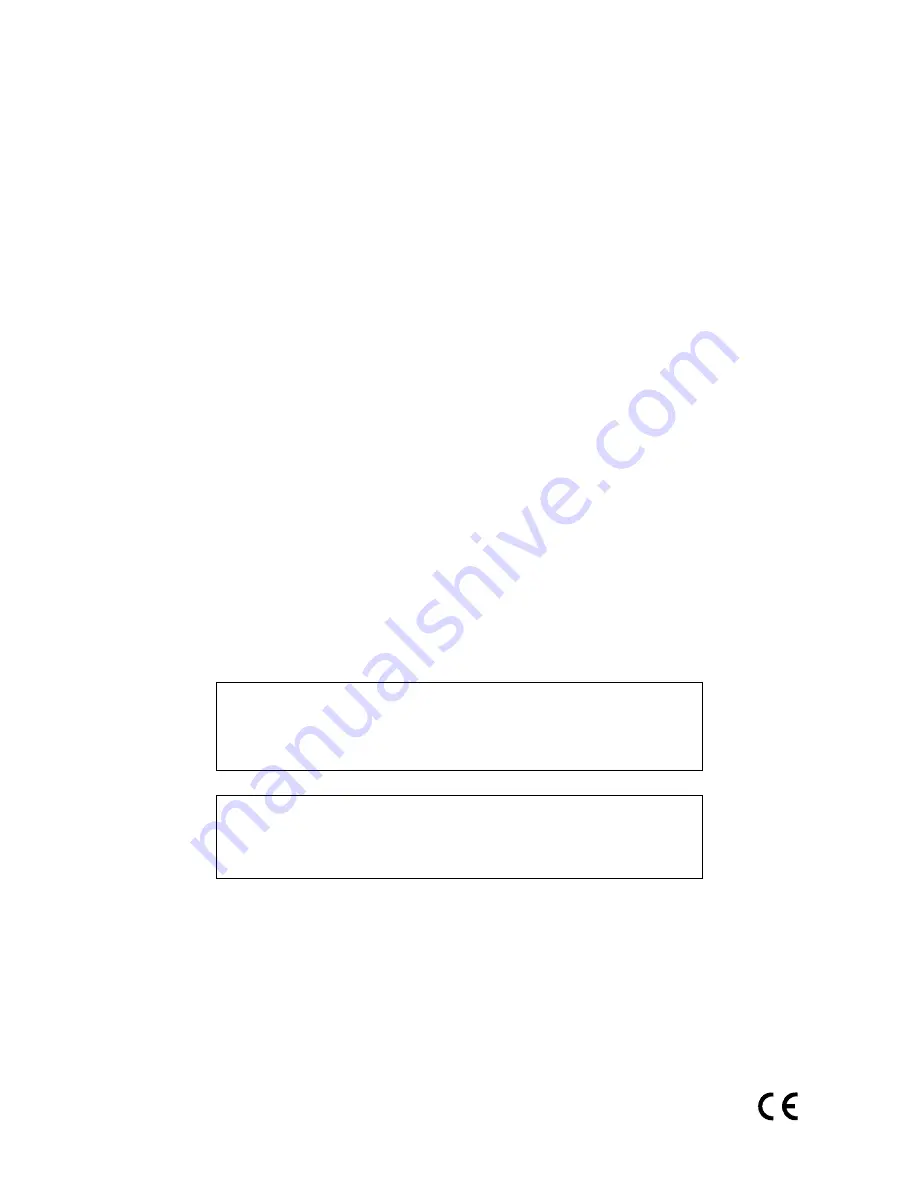
2007 Professional
Systems
Models PLS3.60, PLS4.60,
PLS6.60, & PLS6.120D
Laser Engraving and Cutting System
Safety, Installation, Operation,
and Basic Maintenance Manual
System Serial Number: _____________
(Located on the back of the machine and inside the front door)
Laser Tube Serial Number(s):
______________ ______________
Universal Laser Systems, Inc.
16008 North 81st Street
Scottsdale, AZ 85260 USA
Technical Support Department
Phone: 480-609-0297
Fax: 480-609-1203
Web Based Email Support: www.ulsinc.com
March 2008
Summary of Contents for PLS3.60
Page 8: ......
Page 20: ...SAFETY Section 1 12 ...
Page 21: ...Part 1 Initial Setup ...
Page 22: ......
Page 30: ...INSTALLATION Section 2 10 ...
Page 44: ...GRAPHICS SOFTWARE SETUP Section 3 14 ...
Page 58: ...MAKING A SAMPLE Section 5 4 ...
Page 59: ...Part 2 Laser System Essentials ...
Page 60: ......
Page 70: ...BASIC SYSTEM FEATURES Section 6 12 ...
Page 76: ...BASIC MAINTENANCE Section 7 6 ...
Page 77: ...Part 3 Accessories ...
Page 78: ......
Page 95: ...Part 4 Advanced User ...
Page 96: ......