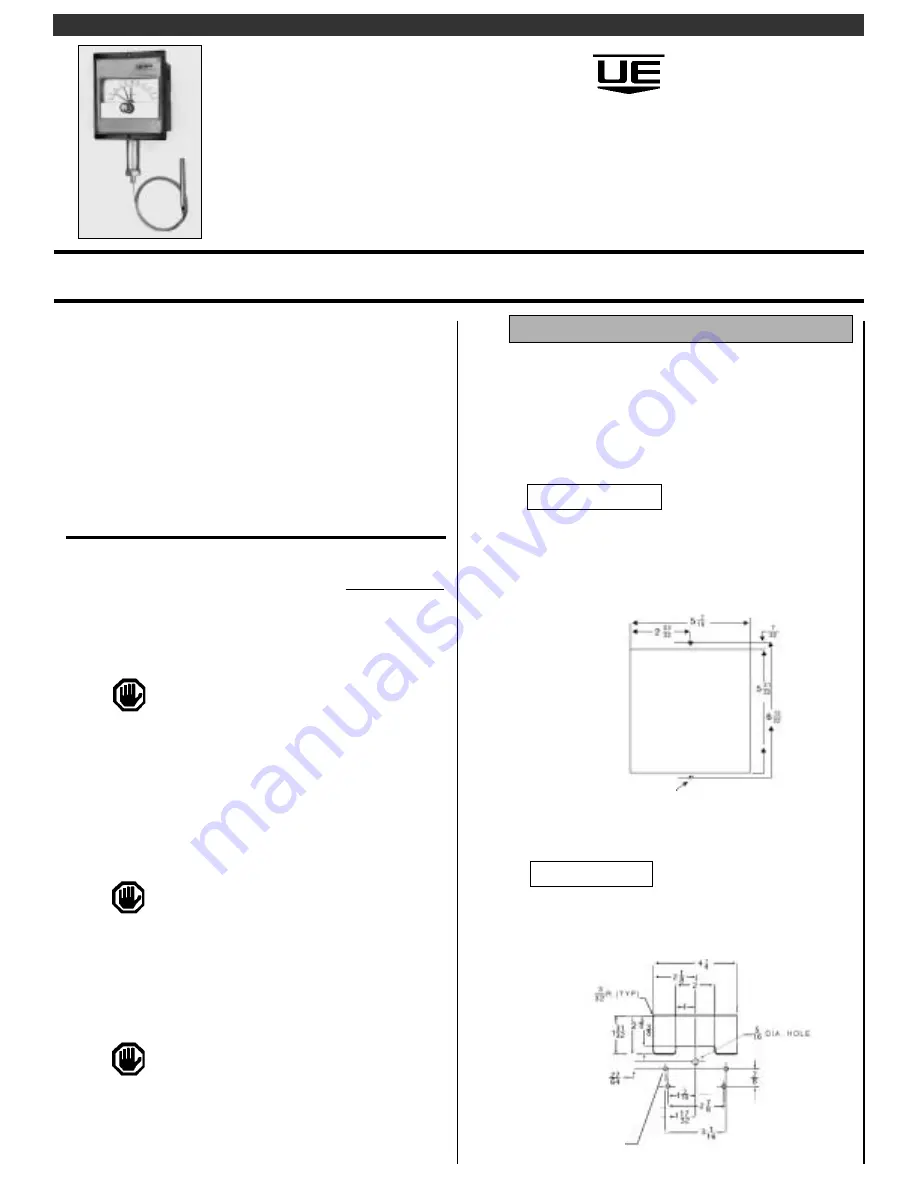
GENERAL
Temperature variations are sensed by the liquid
filled bulb which hydraulically transmits motion
through a mechanism which rotates the indicating
pointer and actuates precision snap-acting
switch(es). Controller settings are made by
turning the adjustment knob(s). Thermometer
types T800 (with enclosure) and T800S
(skeleton) provide temperature indication only
with no control switches.
Tools Needed
Screwdriver to secure
customer supplied screws
Screwdriver
5/64” Allen Wrench
INSTALL UNIT WHERE SHOCK, VIBRA-
TION AND TEMPERATURE FLUCTUA-
TIONS ARE MINIMAL. ORIENT UNIT SO THAT
MOISTURE IS PREVENTED FROM ENTERING
THE ENCLOSURE. IT IS IMPERATIVE THAT
PROPERLY RATED EXPLOSION-PROOF SEAL-
ING FITTINGS BE USED FOR ELECTRICAL
WIRE ENTRY OR 820E AND 822E TYPE UNITS.
DO NOT MOUNT UNIT IN AMBIENT TEMPERA-
TURES EXCEEDING PUBLISHED LIMITS.
PREVENTATIVE MAINTENANCE / PERIODIC
TESTING (6 MONTHS OR SOONER AS DIC-
TATED BY THE ENVIRONMENT) IS NECESSARY
TO ENSURE OPERATION OF THE PRODUCT TO
SPECIFICATION. LUBRICATE ALL PIVOT POINTS
AND MOVING PARTS, TO PREVENT CORROSION,
WITH COMPATIBLE DRY LUBRICANTS OR LIGHT
GREASE.
DO NOT KNOCKOUT ANY PLUGS ON
EXPLOSION-PROOF TYPES 820E OR 822E
When mounting 800 or 802 type controls, it may be
necessary to remove adjustment knob and front cover.
The knob is secured with a 5/64” Allen Setscrew. The
cover is secured by four screws at the corners.
MOUNTING
The controller may be mounted in any position to
either a surface or panel (1/4” thick maximum).
Locate it where vibration, shock and ambient
temperature fluctuations are minimal. It is recom-
mended that mounting the unit with the conduit
connection on the top be avoided.
To Flush Mount
(Not applicable to explosion-proof types)
Cut out the panel as shown in Figure 1A. Mount
to the panel using the two holes located on the
flange of the enclosure.
To Panel Mount
(Skeletons)
Prepare the cut out, drilling the holes for the knob
shaft and the mounting holes per Figure 1B.
U N I T E D E L E C T R I C
C O N T R O L S
Installation and Maintenance
Instructions
IM800-03
Please read all instructional literature carefully and thoroughly before starting. Refer to the final page for the listing of
Recommended Practices, Liabilities and Warranties.
800 Series
Temperature Controllers and
Thermometers
Types 800, 800S, T800, T800S, 802,
802S, 802P, 802PS, 820E*, 822E*
*Explosion-Proof Class I, Groups B, C, D;
Class II, Groups E, F & G; Class III
Part I - Installation
Figure 1A - Flush Mounting
Figure 1B - Panel Mounting (Skeleton)
Clearance for #6 screw
(4) places (3/16 Max.
Panel Thickness)
Clearance for #8 screw - (2) places