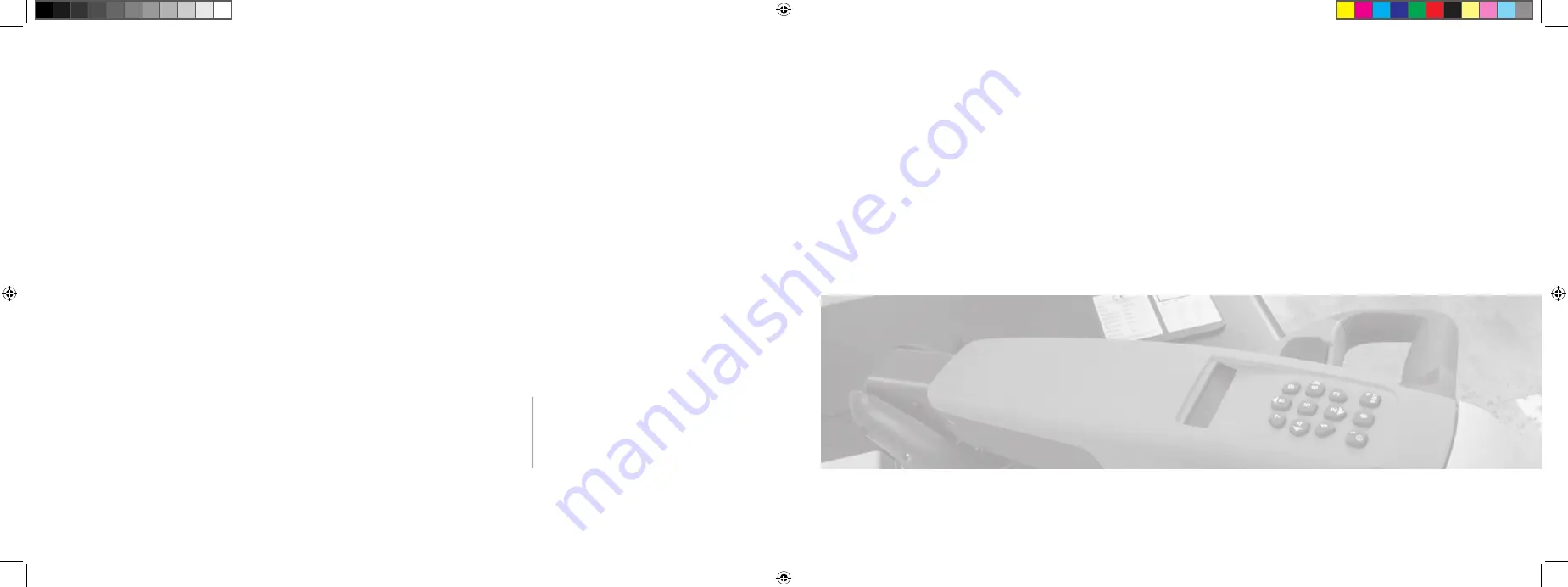
Subsidiary/Dealer
PLL • PLE • PSD • PSL
•
PS
•
PSH
•
PLP
•
TS
Instruction handbook
UniCarriers Europe AB
SE-435 82 Mölnlycke
Sweden
Phone +46 (0)31 98 40 00
[email protected]
www.unicarriers.com
P/N: 159147, Rev. A
GB
l002_handbook_Brandless_språk_Pedestrian_150227.indd All Pages
2015-03-27 10:28:53