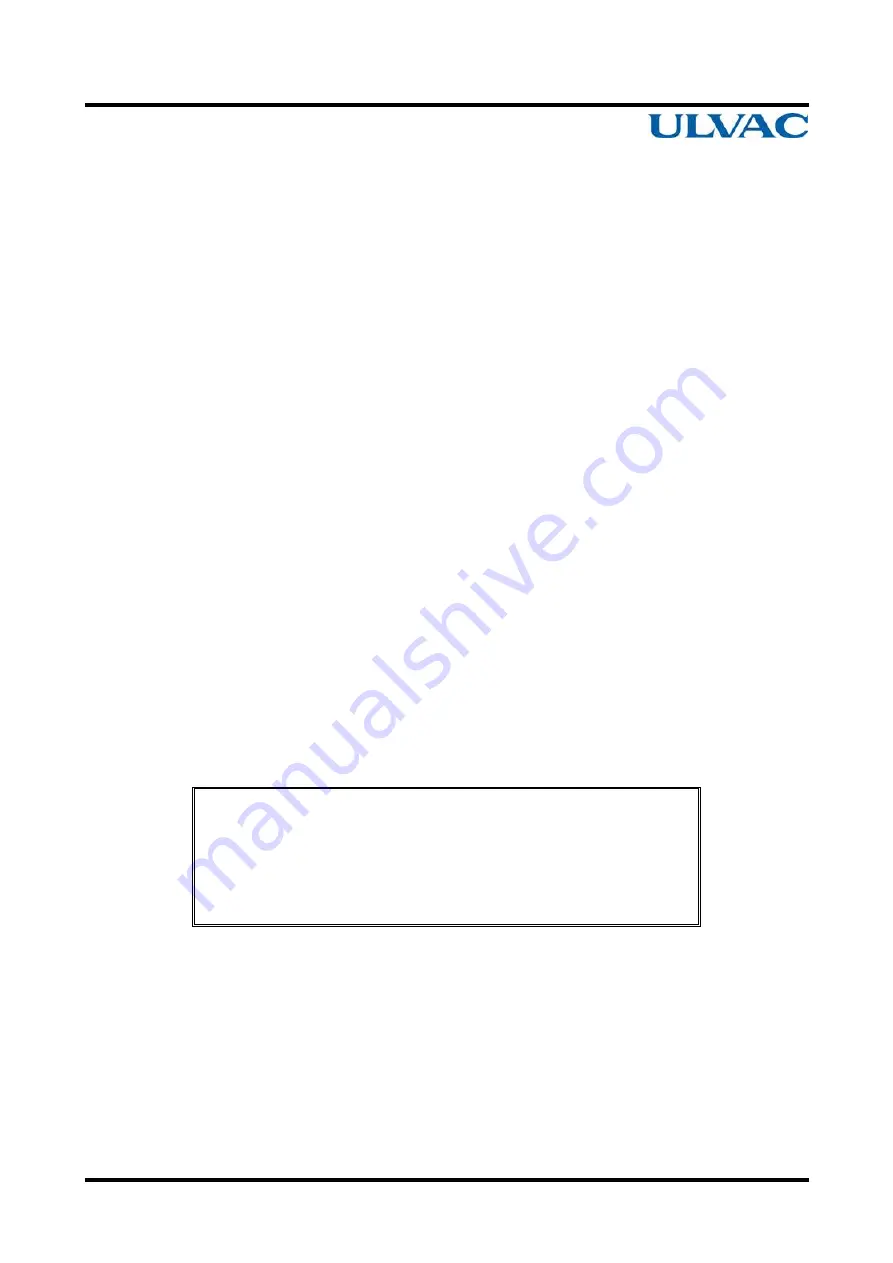
YK11-0016-DI-002-09
INSTRUCTION MANUAL
MECHANICAL BOOSTER PUMP
PMB100D
PMB300D
1)
PMB600D
1)
PMB1200D
1)
PMB2400D
1)
1)
IE3 motor adoption
Before using this product, be sure to read this operation manual.
Keep this manual with care to use at any time.
ULVAC, Inc.
Components Division
http://www.ulvac.co.jp/
Summary of Contents for PMB100D
Page 2: ......
Page 3: ...Declaration of Conformity...
Page 39: ...YK11 0016 DI 002 08 12 2 4 Dimensional drawing Fig 11 Dimensional drawing PMB100D...
Page 40: ...YK11 0016 DI 002 08 13 Fig 12 Dimensional drawing PMB300D...
Page 41: ...YK11 0016 DI 002 08 14 Fig 13 Dimensional drawing PMB600D...
Page 42: ...YK11 0016 DI 002 08 15 Fig 14 Dimensional drawing PMB1200D...
Page 43: ...YK11 0016 DI 002 08 16 Fig 15 Dimensional drawing PMB2400D...
Page 62: ...YK11 0016 DI 002 08 35...
Page 65: ...YK11 0016 DI 002 08 38...
Page 72: ...YK11 0016 DI 002 08 45...
Page 84: ...YK11 0016 DI 002 08 57 Fig 28 PMB300D Optional attachment figure...
Page 85: ...YK11 0016 DI 002 08 58 Fig 29 PMB600D Optional attachment figure...
Page 86: ...YK11 0016 DI 002 08 59 Fig 30 PMB1200D Optional attachment figure...
Page 89: ...YK11 0016 DI 002 08 62 Fig 33 Dimensional drawing PMB2400D Horizontal exhaust model...
Page 99: ...YK11 0016 DI 002 08 72...
Page 105: ...YK11 0016 DI 002 08 78...
Page 119: ......