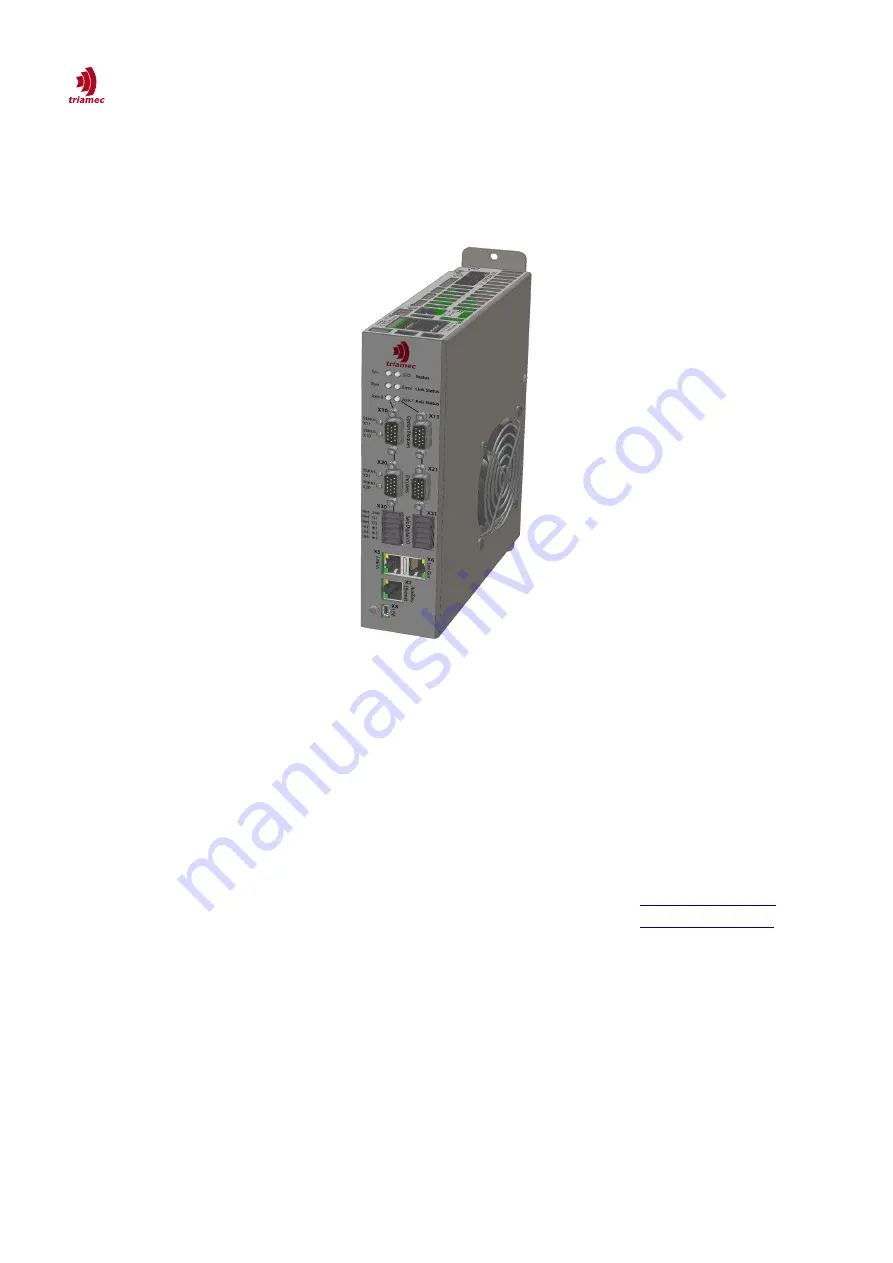
Hardware Manual
TSD80 / TSD85 / TSD130 Revision 4
Keep all manuals belonging to this product during its life span. Pass all manuals to future owners and
users of this product. This English version is the original version of the product manual.
Document
HWTSD80-TSD130_4_HardwareManual_EP
Version
006
Destination T:\doc\Hardware
Owner
up
Copyright © 2018
Triamec Motion AG
All rights reserved.
Triamec Motion AG
Industriestrasse 49
6300 Zug / Switzerland
Phone
+41 41 747 4040
Web
Disclaimer
This document is delivered subject to the following conditions and restrictions:
This document contains proprietary information belonging to Triamec Motion AG. Such information
is supplied solely for the purpose of assisting users of Triamec products.
The text and graphics included in this manual are for the purpose of illustration and reference only.
The specifications on which they are based are subject to change without notice.
Information in this document is subject to change without notice.
2022-01-27