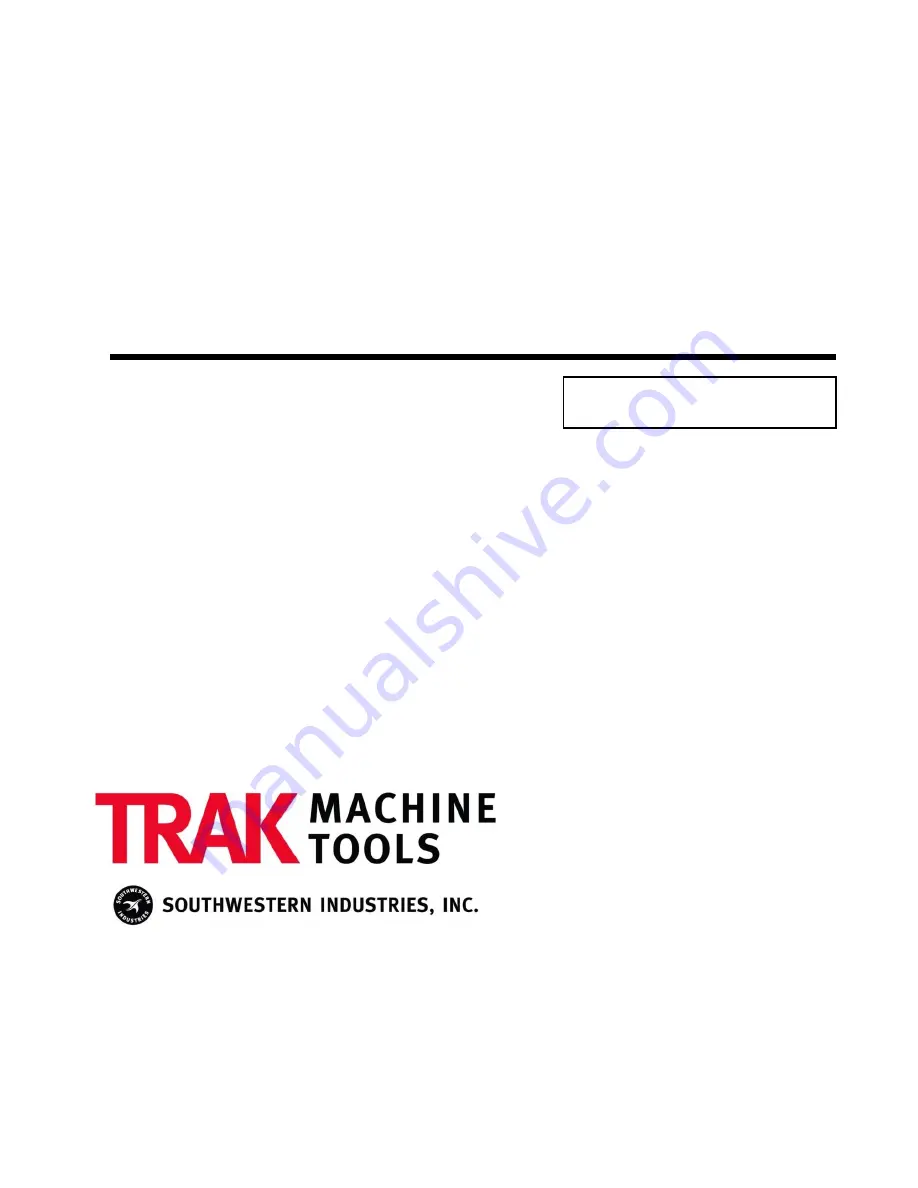
TRAK
®
3ntr 3D Printers
Maintenance & Troubleshooting Manual
Covers Current Models:
•
3ntr A2
•
3ntr A4
2615 Homestead Place
Rancho Dominguez, CA 90220-5610 USA
T | 310.608.4422
|
F | 310.764.2668
Service Department: 800.367.3165
e-mail: [email protected] | [email protected] | web: www.trakmt.com
Document:
P/N 32241
Version:
121820