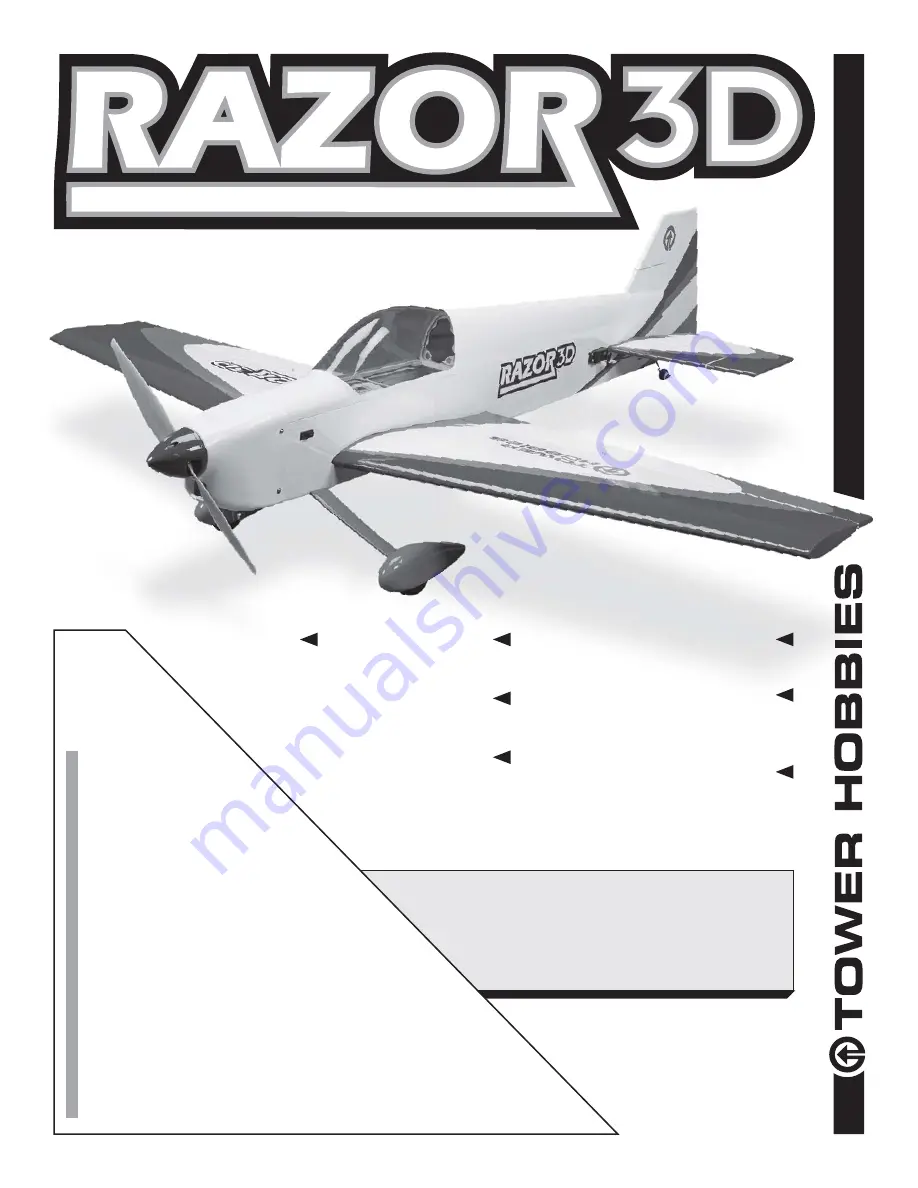
I N S T R U C T I O N M A N U A L
READ THROUGH THIS MANUAL
BEFORE STARTING CONSTRUCTION.
IT CONTAINS IMPORTANT INSTRUCTIONS
AND WARNINGS CONCERNING THE
ASSEMBLY AND USE OF THIS MODEL.
WEIGHT
5 – 5.5 lb [2270 – 2490 g]
WING LOADING
20 – 22 oz/sq ft [61 – 67 g/dm
2
]
RADIO
4-channel minimum with 4-5 servos
and standard size receiver
ENGINE / MOTOR
.46 –.55 cu in [7.5 – 9cc] two-stroke engine,
.70 –.81 cu in [11.5 –13.5cc] four-stroke engine,
RimFire .55 (42-60-480) brushless out-runner motor
To w e r
Hobbies
®
guarantees
this kit to be
free from defects
in both material and
workmanship at the
date of purchase. This
warranty does not cover any
component parts damaged by
use or modification. In no case
shall Tower Hobbies’ liability exceed
the original cost of the purchased kit.
Further, Tower Hobbies reserves the right to
change or modify this warranty without notice.
In that Tower Hobbies has no control over the final
assembly or material used for final assembly, no
liability shall be assumed nor accepted for any damage
resulting from the use by the user of the final
user-assembled product. By the act of using the
user-assembled product, the user accepts all resulting liability.
If the buyer is not prepared to accept the liability associated with the
use of this product, the buyer is advised to return this kit immediately in
new and unused condition to the place of purchase.
To make a warranty claim send the defective part or item to Hobby Services at
the address below:
(OBBY3ERVICESs.!POLLO$R3UITEs#HAMPAIGN),s53!
Include a letter stating your name, return shipping address, as much contact information
as possible (daytime telephone number, fax number, e-mail address), a detailed description
OF THE PROBLEM AND A PHOTOCOPY OF THE PURCHASE RECEIPT 5PON RECEIPT OF THE PACKAGE THE
problem will be evaluated as quickly as possible.
WA
R
R
A
N
T
Y
Entire Contents
© 2011 Tower Hobbies
TOWA2055MNL V1.0
®
®
™
TOWER HOBBIES
#HAMPAIGN)LLINOIS
EXT
WINGSPAN
52 in [1320mm]
WING AREA
579 sq in [37.3 dm
2
]
LENGTH
54.5 in [1385mm]