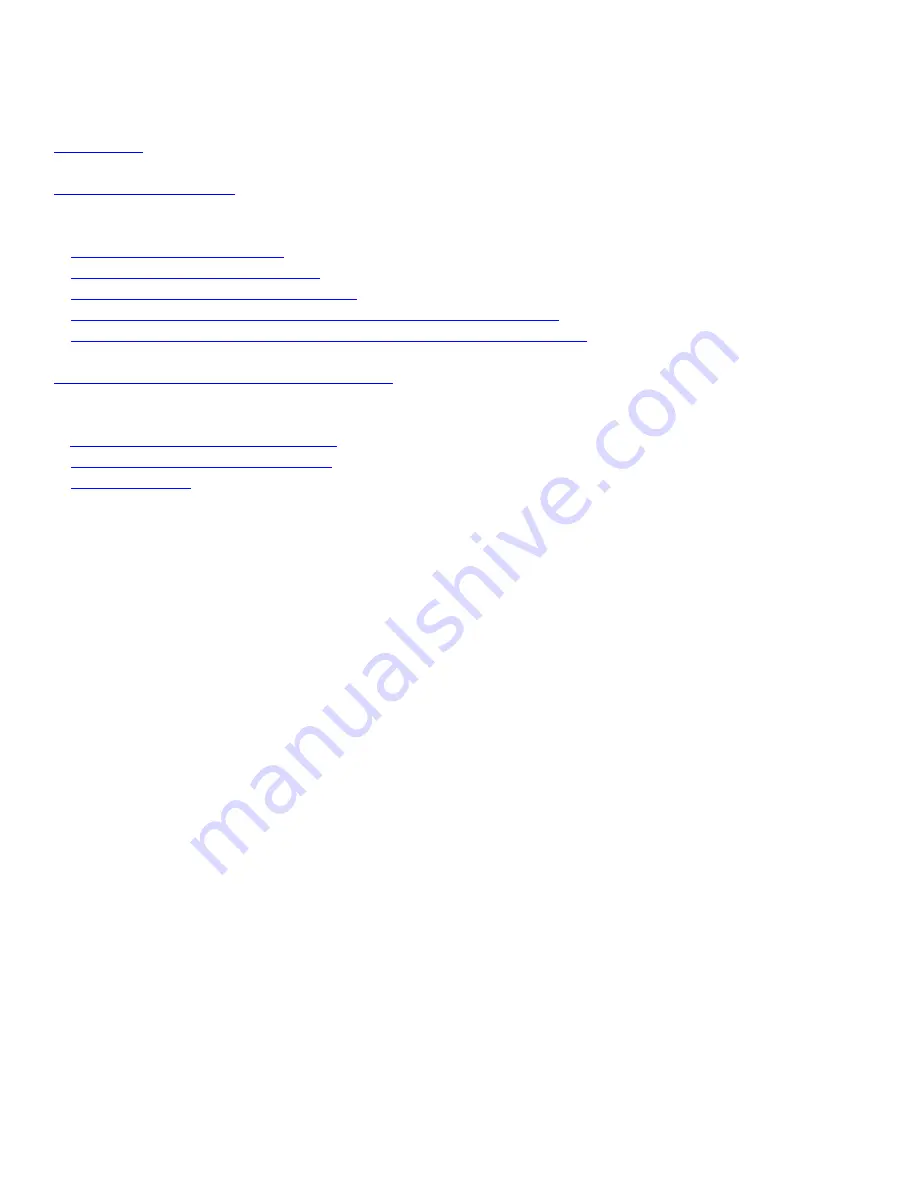
GAS TRIMMER GUIDE, MODELS 51630, 51603, 51604
Table of Contents – Page 1 of 1
MAINTENANCE PROCEDURES
FLEXIBLE DRIVE SHAFT MAINTENANCE
CARBURETOR ADJUSTMENTS -- MODEL TC-1 500 WITH TILLOTSON
CARBURETOR ADJUSTMENT -- MODELS TC-300, TC-400 WITH WALBRO
TROUBLESHOOTING AND TEST PROCEDURES
DISASSEMBLY, REPAIR, REASSEMBLY INSTRUCTIONS