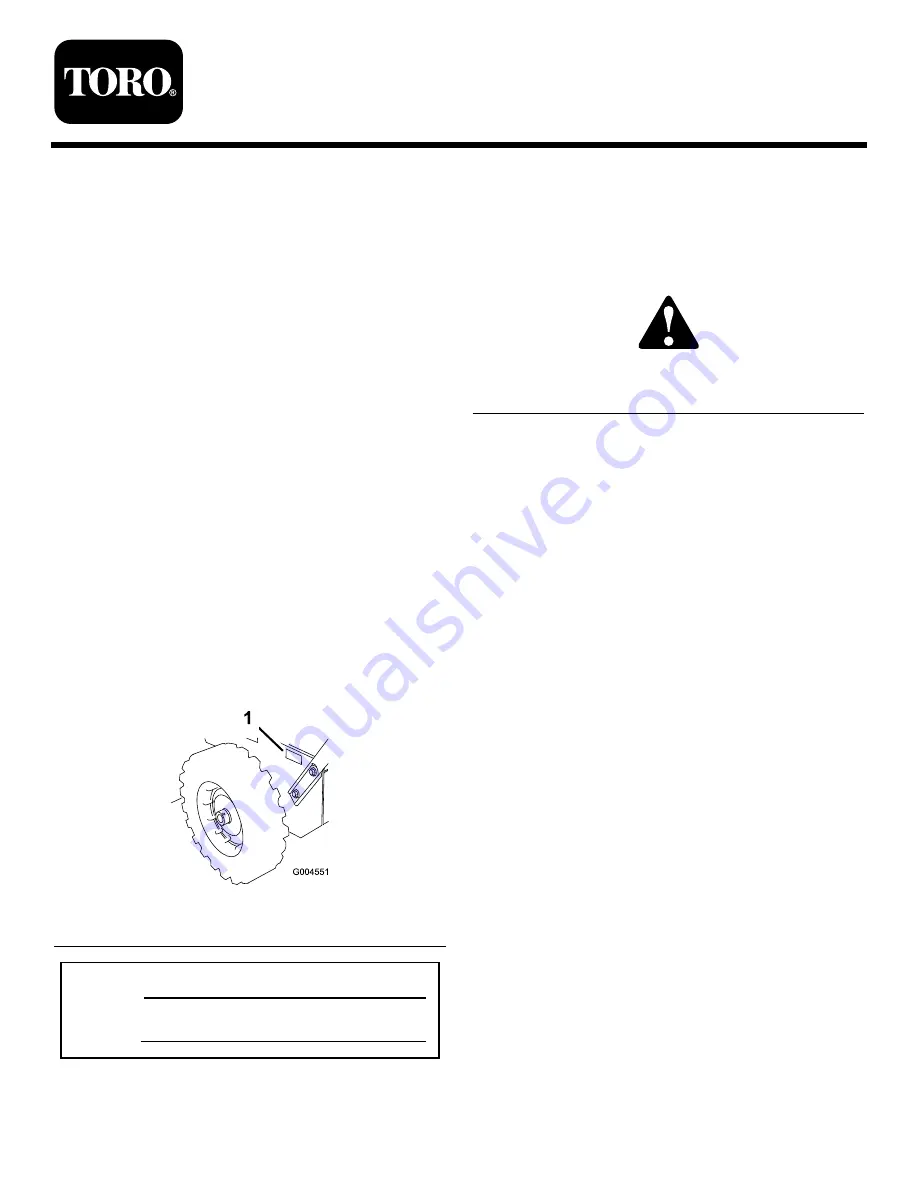
Form No. 3365-707 Rev A
722 Power Throw
®
Snowthrower
Model No. 38608—Serial No. 311000001 and Up
Operator's Manual
Introduction
This machine is intended to be used by residential
homeowners or professional, hired operators. It
is designed primarily for removing snow from
paved surfaces, such as driveways and sidewalks,
and other surfaces for traffic on residential or
commercial properties. It is not designed for
removing materials other than snow, nor is it
designed for clearing off gravel surfaces.
Read this information carefully to learn how to operate
and maintain your machine properly and to avoid injury
and machine damage. You are responsible for operating
the machine properly and safely.
You may contact Toro directly at www.Toro.com for
machine and accessory information, help finding a
dealer, or to register your machine.
Whenever you need service, genuine Toro parts, or
additional information, contact an Authorized Service
Dealer or Toro Customer Service and have the model
and serial numbers of your machine ready. Figure 1
identifies the location of the model and serial numbers
on the machine. Write the numbers in the space
provided.
Figure 1
1.
Model and serial number location
Model No.
Serial No.
This manual identifies potential hazards and has
safety messages identified by the safety alert symbol
(Figure 2), which signals a hazard that may cause serious
injury or death if you do not follow the recommended
precautions.
Figure 2
1.
Safety alert symbol
This manual uses 2 words to highlight information.
Important
calls attention to special mechanical
information and
Note
emphasizes general information
worthy of special attention.
Replacement Engine Owner’s Manuals may be
ordered through the engine manufacturer.
© 2010—The Toro® Company
8111 Lyndale Avenue South
Bloomington, MN 55420
Register at www.Toro.com.
Original Instructions (EN)
Printed in the USA
All Rights Reserved