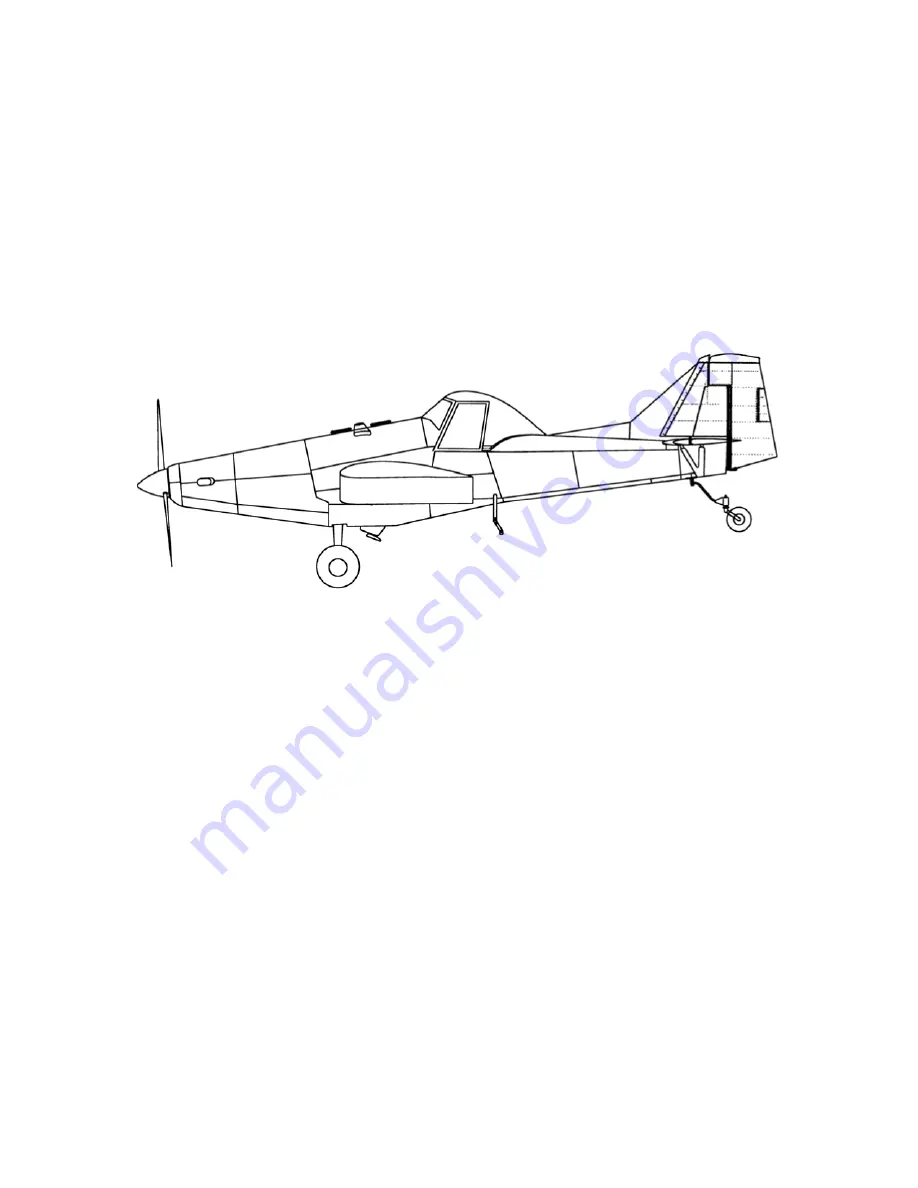
THRUSH AIRCRAFT INC - T660 TURBO THRUSH
AIRCRAFT MAINTENANCE MANUAL
Effective: 01/10/05
i
THRUSH AIRCRAFT INC.
TURBO THRUSH
AIRCRAFT MAINTENANCE MANUAL
Model S2R – T660
Serial Numbers T660 – 109 & Up
Manual Number: T660 -3
Issued December 17, 2003
Revised January 10, 2005
Note:
All serial numbers with the DC suffix indicate the dual cockpit configuration.
Manufacturer’s Serial Number:_____________________________________________
Registration Number: ____________________________________________________
Summary of Contents for S2R-T660
Page 6: ......
Page 17: ...THRUSH AIRCRAFT INC T660 TURBO THRUSH AIRCRAFT MAINTENANCE MANUAL Effective 12 17 03 1 10...
Page 71: ...THRUSH AIRCRAFT INC T660 TURBO THRUSH AIRCRAFT MAINTENANCE MANUAL Effective 12 17 03 2 53...
Page 160: ...Figure 6 2 Effective 09 02 04 6 20...
Page 162: ...THRUSH AIRCRAFT INC T660 TURBO THRUSH AIRCRAFT MAINTENANCE MANUAL Effective 12 17 03 6 22...
Page 199: ...THRUSH AIRCRAFT INC T660 TURBO THRUSH AIRCRAFT MAINTENANCE MANUAL R1 Effective 12 17 04 7 36...
Page 241: ...THRUSH AIRCRAFT INC T660 TURBO THRUSH AIRCRAFT MAINTENANCE MANUAL 9 11 Effective 12 17 03...
Page 300: ......