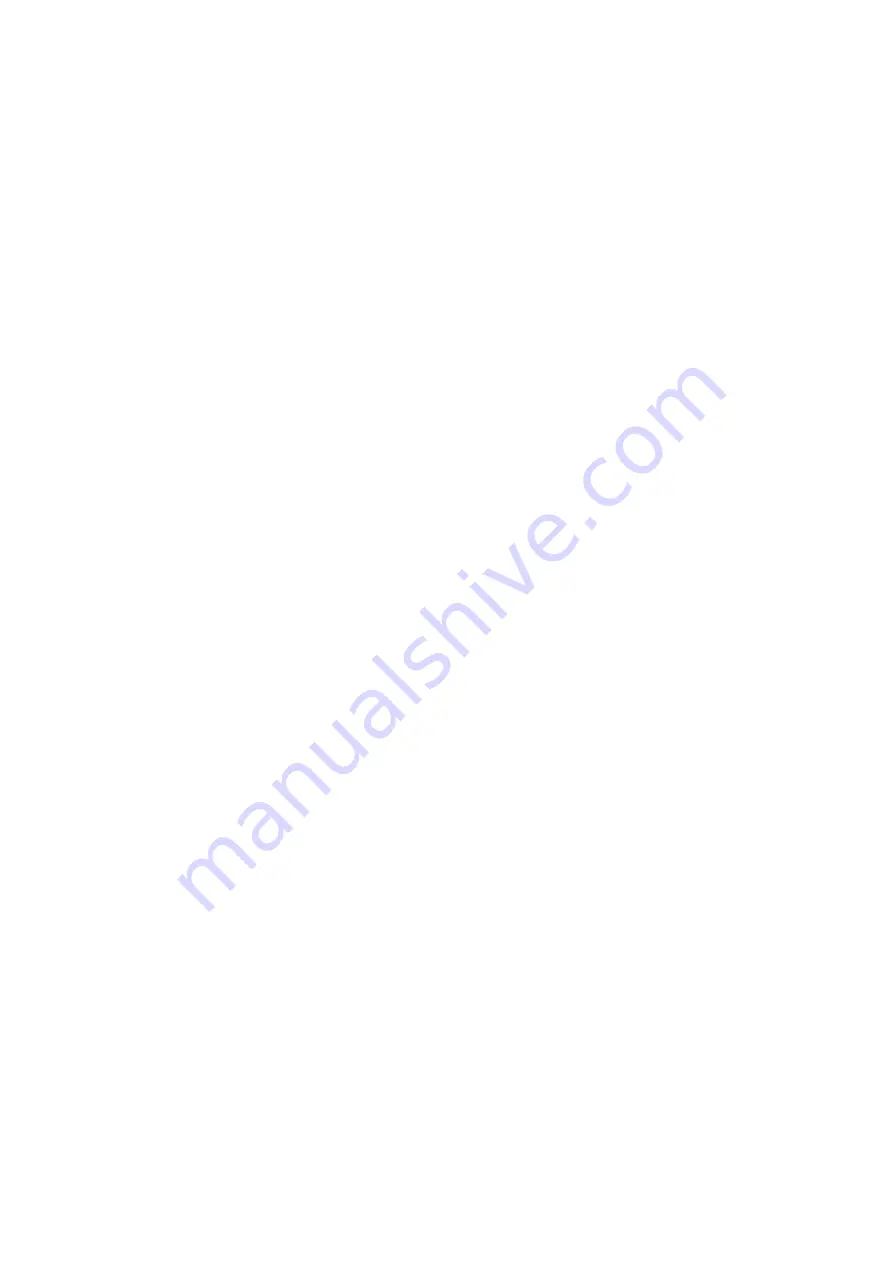
1
CONTENT
1. REGULAR INSPECTION -----------------------------------------
2
1-1 Delivery Introduction ---------------------------------------------------2
1-2 Inspection Before Running -------------------------------------------4
1-3 Regular Inspection ------------------------------------------------------5
1-4 General Inspection ------------------------------------------------------6
2. MAINTENANCE INFORMATION------------------- ------------
7
2-1 Specification Sheet -----------------------------------------------------7
2-2 Maintenance Data ---------------------------- ---------------------------8
2-3 Special Tools --------------------------------------------------------------9
2-4 List of Grease & Oil Adopted ----------------------------------------12
2-5 Circuit Drawings ---------------------------------------------------------13
2-6 Tighting Torque of Screws---------------------------------------------14
2-7 Simplified Troubleshooting -------------------------------------------16
2-8 Troubleshooting ----------------------------------------------------------17
3. DESCRIPTION OF COMPONENTS AND ASSEMBLY ---
25
3-1 Cover and Seat -----------------------------------------------------------26
3-2 Engine ----------------------------------------------------------------------27
3-3 Transmission Mechanism --------------------------------------------30
3-4 Electric System -----------------------------------------------------------35
3-5 Body --------------------------------------------------------------------------37
4. DISASSEMBLY REPAIRMENT
------------ ------------------------39
4-1 Notice for Disassembly Repairment ------------------------------40
4-2 Removal and lnstallation of Engine -------------------------------41
4-3 Disassembly and Assembly of Engine ---------------------------43
4-4 Removal and Assembly of Carburetor ---------------------------73
4-5 Removal and Inspection and Assembly of Electric Parts --75
4-6 Removal and Inspection and Assembly of Body Parts -----80
Summary of Contents for Hornet 50
Page 9: ...9 2 3 Special Tools ...
Page 10: ...10 2 3 Special Tools ...
Page 11: ...11 2 3 Special Tools ...
Page 13: ...13 2 5 Circuit Drawing ...
Page 17: ...17 ...
Page 18: ...18 ...
Page 20: ...20 2 8 2 Troubleshooting for poor skip of spark plugs ...