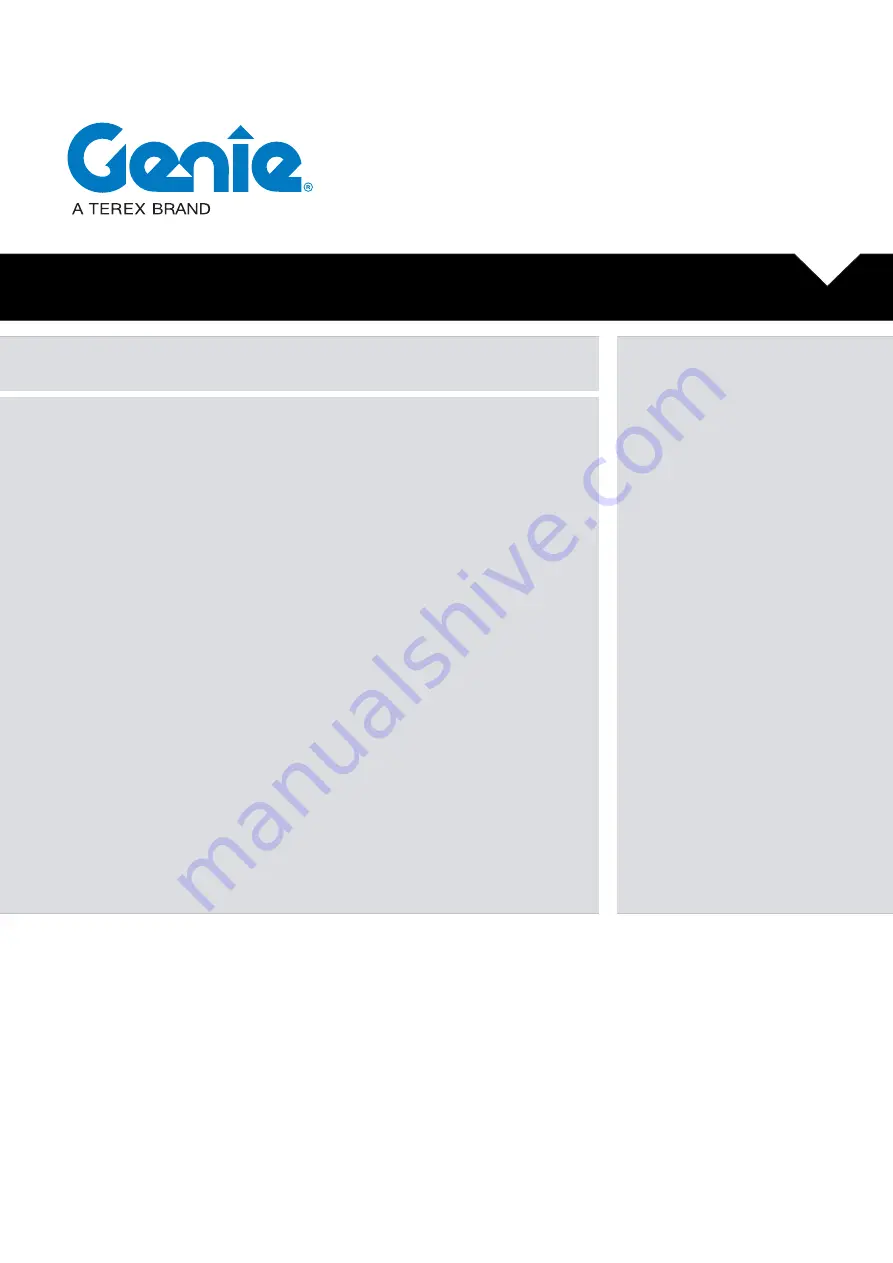
1.
Service and Repair Manual
Serial Number Range
GTH-1256
(Perkins Tier 4i)
From GTH1215M-101 to
GTH1216M-249
GTH-1256
(Deutz Tier 4i)
From GTH12M-250 to
GTH12M-280
Part No. 1272856
Rev A1
September 2016
This manual includes:
Repair procedures
Fault Codes
Electrical and Hydraulic
Schematics
For detailed maintenance
procedures, Refer to the
appropriate Maintenance
Manual for your machine.
From GTH1215M-101 to
GTH1216M-249
From GTH12M-250 to
GTH12M-280