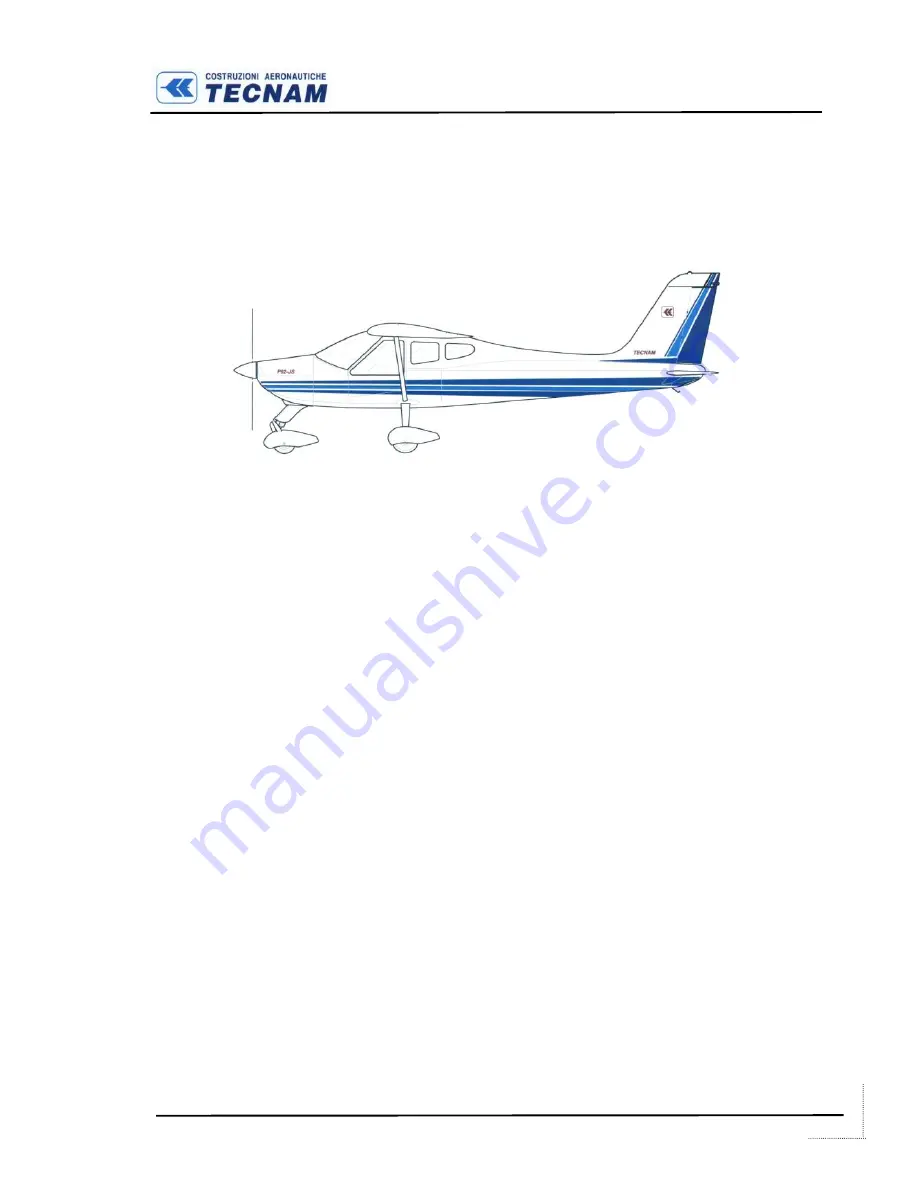
P92-JS
I N TRODUCTI ON
F
LIGHT
M
ANUAL
Date
:
Issue 3, 25
th
May 2010
i-1
FLIGHT MANUAL
Doc. n° 92/61 Issue n°3: 25
th
May 2010
Revision No.0
P92-JS
M
ANUFACTURER
:
COSTRUZIONI AERONAUTICHE
TECNAM
S.r.l.
A
IRCRAFT MODEL
:
P92-JS
T
YPE CERTIFICATION
: n° EASA A.412 (SO/A-340)
S
ERIAL NUMBER
:
............................................................….....
B
UILD YEAR
:
..............................................................…….....
R
EGISTRATION MARKINGS
: .......................................................
This manual contains information to be furnished to the pilot as required by EASA
in addition to further information supplied by manufacturer.
This manual must always be present on board the aircraft.
The aircraft is to be operated in compliance with information and limitations
contained herein.
Sections 2, 3, 4, 5 are approved by EASA: n° 10030344 on 11.06.2010
Section 9 (supp.1) is approved by EASA: n° 2004-1787 on 02.03.2004
Section 9 (supp. 2) is approved by EASA: n° 2004-6324 on 17.06.2004.
Section 9 (supp.3) is approved under DOA privileges: n° MOD92/51.10.06.2009
Section 9 (supp.4) is approved under DOA privileges: n° MOD92/52.10.06.2009
Section 9 (supp.5) is approved under DOA privileges: n° MOD92/53.10.06.2009