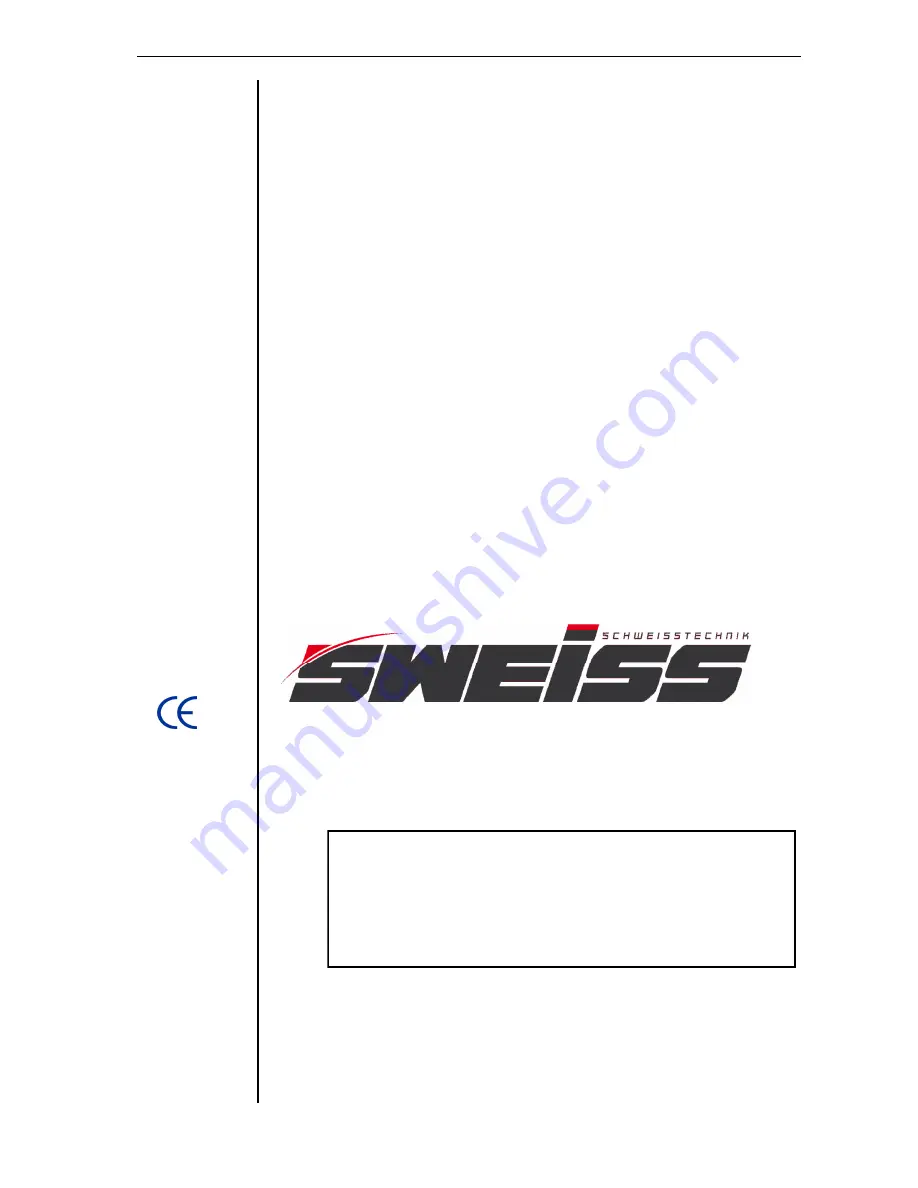
INTRODUCTION
I
ISO9001:2000
2012
.
09
SKY
ARC
ULTRA 31
40
Inverter DC MMA Arc Welding Machine
IMPORTANT:
Read this Owner’s Manual Completely
before attempting to use this
equipment. Save this manual and keep it handy for quick reference. Pay particular
attention to the safety instructions we have provided for your protection. Contact your
distributor if you do not fully understand this manual.
OPERATORS’ MANUAL
Summary of Contents for SKYARC ULTRA 3140
Page 3: ...CONTENT III ...
Page 27: ...MAINTENANCE AND TROUBLESHOOTING 20 5 3 Electrical principle drawi ...
Page 28: ...NOTES 21 ...
Page 29: ...NOTES 22 ...
Page 30: ...NOTES 23 ...
Page 31: ...NOTES 24 ...